Industries that depend on equipment, machinery, vehicles, or other assets rely on maintenance to keep those assets, and the business, running. Without proper maintenance, assets break down unexpectedly, which halts production. On top of the cost of repairs, unplanned equipment downtime has an hourly cost. For example, one minute of unplanned downtime costs vehicle manufacturers $22,000. That’s over $1.3 million per hour of downtime. Keeping up with maintenance is essential, which is why you must track your backlog maintenance.
What is Backlog Maintenance?
Backlog maintenance is your accumulation of incomplete maintenance work. It is typically expressed in a measure of time, such as minutes, hours, days, or larger depending on your amount of backlog. A simple example of backlog maintenance is fleet management. Let’s say you have a fleet of commercial vehicles that all come due for their regular oil change the same day. You only have two technicians that you can assign to the oil changes, and it will take them 5 business days to complete all of the work. You would have a 4-day maintenance backlog. However, this is an oversimplification for this example. Your actual measurement of backlog maintenance might feel more overwhelming. It may not be as easy as this example to add up all the overdue corrective or preventive maintenance and inspections for all of your assets.
The Trouble with Backlog Maintenance
For starters, the longer a task sits in your maintenance backlog, the more likely it is to lead to equipment breakdown. That’s because you plan these inspections and preventive maintenance tasks to keep your assets operating smoothly. So, neglecting them for too long creates the opportunity for your assets to breakdown. It’s expected to have some backlog, but you have to determine your threshold between acceptable and too much.
Furthermore, your goal doesn’t have to be total elimination of backlog. Your goal should be to know your backlog maintenance metric and have an ongoing plan for how to handle it. That plan will be different for every business and will evolve with time. For instance, unplanned equipment breakdown can pull your technician resources away from preventive maintenance to handle emergency repairs. If your backlog grows past your acceptable level as a result, then you’ll need to adjust your plan to tackle the excess after your emergency repairs are done. Otherwise, your backlog will continue to grow and can spiral out of control quickly.
Total Backlog vs. Asset-Specific Backlog
To make strategic business decisions, you will want to know your total backlog and asset-specific backlog. Your total maintenance backlog is an excellent measure of your overall maintenance operations. However, if the majority of your backlog is associated with critical assets, then you have a higher risk of expensive, unexpected downtime. If the majority of your backlog is on low-risk assets that aren’t mission-critical, then it’s less likely to cause a serious problem.
How to Reduce Your Backlog
As the saying goes, “You can’t manage what you don’t measure.” So, how do you measure your maintenance backlog? First, you need a system for tracking the data. While you can try to manage with paper and spreadsheets, it will be a time-consuming and tedious process to track. Instead, we recommend Enterprise Asset Management (EAM) software. An EAM is perfect for digitizing and even automating your maintenance plan, which helps many companies finally achieve their preventive maintenance goals. But also, our EAM enables you to have visibility into your data and pull real-time reports. This is necessary for reducing your backlog of maintenance because you can understand your:
- Total Maintenance Backlog
- Asset-Specific Backlog
- Downtime Costing
- Asset Health
- And, even your Total Cost of Ownership.
With this visibility into your assets’ health and maintenance data, you can determine how much backlog you have, what is acceptable, and how best to manage it.
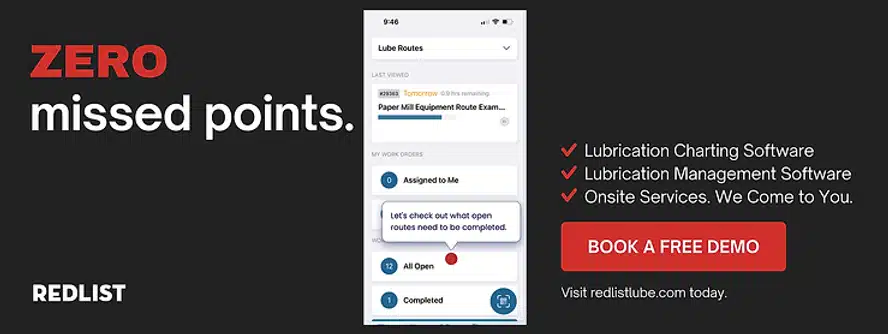
Tackle Your Backlog Maintenance with Redlist
Understanding your backlog and working to reduce it not only benefits your assets but also your entire maintenance operations. When you have accurate data to measure backlog maintenance, you may discover workflow or process inefficiencies that are the root cause of your backlog. Or, you may realize a pattern of a specific asset breaking down unexpectedly and often that is causing your growing backlog. And, the benefits of tackling your backlog with EAM software don’t end there. Every improvement that you make reduces costly equipment downtime, increases production, and even saves on inventory and repair costs.