Grease and oil may seem like similar substances, but they have very different characteristics and purposes. It is thick and viscous, while oil is thinner and less sticky. Industrial greases are important for lubricating moving parts and preventing wear. But what is grease, and what makes it so effective? This article will explore the properties that make it a valuable industrial lubricant. Understanding the various qualities of lubricants can help you choose the right substance for your equipment’s lubrication needs.
What is Grease and Its Components?
It is an oil-based product composed of lubricant and thickener that comes in solid to semi-fluid forms. The specific liquid lubricants and thickeners are used to define its basic properties.
It components are as follows:
- 70-90% Base Oil
- 1-10% Additives
- 5-20% Thickener / Soap
The base oil and additive package heavily influence a grease’s behavior. Furthermore, these are the most important ingredients in grease formulations. In many cases, you may hear the thickener referred to as a “sponge” that holds the base oil and additives.
Grease consists primarily of oil, which the thickener traps to make the final product stiffer or denser. Base oils include synthetic fluids and mineral oils. While mineral oil is the most common base, synthetic bases are best for extreme temperatures. The thickener does not provide any lubricating properties. That all comes from the oil and additives. Despite this, thickeners do affect their performance and application suitability.
When to Use Grease Instead of Oil
You cannot interchange oil and grease. Whenever oil is not practical or convenient, you must use grease instead. You will typically make this decision based on the design of the machinery, operating conditions, and the desired lubricant characteristics.
In general, you can use it for:
- Frequently restarted machines or machines stored for long periods. The grease remains in place, allowing a lubricating film to form instantly.
- Inaccessible machinery that needs frequent lubrication. You can lubricate inaccessible or isolated components for long periods using high-quality greases. Also, some electrical motors and gearboxes are sealed for life and use these greases.
- Excessive conditions include high temperatures, high pressures, shock loads, and slow speed and heavy loads.
- Components that are worn out. It can extend the life of worn parts that were previously lubricated with oil because it maintains thicker films in clearances that have become larger due to wear.
How Grease Serves Your Lubrication Management
First and foremost, you can use grease as a sealant. This proves incredibly useful to minimize leakage and keep contaminants out. It has a high cohesive strength, which acts as a sealant to prevent leaks of lubricant as well as to prevent the entry of foreign materials and corrosive contaminants. Additionally, it can extend the life of deteriorating seals by aiding in keeping them effective.
Another major benefit of grease is how it suspends solid lubricants. Graphite and molybdenum disulfide (moly) are finely ground solid lubricants. For high temperatures or high-pressure applications, they are mixed with it. Solid lubricants will settle out of oils, while grease will hold the solid lubricants in suspension.
What is Grease in Terms of Viscosity?
Grease’s lubrication function mostly comes from the base oil. So, the viscosity of the base oil is still a very important factor. It’s viscosity levels and applications are as follows:
- ISO 100 and lower: Best for higher speeds >3600 rpm, lower loads, and lower temperatures.
- ISO 150/220: Best for moderate speeds of up to 3600 rpm and can carry a decent load. This is the viscosity of most multipurpose greases.
- ISO 460: Greater load capacity than ISO 150/220, and with the bonus of higher water resistance.
- ISO 1500: Best for lower speeds under 100 rpm, high water resistance, and good load carrying capability.
Common Grease Additives
Lubricating grease contains several additives, with the key functions including:
- Improving existing desirable properties.
- Eliminating or reducing undesirable properties.
- Establishing new properties.
Anti-wear, oxidation and rust inhibitors, extreme pressure, and friction-reducing agents are the most common additives. Additionally, boundary lubricants such as molybdenum disulfide or graphite may be suspended in grease to cut friction and wear while minimizing chemical reactions between the grease and metal surfaces during certain conditions.
Does the Thickener Impact the Grease’s Lubrication?
While the thickener does not impart any lubricating qualities, it can impact various grease characteristics. A grease thickener affects the following aspects:
- Optimal Temperature Range
- Pumpability
- Water Resistance
- Mechanical Stability
What is Grease: An Intro to Thickeners
There are two types of thickeners, a soap-like base that is chemically similar to soap and a non-soap base. Currently, metallic soap is the primary thickener you will see in it. However, complex thickener-type greases have become increasingly popular in recent years due to their high dropping points and great load-carrying capabilities.
Around 11% of greases on the market consist of polyurea, organophilic clay, and other non-soap greases. The rest have a soap thickener. For reference, if the thickener name ends in “-ium”, then it is a soap thickener. About 68% of it is available in North America and contains lithium or lithium complex. But, there are four common kinds: lithium, calcium, sodium, and aluminum.
If you need grease with the best water resistance, barium and aluminum complexes are the most effective. Sodium, on the other hand, has the least water resistance. Polyurea is well-suited for electric motor bearings. Additionally, many non-melting high-temperature greases use organophilic clay.
Nonsoap thickeners are also becoming more and more common in specialized applications, like high-temperature environments. Examples of thickeners that do not melt at high temperatures are bentonite and silica aerogel. However, there is a misperception that comes with high-temperature thickeners. While the thickener may be able to resist the high temperatures, the base oil will oxidize quickly and necessitate frequent relubrication.
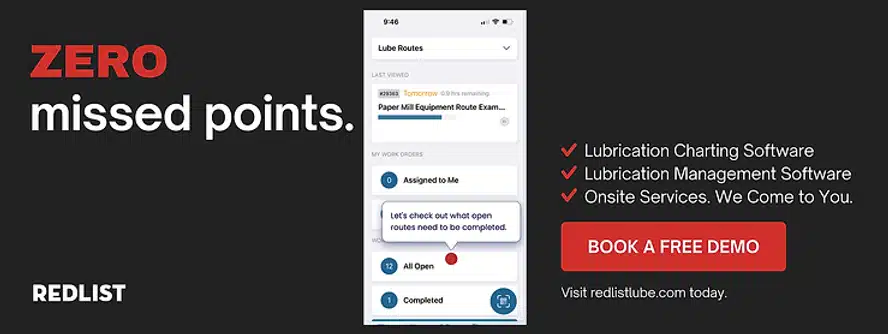
The Right Lubricant Makes a Difference
Grease has a unique set of traits that you must take into account when choosing it for a particular application. It can lubricate moving surfaces and stay in contact with them without seeping out due to pressure, centrifugal forces, or gravity. The main practical need for it is that it must maintain its characteristics when subjected to shear forces at all operating temperatures. You can ensure that your facility is performing at its best by including the right grease in your lubrication management plan.