As a reliability engineer, your primary mission is to enhance the longevity of equipment and ensure seamless operations. Equipment failure can lead to unplanned downtime, costly repair bills, and compromised safety. Understanding the common causes of equipment failure and implementing strategic preventative measures is essential to maintaining high equipment reliability. This guide delves into the top causes of equipment failure and how to mitigate them effectively.
Common Causes of Equipment Failure
1. Bearing Failure
Bearings are critical components in many pieces of machinery. Bearing failure often arises from inadequate lubrication, contamination, misalignment, or wear and tear. To prevent bearing failure, focus on proper lubrication management and regular inspections.
2. Inadequate Lubrication
Improper lubrication accounts for a significant percentage of mechanical failures. Lubrication manages friction and wear, but it must be managed effectively. Implementing a rigorous lubrication program and utilizing lubrication management software can drastically reduce the risk of equipment failure.
3. Contamination
Contamination of lubrication systems, bearings, and other components can lead to accelerated wear and eventual failure. This includes contaminants such as dirt, water, and process chemicals. Ensuring clean, contaminant-free lubrication systems through effective lubrication tracking is vital to equipment longevity.
4. Overheating
Overheating of components can degrade lubricants, increase wear, and lead to equipment failure. Proper ventilation, cooling systems, and regular inspections can keep equipment operating within safe temperature ranges.
5. Human Error
Human error, such as improper installation, neglect of maintenance, or incorrect operation, can lead to equipment failure. Invest in thorough training programs and clear, accessible maintenance procedures to mitigate the risk posed by human error.
6. Age and Wear
Age and natural wear and tear are inevitable. Regular condition monitoring and proactive replacement of aging components can prevent unexpected failures.
Preventative Measures for Reliability Engineers
Develop a Comprehensive Maintenance Plan
A structured maintenance plan, tailored to your specific equipment and operational needs, is the foundation of equipment reliability. This includes routine inspection schedules, lubrication management, and timely replacement of wear-prone components.
Implement Lubrication Management Software
Effective lubrication management is paramount. Redlist offers advanced lubrication management software, enabling reliability engineers to track lubrication schedules, monitor lubricant condition, and analyze lubrication data to optimize maintenance tasks. The benefits of using Redlist’s lubrication management software include:
- Enhanced Lubrication Tracking: Automated tracking of lubrication schedules ensures no task is overlooked.
- Data-Driven Insights: Access real-time data to make informed decisions and prevent equipment failure.
- Efficiency Improvement: Streamline lubrication processes, saving time and reducing manual errors.
- Increased Equipment Reliability: Optimized lubrication leads to prolonged equipment life and fewer failures.
For more in-depth strategies and practical advice, download our comprehensive guide: “Mastering Lubrication Management: A Comprehensive and Practical Guide to enable Enhanced Equipment Reliability.” This book aims to equip lubrication practitioners, reliability engineers, and maintenance managers with the information they need to significantly improve their equipment reliability programs. Get your copy today and start mastering lubrication management for enhanced operational excellence.
Condition Monitoring and Predictive Maintenance
Utilize modern condition monitoring tools and predictive maintenance strategies. Tools such as vibration analysis, thermal imaging, and oil analysis can provide early warning of potential issues before they lead to failure.
Training and Development
Regular training sessions for maintenance staff and reliability managers can reduce human errors. Ensure everyone involved understands the importance of adherence to maintenance protocols and is proficient with the tools and software employed.
Frequent Reliability Reports
Generate and analyze reliability reports regularly. Monitoring key performance indicators and identifying trends helps in refining maintenance strategies and pinpointing potential areas of concern.
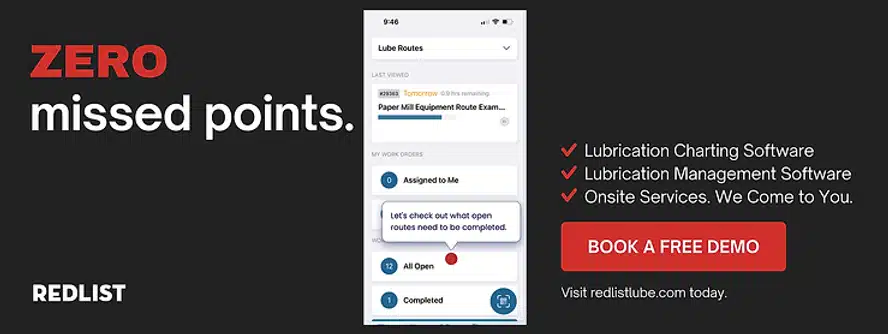
Conclusion
Preventing equipment failure is an ongoing challenge for reliability engineers, but with the right tools and strategies, it is entirely achievable. Implementing comprehensive maintenance plans, utilizing advanced lubrication management software like Redlist, and investing in staff training are pivotal steps toward enhancing equipment reliability. Remember, proactive prevention is always more cost-effective than reactive repairs.
To experience the benefits of Redlist’s lubrication management firsthand, don’t miss the opportunity to book a free demo today. Empower your maintenance team with the right tools to ensure your equipment runs smoothly, efficiently, and reliably.