When it comes to asset reliability and productivity, there is a lot of talk about downtime. However, there’s a very important distinction to make when measuring your downtime. That distinction involves determining what is idle time and ensuring that you don’t include it in your downtime. Even though they are similar, idle time and downtime are not the same. So, what is an idle time? Idle time, also known as waiting time, is any time that a machine or employee could be working but is not, due to waiting on something. Alternatively, downtime is when a machine or asset cannot produce because of equipment breakdown and unplanned maintenance. To calculate your idle time, you can use this equation:
Idle Time = Scheduled Production Time – Actual Productive Time
What Causes Idle Time?
The main difference from downtime is the cause. Downtime is the result of an unplanned asset breakdown. Idle time can be a result of many other factors, including:
Process Inefficiency
Production or other process inefficiencies may show up in different ways, such as when a machine is waiting for materials. Other inefficiencies could be a backlog of approvals needed to move work ahead, technicians waiting for tools or parts to be available, or even lack of detail on a work order causing extra trips to the storeroom.
Employee Inefficiency
Employees cannot be 100% efficient in a workday. However, there may be inefficiencies from distractions in the workplace or inadequate training. You can reduce non-productive time by improving training or onboarding and making sure you resolve workplace distractions.
Unexpected Personal Events
Your employees have a life outside of work, so it’s natural that the two can affect each other. Personal calls, texts, or even an employee simply being stressed about a personal matter can cause idle time. Your managers can be understanding and supportive, but still address this kind of idle time constructively. This becomes a bigger problem to address if their personal matters distract them from work in a way that threatens workplace safety.
Natural Disasters or Storms
This one is almost entirely out of your control. If a storm causes a power outage or the internet goes down, your machines or employees will have idle time. While you can’t prevent storms or natural disasters, you can plan for them like having generators to operate essential assets or offline functionality for your digital resources. Companies with a fleet that delivers products or services to clients may have a large amount of idle time due to road conditions caused by weather.
Accidents
In the event of a workplace injury, equipment may be shut down and production put on hold while you fill out the accident report or remedy the situation. This creates waiting time for the equipment and other employees. The only way you can prevent this is with a strong safety program.
How to Reduce it
Determine the Root Cause
The first step to reducing idle time is to figure out the root cause. When it comes to your employees, you want to foster a positive, healthy work environment. This means being understanding of personal matters and ensuring they take the necessary breaks in their day. If you rely on mobile devices for software and are concerned about the distractions of social media or online videos, you can implement a Mobile Device Management (MDM) to support your employees by blocking distracting apps. You cannot eliminate all employee idle time, but you can reduce it depending on the cause.
On the other hand, you can greatly reduce machine idle time. But, you must keep in mind any limitations of various equipment. For example, idle time may allow temperatures to cool down and remain in an optimal operating zone. This is why a root cause analysis is the first step. It will provide the information you need to determine if you even go to step two.
Address the Issue
There are many things you can do to reduce idle time. Optimizing your workflows and processes is an excellent place to start. This could be anything from removing bottlenecks in approvals to rearranging equipment to create a better production flow. Additionally, you can provide more resources for your employees. This may be more training for new hires, checklists to support inspections or maintenance, or improving the detail of your work orders or service tickets.
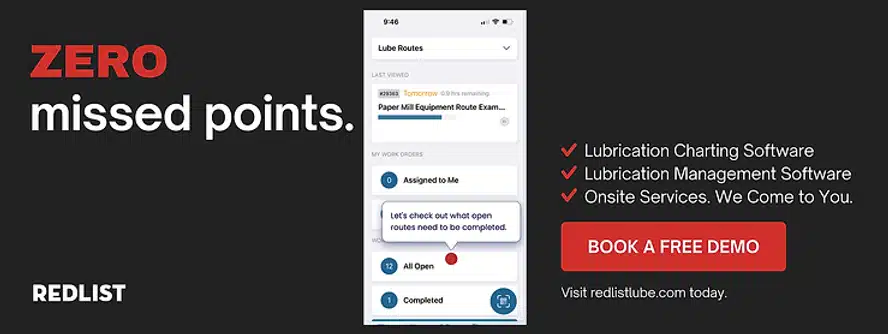
Why You Should Track Non-Productive Time
While you can’t eliminate idle time, you can reduce it. Reducing non-productive time increases productivity, which helps your bottom line. However, that means you have to track idle time to know where to begin with reducing it. If you lump idle time in with equipment downtime, you will throw off your maintenance metrics, as idle time is not maintenance-related. It is best that you track both of these separately, especially if you want to work toward reducing them. Redlist’s Enterprise Asset Management (EAM) software can support you in tracking all of your maintenance and business operations’ metrics. Schedule a demo to learn more about how the software can help you gain visibility into your operations.