Assigning access to your computerized maintenance management system (CMMS) is critical to its success. Identifying who can use the software helps ensure its efficient operation and positive impact on your business. Granting access to the wrong people or letting too many personnel use this software system often results in inaccurate data, safety failures, overspending, and other undesirable outcomes.
In this article, we look into users and levels of user access and discuss the top 10 key users in your organization. And from this, you’ll also learn how to identify the people who don’t need to access your maintenance management software.
What is a CMMS User?
A CMMS user can be anyone in the company who is qualified to provide the essential data the system needs. Your users should also have the proper training and adequate experience in using the system.
The software comes with different levels of access to the system that you can assign to each user. And each level has specific features, viewable data, and a level of control. Understanding the different levels of access in a CMMS allows you to assign the ideal access to each user in your organization.
CMMS Users and Levels of Access
CMMS software has different levels of access to guarantee the accuracy of data and efficiency of executing the maintenance program. When setting up your software, knowing your objectives and procedures is critical. Discussing these details with your software provider will help gather suggestions and recommendations to identify these access levels and optimize your CMMS.
The number of active users you assign also determines the price of your software. Knowing the number of users you need allows you to get a reasonable price for your software, thus letting you get the most out of your investment.
The levels of access in a CMMS can also differ depending on the size of the operation or company. A small company can have one person access to all maintenance tasks, while a large company can assign a user to manage repairs or operations only.
Lastly, the use of CMMS is not limited to people who can access the system. The ideal CMMS should allow personnel to submit, track, search, and sort maintenance information in its database without logging in.
The 10 Key Users of CMMS Software
Below are the personnel who should have access to your CMMS and their appropriate levels of access.
1. Facility Manager and/or Operations Manager
Maintenance is essential to the operation of a production facility. Facility managers and operations managers must therefore have access to your CMMS. They must be able to view maintenance data, metrics, schedules, and performance across several locations to increase productivity, plan for audits, calculate budgets, purchase inventory, and more.
2. Maintenance Manager or System Administrator
Being the overseer of all maintenance processes, the maintenance manager or system administrator should be the core user of a company’s CMMS. They are the daily users of the software and are extensively involved in selecting, integrating, and optimizing CMMS. The maintenance manager must have administrative access to the system because they are responsible for the majority of maintenance tasks, such as creating, scheduling, and prioritizing work orders, managing assets, and generating reports.
3. Inventory Manager
Involved in managing resources, the inventory manager needs to access your CMMS to log information on spare parts, view historical data, establish minimum quantities, and submit purchase requests. From this, the system can improve inventory management and purchasing, ensuring that the maintenance team has the appropriate components for every job in the correct quantity and location. The inventory manager’s effective use of CMMS can also lead to more accurate records on stocks and expenditures, resulting in improved departmental cooperation.
4. Reliability Engineer, Technical Program Manager (TPM), and/or Continuous Improvement Manager
These engineers and managers work with data collected and stored in your CMMS. They need access to retrieve these data, crunch the numbers, analyze the results, and produce actionable information. Also, they should have administrative access to the CMMS to work with analytical tools, run reports, and build processes that can reduce downtime, increase efficiency, and reduce costs.
5. Health and Safety Personnel
Health and safety are essential to reduce accidents, pass audits, and maintain compliance. Granting administrative CMMS access to health and safety personnel allows them to organize all health and safety data, such as certifications, policies, checklists, and audit findings, in one system. Allowing this access is a beneficial strategy to lower workplace safety concerns and ensure that the company stays compliant.
6. Production Personnel
This includes personnel who use the machines and equipment daily, such as line supervisors and machine operators. Production personnel should also have access to your CMMS because they can spot early warning signals of failure and are present when a breakdown occurs. Through CMMS, production personnel can submit requests or provide additional information to work orders, allowing the early identification of problems and speeding up the repair process. A CMMS also makes it possible to assign essential maintenance responsibilities to operators. These responsibilities include cleaning and maintaining the health of the equipment, thus saving time and freeing up technicians for other more complex or technical tasks.
7. Technicians
When implementing CMMS, technicians are indispensable. They are the employees who will perform most maintenance tasks, after all. A technician’s level of access to CMMS need not be administrative. Still, they should be able to examine work orders, get alerts, add details to asset profiles, and do other duties necessary for the repair and inspection process. With CMMS, technicians can log data in real time while being effective, safe, and precise.
8. Contractors
Guest access to your CMMS can also be granted to contractors and independent technicians. This access allows third-party affiliates to view work orders, task lists, and resources while also being able to add notes and complete tasks. As a result, the company will benefit from a faster and more efficient process of availing and recording external services.
9. IT Department
The IT department manages the whole digital infrastructure of your business, including the CMMS. Granting your IT staff access to CMMS lets them keep an eye on any integrations, software updates, data storage, and security duties carried out by the software provider, ensuring proper regulations and procedures are followed.
10. Senior Leaders and Executives
Access to your CMMS gives senior leaders and executives information to make educated decisions and the right corporate choices. CMMS can provide these decision-makers with the performance of the maintenance operation, any significant accomplishments, challenges, and key performance indicators (KPIs). Limited access should be enough for your senior leaders and executives, as they don’t need to use CMMS frequently.
Who Doesn’t Need to Access Your CMMS?
Individuals not included in the list above will not likely need access to your CMMS. Employees with minimal contact with the production or maintenance departments don’t need to work with your CMMS. The cost and effort of providing access and training to these employees would outweigh the benefits. Also, some departments, accounting, for example, may require access to CMMS for purchases and stock control. In cases like this, CMMS integrations allow other departments to use CMMS data without accessing and modifying the main CMMS processes.
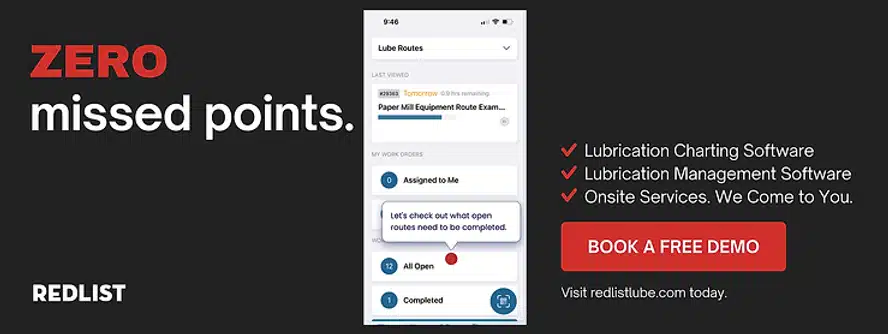
Optimized CMMS Access
The success of your CMMS implementation is supported by optimizing user access. Optimized access happens only when the right users are assigned, and if they use the system correctly and regularly. Therefore, you need a CMMS like Redlist that is user-friendly, adaptable, intuitive, and integration-friendly. All these qualities ensure optimized access for every level of access and every CMMS user’s skill and knowledge. If you’d like to learn more, schedule a demo with a member of our team today!