Condition monitoring is an excellent practice for organizations of all sizes. By incorporating condition monitoring into your maintenance routine, you can optimize equipment performance, identify and prevent potential failures, and extend the life of your valuable assets. By identifying potential problems early on, businesses can avoid costly repairs and downtime. In this blog post, we’ll explore the advantages of condition monitoring and how it can help your business run more smoothly.
What is Condition Monitoring?
To understand the advantages of condition monitoring, it is important to have a clear definition and know your variety of condition monitoring options. The goal of condition monitoring in maintenance is to prevent asset failures, downtime, and even unnecessary maintenance. By monitoring equipment health, you can better determine what maintenance you need to perform and when. In fact, a predictive maintenance strategy is not complete without condition monitoring. Additionally, condition monitoring drives condition-based maintenance. Both of these maintenance strategies involve planning maintenance only when conditions pass certain thresholds or indicators indicate that failure is imminent.
There is a key difference between condition monitoring and traditional asset monitoring. It is common to have predetermined intervals for non-invasive measurements, visual inspections, performance data, and scheduled tests. However, with condition monitoring, you create a plan according to your equipment’s potential failure modes and their indicators. Then, sensors provide a continuous method of testing and tracking asset health, which generates real-time data.
The Different Types of Condition Monitoring
There are many different ways to monitor asset health. The most common options are:
- Vibration Analysis – Worn components can cause vibrations that indicate developing flaws and potential breakdown.
- Oil Analysis – This involves analyzing lubricants to determine their condition and to provide information about equipment conditions.
- Temperature Measurements – These include simple temperature measurements as well as more advanced methods like thermography. Thermography reveals any areas of excess heat or thermal anomalies, which are often indicative of lubrication problems, worn parts, or misalignment.
- Acoustic Analysis – The two main types of acoustic analysis are ultrasonic and sonic. Sonic analysis uses microphones to monitor proper lubrication. Ultrasonic analysis is more in-depth, as it measures sounds that are beyond human hearing abilities.
- Motor Circuit Analysis – This process looks for electrical imbalances and degradation of insulation in a motor to determine its overall health and prevent failure.
- Electrical Monitoring – This can cover a variety of characteristics, including induction, pulse and frequency response, capacitance, and resistance.
- Electromagnetic Measurement – This measures distortions in the magnetic field and current fluctuations to determine if there are any issues.
- Radiation Analysis – Radiation imaging of equipment is similar to an x-ray at the doctor’s office. But, instead of broken bones, it inspects for internal flaws, like corrosion. It is one of the most thorough non-destructive testing methods
- Laser Interferometry – By measuring wave displacement of laser beams, this can detect issues on the surface and subsurface of materials.
Unexpected Advantages of Condition Monitoring
Condition monitoring and predictive maintenance set themselves apart from preventive maintenance (PM) through the timing of repairs. It’s all about scheduling maintenance precisely when it is needed, which is not too early or often and not too late or infrequent. This process works by detecting signs of upcoming failures far enough in advance to schedule maintenance at just the right time to avoid equipment breakdown.
Preventive maintenance depends on doing specific tasks on a predetermined schedule. Typically, you would schedule maintenance according to equipment use, time, or a combination of the two. You might replace one component every six months or change oil every 10,000 cycles, for instance. With strictly preventive maintenance, you stick to the schedule regardless of how much life the lubricants or parts still have.
However, the advantages of condition monitoring include knowing how much life those components have left and using every last bit of it! This is a vital practice for keeping your maintenance budget in check and making the most of your inventory in times of supply chain issues. Furthermore, only performing maintenance when it is actually necessary guarantees the equipment’s maximum uptime. In general, condition monitoring increases the intervals between maintenance shutdowns because maintenance is only performed when it is necessary, which has the potential to reduce maintenance costs.
Common Advantages of Condition Monitoring
Gaining a better grasp of the health of your assets is one of the major advantages of condition monitoring. After analyzing the condition monitoring data, you will have new insight into the distinctive characteristics of each asset.
These are some of the most common advantages of condition monitoring:
- Increases Uptime
- Reduces Unplanned Failures
- Lowers Maintenance Costs
- Improves Asset Life
- Frees Technicians of Unnecessary PMs
- Makes Planning and Prioritization of Work Orders Easier
- Increases Maintenance Efficiency
- Improves Visibility and Knowledge of Asset Health Data
Simply put, probably one of the greatest advantages of condition monitoring is fewer equipment failures. That one impact alone leads to all of the other advantages of condition monitoring, including better equipment availability and more productive operations for longer periods.
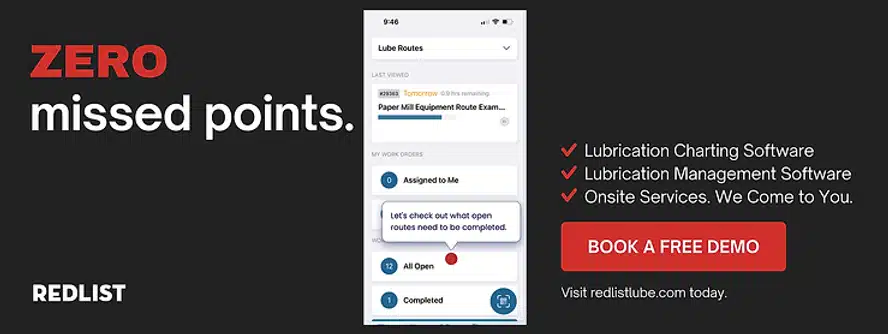
The Advantages of Condition Monitoring Sensor Integration
One of the key steps of condition monitoring is to install sensors on your assets. Sensors will keep an eye on your equipment to look for signs of declining performance or impending breakdown. As a result, fewer manual tests and inspections are required. However, automating the collection of condition monitoring information means you will have a lot of data to analyze. If you don’t have a system in place to do so, you most likely won’t reap the full benefits of condition monitoring. So, it is essential to automate the analysis, alerts, and even trigger workflows when condition monitoring thresholds are hit. Then, with very little manual input or labor hours up to this point, your maintenance team can attend to the problem and carry out the required maintenance right away. That’s the power of lubrication management software that integrates with your condition monitoring sensors and systems.