As a maintenance manager or technician, you understand the importance of keeping your equipment running smoothly. One way to maintain your machines is to regularly clean and replace the filter elements. But, what about the air that’s circulating inside the machine? For your equipment to run efficiently, it’s important to keep the air as free from moisture and contaminants as possible. That’s where desiccant breathers come in. Read on to learn more about desiccant breathers and how they can help improve your machine’s performance.
What are Desiccant Breathers?
A desiccant is a hygroscopic substance, meaning it attracts and holds water molecules, that absorbs moisture from the air. You are more familiar with desiccants than you may realize. They are often used in packaging to prevent spoilage or keep products dry, such as the little silica gel packets in vitamin bottles. However, they are also used in filters called desiccant breathers. Desiccant breathers are used in lubrication management to help keep lubricants dry and free of contaminants.
The function of a desiccant breather is to remove moisture from the air that comes into contact with the lubricant, keeping the lubricant dry and preventing it from breaking down. In addition, desiccant breathers can help to filter out dust and other contaminants that can cause wear and tear on equipment. By keeping lubricants clean and dry, desiccant breathers can play an important role in extending the life of your equipment and reducing downtime.
A Must-Have for Your Lubrication Management
Proper lubrication is critical for ensuring the proper operation of machinery. Lubricants help reduce friction and wear, as well as protect metal surfaces from corrosion. However, lubricants can quickly become contaminated by water and other debris, reducing their effectiveness and leading to premature failure. Lubricant contamination is a major problem at the root of lubrication-related equipment failure, which is 70% of all equipment failures. Furthermore, studies have found that 50% to 70% of lubricant contamination actually originates from sources outside your equipment.
Prevent Lubricant Contamination
Any small step you can take to prevent contamination is critical for your lubrication management. That’s why desiccant breathers are an essential part of any lubrication management system, as they help prevent water vapor and other contaminants from reaching your lubricant. Since most machines are designed to “breathe” which brings in exterior contaminants, you have to filter the air your machines are breathing. Doing so helps to prevent lubricant contamination as much as possible, resulting in:
- Prolonged Life of Lubricants
- Reduced Maintenance Costs
- Increased Life of Additives in the Lubricant
- Decreased Corrosion and Rust
- Lower Component Wear Rate
- Decreased Downtime
- Improve Overall Asset Reliability and Health
How do Desiccant Breathers Work?
As you choose the right desiccant breather for your equipment, you’ll find there are several different configurations with unique features. Many desiccant breathers have a three-stage system that generally works like this:
- Stage One: A solid particle filter that removes particles over two microns in size.
- Stage Two: A silica gel desiccant dehydrates the air by extracting and retaining any water.
- Stage Three: A secondary solid particle filter to remove any remaining particles over two microns in size.
How Long are Desiccant Breathers Good for?
A very important detail to note is that desiccant breathers don’t last forever. The silica gel retains the water it extracts from the air. So, over time, it will eventually become fully absorbed and no longer function at 100%. Most desiccant breathers are designed with silica gel that will change colors as it reaches maximum water absorption. Regular inspection and replacement of your breathers are essential to continue preventing water contamination. If your desiccant breathers are sized appropriately, they can last three to six months. It all depends on the volume and frequency of air intake, the amount of desiccant in the breather, and how humid your environment is.
Where Should You Install Desiccant Breathers?
Reservoirs, tanks, bearing sumps, process pumps, and gearboxes are a few of the common applications for desiccant breathers. You may use these systems occasionally, which allows water to accumulate from headspace condensation. Any system that takes in air can introduce a large amount of water and dirt, so you should install a desiccant breather. Furthermore, desiccant breathers are a great addition to your lube room! Day tanks or containers for dispensing lubricants can breathe and contaminate your lube with water from humidity or temperature changes. Contamination prevention at every level from storage to machinery is key.
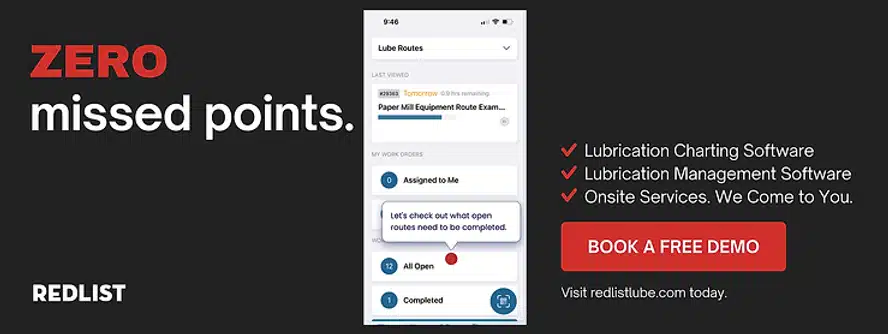
A Simple Solution for Lubrication Management
Lubrication management is about so much more than simply completing lubrication routes. There are preventive measures and best practices to implement at every step of the process, plus continuous improvement through lubricant analysis and condition monitoring. While some machines don’t need desiccant breathers because they are always running, at a high temperature of over 150°F, or have no history of water contamination. However, most equipment can benefit massively from the installation of desiccant breathers. It’s a simple solution that helps prevent a major problem you face daily with lubrication management.