Maintaining your business’s equipment is essential for ensuring that it continues to run smoothly and efficiently. However, crafting a maintenance strategy is not a cut-and-dried process. Not only do you have to sort through manufacturer-recommended maintenance, but also there is a growing list of maintenance types and tips to go with them. Without the proper tools in place, it is difficult to keep track of what you have and ensure that you always have the necessary items on hand when you need them. That’s where maintenance inventory software comes in. This type of software can make it easy to manage your inventory, track usage, and order supplies when needed. Here we’ll take a look at why every business should consider using maintenance inventory software, and explore some of the benefits this type of tool can provide.
What is Maintenance Inventory Software?
There are general inventory management systems that retail businesses use, but that isn’t sufficient for managing maintenance inventory. Instead, maintenance inventory software integrates with your maintenance management. This software is typically a part of Enterprise Asset Management (EAM) software or a Computerized Maintenance Management System (CMMS).
The issue with using a basic inventory software for your spare parts is that you create a data silo. This means that all of the information is not in the same system. You likely have software or a system in place to handle your maintenance, work orders, and assets. So, the inventory that keeps all of those things running smoothly should be in the same system for the most efficient operation. Redlist’s maintenance inventory software is included in the EAM/CMMS offering and allows you to track your parts, products, and tools all in the same platform as the rest of your maintenance.
Why Do You Need Maintenance Inventory Software?
Maintenance inventory software streamlines your maintenance operations. One key element of maintenance inventory management is inventory control. Stocking the right amount of spare parts and materials is vital to keeping your maintenance operation running smoothly. However, too little inventory can result in downtime due to missing parts, while too much inventory ties up capital that could be better used elsewhere. Managing this on paper or with spreadsheets requires far more manual labor hours and leaves a greater room for error, especially if you have inventory across different locations or in the field. Maintenance inventory software can help you strike the perfect balance by providing visibility into your current levels of inventory and demand patterns. This way, you can make informed decisions about ordering new parts and stocking levels.
In addition to inventory control, maintenance inventory software can also help you save time and improve productivity through automation. By automating tasks like stock level alerts, parts requests, and reporting, you can free up your staff to focus on more important tasks.
Save Money with Maintenance Inventory Software
Digitizing your maintenance inventory can help you save money as well. By avoiding stockouts, minimizing excess inventory, and reducing paperwork, you will see reduced maintenance inventory costs. As a result, maintenance inventory software can help you optimize your entire maintenance operation and improve your bottom line.
- The average cost of storing spare parts ranges from 12% to 20% of the purchase price. This is called your “carrying cost”.
- Stockouts result in expensive equipment downtime and unnecessary rush shipping expenses.
- A study found that 50% of unscheduled downtime annually is caused by a lack of the necessary spare parts.
- Maintenance technicians spend an average of 10% to 25% of their time finding the parts they need to get their work done. When every minute of downtime counts, the cost of an unorganized maintenance inventory adds up.
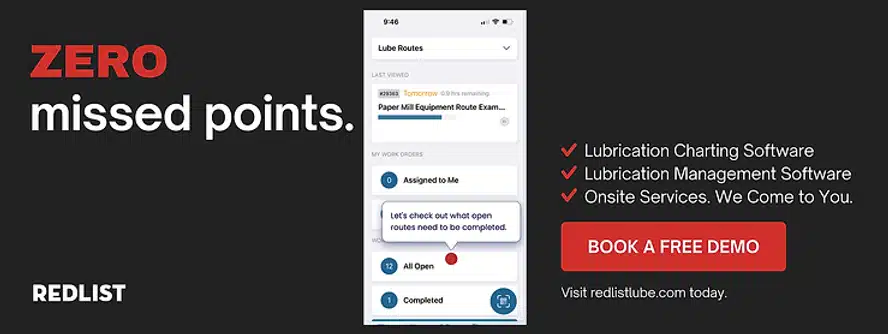
Improve Your Spare Parts Inventory with Redlist
Redlist helps you remove the guesswork from your inventory management. Our EAM/CMMS software includes a fully integrated purchasing and inventory platform with the features you need:
- Automated Min Max Alerts
- Assign Products for Increased Accountability
- Automated Purchase Order Creation
- Item Images
- SKU and Parts Numbers
- Multi-Location Inventory
- Costing
- Vendor Management
- Saved Part Alternatives
- Multi-Level Categories
- Part Locations by Row, Shelf, and Bin
- Add Sales Markup
Maintaining a stock of spare parts and equipment is critical for any business that wants to avoid costly downtime. But tracking and managing this inventory can be difficult, especially if you have multiple locations. Our software helps you do more than just keep track of your parts and equipment. One Redlist user started with the intention of gaining better visibility into their inventory management and ended up recovering $131,000 of employee theft. Our team would be happy to walk you through the software and explain the benefits specific to your business. Schedule a demo today to explore our maintenance inventory software features.