Creating a lubrication route or a lubrication management plan is one thing, but maintaining it is another. Once you do the initial setup, you may find yourself wondering what can you do to maintain your lubrication system. If you have a system, then you already know that it is crucial to the overall health of your business. So, by taking proper steps to care for your system, you can ensure that it runs smoothly and efficiently. Here are some tips and best practices to maintain your lubrication system.
Actively Preserve Fluid Cleanliness
Your lubrication system is only as strong as the weakest link. While application, storage, and the schedule are important, you could ace all of those and still have problems if your lubricant is contaminated. So, the number one action to maintain your lubrication system is to maintain your lubricants. From storing to dispensing and applying, there are several best practices to proactively protect your fluids. The key is to reduce or completely avoid any conditions that put stress on the lubricant. That includes maintaining a consistent temperature, storing in a dry place, proper ventilation, and clean containers, dispensers, and applicators. Furthermore, realizing that new oil is typically not clean and ready for use is helpful. An affordable fix for that is to dispense your bulk stored lubricant through high-quality filters to catch any contaminants before they go into your equipment.
Make Lubrication Routes as Easy as Possible
Lubrication charting and route planning should include a high-level view of efficiency. If your technicians need different tools, lubricants, and paperwork for the assets on their route, they will spend unnecessary time switching out supplies between assets. Instead, do your best to arrange routes by grouping similar tasks as much as possible. Additionally, no lubrication system is complete without regular inspection and analysis. But, for the most sustainable plan, make your lubrication inspections simple. Group the inspection routes similar to the lubrication routes. Also, you can adjust your inspection checklist and questions to be quick yes or no answers. This is a great opportunity to explore a CMMS (Computerized Maintenance Management System) to support your technicians and inspectors on their routes.
Check Your Metrics
Data provides visibility into your assets and their health. As with any maintenance strategy, you can check your metrics for insight about the impact of your lubrication system. Ideally, a great lubrication plan will maintain or improve equipment performance and productivity. So, if your performance metrics take a dip, then you can perform a root cause analysis to determine the cause. It could be an issue with your lubrication plan, or it could be something else. Either way, your organization will be better off because of your data.
Perform Oil Analysis
Oil analysis is a strategy employed by world-class lubrication plans. However, you may want to optimize every step of your process before you invest in oil analysis. There are simple things like filtering new oil and ensuring lubricant applicators are clean that really should be done first. Once everything else is running like a well-oiled machine, oil analysis is a great resource for continuous improvement. Also, oil analysis can greatly reduce your lubricant costs. For example, say you have a machine that costs $5,000 to change the oil due to the large volume. You change it after 500 operating hours per the OEM (original equipment manufacturer) recommendation. After implementing oil analysis, you discover that the oil is still good at 500 hours, 600 hours, 700 hours, etc. Now, you can double the time between oil changes to 1000 hours, which cuts your lubricant cost in half for that machine.
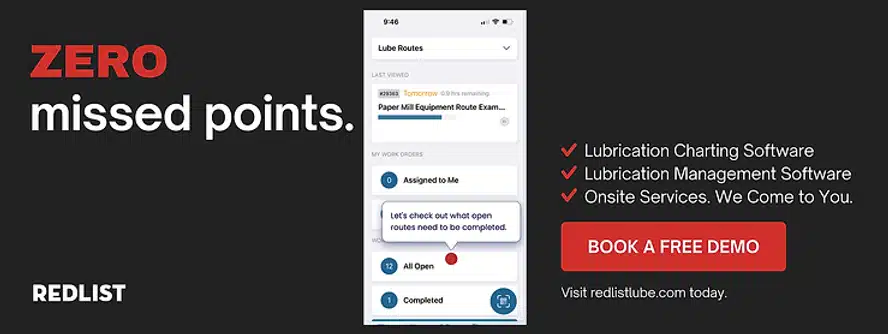
The Bottom Line on What Can You Do to Maintain Your Lubrication System
When asking what can you do to maintain your lubrication system, the answer isn’t to switch lubricants or buy the most expensive one. The best lubrication systems aren’t the ones that just purchase premium lubricants. In fact, poor lubrication practices using premium lubricants will severely increase costs long term. Investing wisely in quality lubricants, education, analysis, and best practices will provide you with higher returns on investment. Furthermore, there are several industry experts in this space to support you and your team in the creation, implementation, and maintenance of your lubrication system. Then, you can have peace of mind knowing that everything from oil analysis procedures down has been carefully planned out by an expert team who knows what works best under different conditions.