Did you know that there are specific requirements your lube oil system needs to meet to keep your equipment running smoothly? In this blog post, we will discuss the top 10 lube oil system requirements to consider when choosing your lube oil system or maintaining your current one. Make sure your system meets these standards to help avoid costly downtime and repairs.
What is a Lube Oil System and How Does it Work?
Lube oil systems are also known as lube skids or circulating oil systems. Gas turbines, blowers, gearboxes, bearings, and other industrial equipment are common applications for a lube oil system. Basically, a lube oil system continuously lubricates the equipment and can even cool or heat the lubricant. A lube oil system helps to minimize temperature fluctuations and reduce the circulation of contaminants. In most cases, lube oil systems operate in a loop until you need to replace the filter.
The Lube Oil System Requirements You Should Keep in Mind
1. Flow Rate
Whenever lubricant is feeding to more than one bearing, your lube oil system’s flow rate must match the total requirements. To regulate flow into the bearing, there will be a needle valve at the delivery point. Additionally, you should size the pump and motor to maintain the maximum flow rate necessary, plus some buffer.
2. Pressure
The typical operating pressure is 35 psi (pounds per square inch) or less. You may require higher pressures for specific applications, such as a system that suspends a bearing in lubricant during startup to prevent metal-to-metal contact. The primary factor affecting the maximum amount of pressure possible is the pump’s capacity. Additionally, by changing the bypass relief valve to let less oil into the bearing, you can raise the system pressure.
3. Pumps and Motors
Depending on the available power sources, you can choose from several motor voltages, frequencies, and phases. The typical lube oil system motor works well in a variety of industrial environments thanks to its TEFC (totally enclosed, fan-cooled) rating. If your system will be near combustible vapors and particles, you might need an explosion-proof rating. Furthermore, you will have to determine the class, division, and group for an explosion-proof motor.
4. Filtration
Generally, your lube oil system will have three different types of filtration. The reservoir is divided by a baffle first. Particles settle and oil pours over the top of the baffle, creating passive filtering. Next, the fluid travels through a mesh strainer as it leaves the reservoir to complete the second stage of filtering. Before the fluid returns to your equipment, it undergoes the final filtration. At this point, most lube oil systems have a 23-micron filter. You should routinely clean the strainer and keep an eye on the filter for the optimal replacement to preserve lubricant cleanliness.
5. Gauges
Gauges are vital in helping you monitor your lube oil system’s operational characteristics. A pressure gauge between the bypass valve and the pump avoids the buildup of too much pressure. Next, you can monitor the temperature of the fluid inside the tank thanks to a liquid-level gauge with an integrated thermometer. Installing a temperature gauge in the pipe will allow you to keep track of the lubricant’s temperature after it passes through a heat exchanger. Also, you can use a differential pressure gauge to track pressure loss due to filtering. It could be time to replace your filter if the system pressure declines.
6. Switches
There are seemingly endless switch options to consider for your lube oil system. You can implement switch signals for electronic controls to turn on alarms, regulate a unit’s operation, send information to monitoring stations, or stop operations. As the temperature rises, a signal can alert the heat exchanger, or a temperature switch can activate it. A liquid-level switch can warn that there is not enough oil in the tank if the system fails or there is not enough fluid circulating. Another option is to utilize a liquid-level switch to alert you when the tank level is high if there is an unexpected flow restriction in the piping or at the bearing.
Additionally, a low-flow switch turns on when the flow falls below a predetermined threshold. This could happen as a result of a fluid drain, malfunctioning pump, clogged filter, or power loss. A switch’s signal provides a critical early warning for corrective action. It informs you that the pressure has increased by a differential pressure switch after the fluid has passed through the filter. This signifies that it’s time to replace the filter.
7. Heat Exchangers
A heat exchanger’s purpose is to lower the oil’s temperature before reintroducing it to the bearing. The heat exchanger uses either air or water to transfer heat from the lubricant. An air-cooled heat exchanger circulates oil through a web of smaller pipes while having air blown over them by a fan. If you choose a water-cooled heat exchanger for your lube oil system, the piping will pass through a cylinder that receives a continuous flow of cool water.
You must be aware of the temperature of the oil as it exits the bearing and the necessary temperature for its return to select the ideal heat exchanger for your application. After that, you can figure out how many BTUs (British Thermal Units) your system must remove each hour. The oil temperature can only be as low as the temperature of the surrounding air when utilizing an air-cooled heat exchanger. With an increase in ambient temperature, you will need a larger heat exchanger. Lower water temperature and higher water flow yield improved efficiency from a water-cooled heat exchanger. An attendant can manually operate a heat exchanger, leave it running continuously, or have it run automatically using a temperature switch or information from a temperature gauge.
8. Immersion Heaters
To raise the lubricant temperature, immersion heaters make contact with the lubricant in the reservoir. This heats the lubricant for a smoother startup, making it perfect for systems in cold regions. The immersion heater heats the oil to the right viscosity before circulating it to the bearing. Moreover, the heater can have an integrated thermostat to self-regulate when the lubricant reaches the ideal temperature.
9. Installation Environment
Lube oil systems are affected by the environment around them. Taking altitude, climate, and weather conditions into consideration is essential for the design to be successful. Depending on the space available for the unit, the dimensions of the tank, locations of components, and piping layouts vary.
If you want your lube oil system to be gravity-fed, you must install the system lower than the equipment it circulates the lubricant to. To avoid backups, you should make sure the return line is properly vented and two sizes larger than the supply line. The amount of pressure required to provide oil to the bearing can be affected by the elevation of the bearing, the size of the pipe, and obstructions from manifolds or nozzles.
10. Reservoirs and Piping
A typical reservoir is built of welded steel and has a heavy-gauge steel lid. It functions as a surface for mounting system components. In most cases, lube oil systems use iron pipes and fittings with national pipe thread (NPT) fittings. However, pipes and reservoirs can also consist of stainless steel. You have to paint or coat the entire system to prevent corrosion. Finally, lube oil systems should have their component functionality and leak detection tested before being put into service.
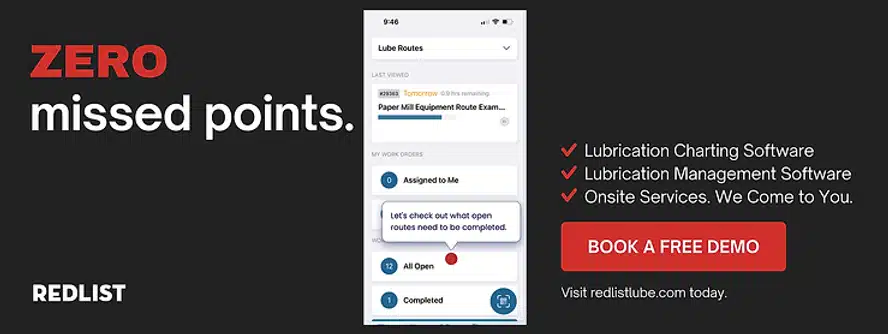
Lube Oil Systems Provide Excellent Lubrication Management Support
Lubrication management is a must for your equipment, no matter what sector of business you are in. Having the appropriate lube oil system in place is one of the greatest ways to automate lubrication in large facilities. This helps minimize wear and tear, which can help you save time and money, ensure that your equipment operates smoothly, and increase reliability. Selecting the best one, however, might be intimidating given the number of elements that go into the design of your lube oil system. There isn’t a single, universal lube oil system. To find the right fit for you, consider all ten of these lube oil system requirements.