In any industry, equipment reliability determines a company’s success. Reliability engineers are critical to this success because they are at the forefront of the efforts to achieve reliability and minimize equipment failure. This post provides a detailed look into a reliability engineer’s responsibilities, tools, and skills needed to accomplish reliability goals.
What Equipment Reliability Means
To understand the role of a reliability engineer, first, you must understand what equipment reliability means. Reliability is defined as the ability of any system to function properly under specific conditions and periods. It is a measure of consistency, dependability, and predictability of performance.
Reliability is a critical attribute of machines, equipment, and other assets to achieve:
- Operational Efficiency – Having reliable equipment means having smooth and uninterrupted operations, thus having high productivity and efficiency.
- Cost Savings – High reliability also means reduced frequency of failure and maintenance, leading to lower repair costs and less downtime.
- Customer Satisfaction – Reliable equipment results in reliable products and services, increasing customer satisfaction and loyalty.
- Safety – Assets with high reliability reduce the risk of accidents and hazards, resulting in a safer environment for operators, employees, and other staff.
- Quality – Reliable equipment results in products and services with consistent performance and minimal defects or waste.
What a Reliability Engineer Does
A reliability engineer is a professional responsible for ensuring the reliability of machines, equipment, and other assets. Their primary focus is to minimize failures and maximize the performance of these assets. They do this through various methods including:
1. Failure Analysis
A reliability engineer must understand any failure experienced to prevent its recurrence. They must conduct root cause analysis (RCA) to understand the causes of equipment failure. They must also perform failure mode and effects analysis (FMEA) to evaluate potential failure modes and their impact on equipment performance.
2. Maintenance Strategy Development
Proper maintenance is essential to achieve optimum asset reliability. A reliability engineer must develop and implement preventive maintenance schedules that are effective in preventing unexpected breakdowns. They should also use predictive maintenance techniques, including condition-based monitoring, to forecast and optimize maintenance tasks.
3. Design and Process Improvements
The design of a machine or asset and the processes in an operation affect reliability. Therefore, a reliability engineer must review new assets or proposed processes to ensure that reliability is considered before their installation and use or implementation. A reliability engineer should also review current assets and processes to recommend reliability-related modifications and upgrades.
4. Reliability Testing
The current reliability status of assets provides accurate and relevant data for effective business planning and decision-making. A reliability engineer must conduct life testing on assets to determine the lifespan of asset components. They should also perform stress tests to identify potential weaknesses under extreme conditions.
5. Data Analysis and Reporting
Asset data provides valuable insight into asset health and future failures. A reliability engineer must analyze failure data to predict potential failures and improve reliability. To add to this valuable asset data, they must track and report key performance indicators (KPIs) such as Mean Time Between Failures (MTBF) and Mean Time to Repair (MTTR).
6. Training and Collaboration
Achieving high reliability depends on the proper education and training of relevant operators, maintenance staff, etc. A reliability engineer must spearhead the education of these personnel on reliability principles, techniques, and best practices. The reliability engineer must also lead the collaboration among different departments, such as operations, production, and maintenance, to ensure a holistic approach to reliability.
7. Risk Management
The use and failure of assets come with risks that impact businesses, human lives, and the environment. A reliability engineer must identify and assess said risks and develop and implement mitigation plans to address them.
Tools and Techniques of Reliability Engineers
To perform their varied roles and responsibilities, Reliability Engineers require the following:
- Condition Monitoring Tools – Includes sensors, devices, and equipment for real-time tracking of equipment condition and health. Examples are vibration sensors, thermal imaging equipment, etc.
- Analytical Software – Computer programs or applications that can help with reliability analysis, maintenance planning, and data management.
- Statistical Software – Methods and computer programs that can analyze failure data and predict future failures.
- Reliability Block Diagrams (RBD) – Visual methods and tools to analyze the reliability of complex assets.
Essential Reliability Engineer Skills
Accomplishing reliability goals requires Reliability Engineers to have the following skills:
- Technical Skills – Including knowledge of statistical, mathematical, and engineering concepts.
- Analytical Skills – Including skills in problem-solving, critical and logical thinking, strategizing, and risk management.
- Communication and Collaboration – Including the ability to work with cross-functional teams like maintenance and operations, and to train and educate various team members.
- Project Management – Including skills in planning, scheduling, and organizing multiple tasks and activities while keeping detailed records and reports on these activities.
- Technological Skills – Including skills to use condition monitoring tools, computer software, management systems, analytical software, and other complex technological tools.
- Leadership and Innovation Skills – Including skills to promote continuous improvement, keeping up-to-date with the latest trends and technologies, and adapting innovative solutions to improve reliability.
- Industrial Knowledge – Including knowledge of current standards and regulations on reliability and safety, familiarity with legal requirements, and specific knowledge of the industry in which they work (for instance, food manufacturing or mining).
- Specialized Skills – Including additional abilities that they can acquire through training, hands-on experience, and certifications.
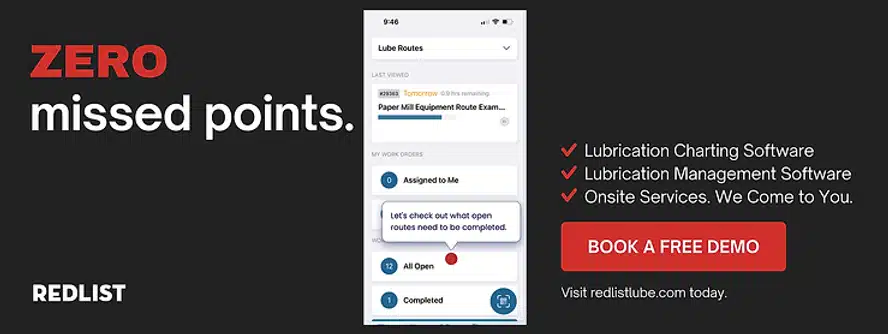
Technological Support for Reliability
A complex and multifaceted objective like reliability requires a professional with a combination of technical, analytical, interpersonal, and project management skills. Even then, they still need all the additional support they can get. Redlist’s Computerized Maintenance Management System (CMMS) can provide this valuable support.
By leveraging Redlist’s powerful computing functions, cloud-based storage, and mobile capabilities, reliability engineers can easily accomplish their responsibilities. Redlist provides an all-in-one user-friendly platform for reliability engineers and multiple users, fostering collaboration and clear communication. Redlist is the ultimate technological support for seamless, error-free, and continuously improving reliability programs. Schedule a free demo with our experts and learn how we can support your reliability efforts today!