A non-conformance is any deviation from specification or requirement. In other words, it’s anything that’s not supposed to happen in the production of a good or service. Non-conformances can stem from a variety of sources, including incorrect assembly, defective materials, and human error. They can also result in a wide range of problems, such as safety defects, reduced quality, and increased costs. Therefore, it’s essential that businesses have systems in place to detect and correct non-conformances before they cause serious damage. Fortunately, there are a number of steps you can take to mitigate the risk of non-conformances. By ensuring your workforce is properly trained, and your manufacturing processes are tightly controlled, you can improve the consistent quality of your products or services.
What is a Non-Conformance?
Non-conformances mean that your process, product, or service doesn’t meet the standard you set for it. This typically means that something went wrong along the way or your systems and processes weren’t followed. However, if you can determine the root cause of the non-conformance, you can make a plan to fix and prevent it. In order to handle and prevent them, it is important to understand the different kinds of non-conformances.
Types of Non-Conformances
Non-conformances are often broken down into two categories, either major or minor. The key difference between the two is the amount of work it will take to correct the non-conformance. However, other differences include the impact, ease of detection, and recurrence.
- Minor Non-Conformance
- Impact – small impact or doesn’t impact customers directly.
- Detection – easily detected by your systems and processes.
- Recurrence – happens rarely.
- Major Non-Conformance
- Impact – large and/or negative impact on your customers.
- Detection – challenging to detect with your current systems and processes.
- Recurrence – happens regularly.
Additionally, a minor non-conformance can easily turn into a major one if you don’t address it.
Why is it Important to have a Non-Conformance Plan?
Identifying non-conformances is only one step. You must also have a plan for corrective and preventive action. Otherwise, you may face product recalls, rework, decreased productivity, increased operating costs, and unhappy customers.
Ways to Detect Non-Conformances
Considering the negative potential impacts of non-conformances, there are several steps you can implement for detection.
Customer Surveys
Proactively asking customers for feedback can bring things to your attention that you may not have known otherwise. A customer will likely complain about a major non-conformance, but you can detect a minor non-conformance from customer survey responses. Catching minor issues before they become major goes a long way in keeping your customers happy and maintaining a positive reputation.
Routine Testing or Inspection
As with any business strategy, you have to monitor, test, or inspect if you want to recognize trends and areas for improvement. So, make sure you have steps in your process that involve inspecting materials or testing the finished product are key to quality control.
Internal or External Audit
Sometimes it just takes a fresh set of eyes to spot where your product or service could be better. You and your employees may be too close to the process or too busy to think beyond what you’re already doing. In this case, you can have a manager from another branch or department review your process or even hire a consultant. Also, if you don’t want to audit your process, product, or service, you can simply open the floor for employee feedback. The people manufacturing the product or delivering your service to customers may already have ideas. They have in-depth, hands-on experience with the daily systems and processes, as well as past issues. You just need to let them know that you’re open to feedback and ideas.
The 5-Step Non-Conformance Process
There are five main steps to include in every non-conformance plan.
1. Containment
Once you identify a non-conformance, you need to contain it. That may be pulling the product from the production line or calling the customer who received poor service.
2. Short-Term Corrective Action
Your short-term or immediate corrective action is a remedy for right now. One way to think of it is that this is the bandage on a wound that you need to stitch up later. If you have an unhappy customer, the short-term corrective action might be offering to redo the service at no additional cost.
3. Root Cause Analysis
This step is essential to the success of your non-conformance plan. If you don’t dig deep enough with your root cause analysis, your long-term corrective action won’t fix the actual cause. That means the non-conformance will likely occur again.
4. Long-Term Corrective Action
Once you know the root cause of your problem, you can work with your team to create a long-term corrective action plan. The goal of long-term corrective action is to prevent the non-conformance from happening again.
5. Monitor for Effectiveness
This final step is almost as important as the root cause analysis. As the saying goes, “You can’t manage what you don’t measure”. So, you need to monitor to ensure the non-conformance doesn’t repeat. Also, this provides the opportunity to make revisions if you find that your long-term corrective action is not effective.
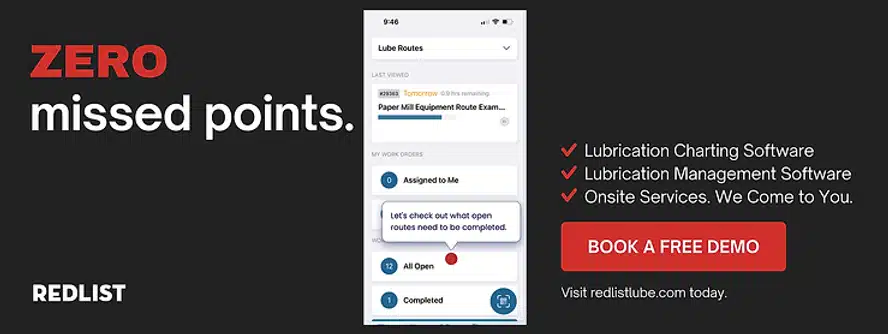
How can Software Help You Reduce Non-Conformances
Every business is looking to reduce the number of non-conformances in their operations. Fortunately, software can help you track and manage your non-conformances more effectively, as well as improve the overall efficiency of your systems, processes, and operations. From digitizing your non-conformance plan to automating steps of your production, Redlist has a suite of software that you can configure to your specific needs. We’d be happy to show you our three platforms and how they can support your business. Schedule a demo today to learn more.