Establishing a reliability culture is a key component of your maintenance plan. So, what exactly is it? It is the collective mindset and approach within your company regarding asset management, maintenance, and reliability. The goal is to increase asset availability through decreasing equipment failure. As a result, you experience a safer workplace and increased productivity. However, all of this is still a bit vague when it comes to implementing a plan to develop a reliability-focused culture.
3 Main Aspects of Reliability Culture
First, empowerment of employees to take ownership of the assets they work with daily. That means operators are more involved with simple routine maintenance and identifying equipment issues. After all, operators use this equipment every day and likely know it better than anyone else. Next, the maintenance team’s role shifts more to be “on-site specialists”. They are essential to ensure assets are available and operating properly to meet production. Finally, every employee who interacts with the assets provides input for asset design and maintenance. These three elements will shift your company culture to be more reliability-focused.
How to Know if You Could Benefit from Reliability Culture
You could say that any company that relies on assets would benefit from a reliability culture. But, if this is a new concept or you are already working on it, these are the issues to watch for:
- General struggles with maintenance and asset productivity
- Inefficient maintenance workflow and reporting
- Potential safety issues from equipment breakdown
- Maintenance tasks are primarily reactive maintenance
- Unable to achieve maintenance goals or hit key performance indicators (KPIs)
- High downtime
- Large maintenance and overtime expenses
- Quality control issues
Obstacles to Creating a Reliability-Focused Culture
Reliability culture is dependent on everyone helping to carry the weight of asset management. So, if your information or communication is siloed, then your culture will suffer. Silos often show up around departments or data. This means your maintenance data may be in one software or spreadsheet, but your operations or accounting teams use different software or spreadsheet. Or, your operators have insights on assets that aren’t communicated to your maintenance technicians because there isn’t an established system of communication. Maintenance, operations, and the administrative staff all need to be working from the same data and be able to communicate easily. Redlist’s Enterprise Asset Management (EAM) software ensures you eliminate organizational silos.
The other critical component of a reliability culture is to ensure you have buy-in and engagement from everyone. You can present the benefits of a reliability culture to company leadership to get them on board. Once you have buy-in from management, you can create a plan that engages everyone from operators to maintenance. Implementing a reliability culture requires making everyone aware of why the changes are necessary and how to do their part. It is important to provide the reasoning behind the change because you need to motivate your team to adopt the new processes.
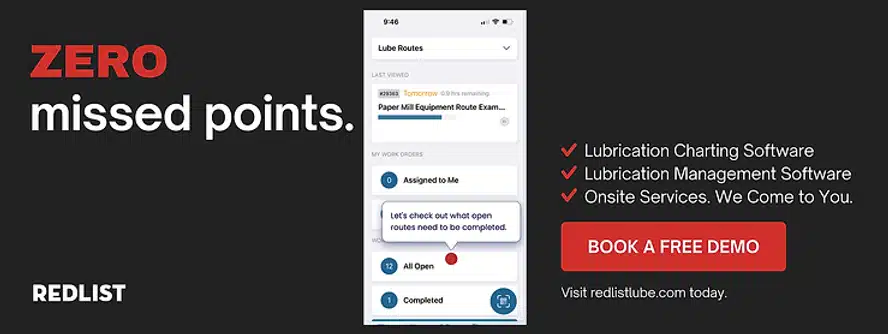
Plan, Implement, Measure, and Revise
Once you have a plan and implement it, it is important to measure your progress. Culture is a rather subjective thing, so it is essential to establish KPIs that will track the growth of your reliability culture. This is where EAM software enters the equation again, as it is helpful to streamline the collection of data and reporting measuring your KPIs. Redlist auto-populates your reporting dashboard with your real-time information, which enables you to revise your reliability culture plan based on current data. That is key to moving your plan forward and seeing the real impact of reliability culture on the business.
While it does take work to shift your company culture and cultivate a reliability culture, the benefits are worthwhile. Increased uptime and productivity, a safer workplace, and a culture of collaboration and teamwork to maintain your assets are only a few. Just as your reliability culture plan will be custom to your company, you will experience your own unique combination of benefits. As long as you implement, measure, and revise, your reliability culture will grow along with your employees and your business.