A primary challenge companies experience with their asset maintenance is simply having enough resources to get it all done. Whether you need more time or people to achieve your goals, autonomous maintenance (AM) may be an alternative solution. Autonomous maintenance is a maintenance strategy that involves training your machine operators to handle some basic or routine maintenance tasks. These tasks may include inspections, cleaning, lubrication, adjusting bolts, or even safety checks. This results in better-maintained equipment and frees up your maintenance technicians to do other work. Additionally, autonomous maintenance is a pillar of any Total Productive Maintenance (TPM) plan.
Why Should You Invest in Autonomous Maintenance?
Like most maintenance strategies, achieving autonomous maintenance will require an investment of time and money. Training your operators takes them away from their work, which may feel wasteful when you have technicians who already know how to do these tasks. However, the benefits of autonomous maintenance far outweigh the cost.
Early Detection of Problems
While your maintenance technicians only deal with an asset when they’re working on it, your operators work with that asset every day. Furthermore, with the right knowledge, your operators can detect issues, malfunction, or signs of breakdown before it becomes a major problem. This helps prevent unplanned downtime and potentially reduces the cost of repairs needed.
Increase Overall Equipment Safety and Reliability
Preventing unexpected equipment breakdown improves reliability. Also, autonomous maintenance isn’t limited to maintenance. Training operators to perform important safety inspections ensures that the equipment is operating safely and employees avoid accidents.
Complete More Preventive Maintenance and Reduce Backlog
Shifting the load of preventive maintenance (PM) to no longer be carried by your technicians alone means you can complete more preventive maintenance. As technicians are often busy with more critical or urgent maintenance work, preventive maintenance can slip through the cracks. Allowing your operators to take on simple PMs ensures that they get done. Also, the time it saves your technicians can be put towards reducing backlog or handling other higher-level equipment issues.
Improve Cleaning and Lubrication
When your technicians focus on major repairs, it is possible to miss or speed through the detail work. For that reason, cleaning and lubrication tasks are simple, detailed work that you can assign to operators instead.
Reduce Labor Expense
Depending on your industry, how many locations you have, and whether you dispatch equipment for field services, you may have maintenance technicians spending time traveling. In many cases, this puts production on hold while waiting for the technician to arrive. So, you have a downtime cost plus the cost for your technician to spend time and resources traveling.
For example, one Redlist user dispatches cranes to various job sites. They were experiencing recurring boom repairs caused by a lack of lubrication that cost around $500,000 per year in downtime and repairs. If a crane needed lubrication, the job would have to be put on hold while a maintenance technician traveled to the job site. Using Redlist’s Enterprise Asset Management (EAM) software, the company created a process of autonomous maintenance. Now, crane operators know what to look for in their pre-op inspection to prevent the boom failure, and they can even perform the lubrication task themselves. Read more about their experience and $500,000 savings in their case study.
Improve Equipment Knowledge and Operation
The more an operator knows about their equipment, the better they will be at operating it. In performing basic maintenance, your operators will increase their equipment knowledge. This could include a better understanding of the equipment’s temperature limitations, allowing them to notice when something is overheating. Or, they may learn the meaning behind certain sounds that are an early signal of breakdown. Whatever knowledge they gain from autonomous maintenance training will result in improved productivity, reliability, and early detection, as outlined above.
Create Accountability and Empowerment
It sounds like a simple thing, but creating accountability leads to so much more. When you empower your operators to take on autonomous maintenance tasks, they end up with a greater feeling of ownership of the equipment they work with. When an employee feels a sense of responsibility for their equipment, they will be more caring and mindful of its maintenance and use.
The Steps to Implement Autonomous Maintenance
There are seven steps to implement autonomous maintenance. But, there is a lot of room to optimize the process within each of those steps. One of the main ways to support your operators as they take on autonomous maintenance tasks is to use EAM software. We outline how it helps at each step below.
1. Train Your Operators
An EAM will help you track the training of current and future operators and provide ongoing resources if they forget how to do something. With Redlist, you can give your operators digital checklists and even photos and videos that walk them through the maintenance task.
2. Initial Inspection and Cleaning
With our EAM’s digital forms tool, your operators can complete their first inspection and cleaning and submit any issues they identify. They should look for leaks, cracks, improper lubrication, loose bolts, dust or dirt, and abnormalities in sounds, smells, or temperature. You can also use this first autonomous maintenance experience to build their list of maintenance tasks.
3. Remove Contamination
The time invested in the initial inspection and cleaning shouldn’t go to waste. You can configure Redlist to automatically alert operators to perform regular cleaning to maintain your assets in “like new” condition. Additionally, you can include reminders and guidance for how to safely clean equipment, including your ‘lockout/tagout‘ (LOTO) procedures.
4. Determine Your Inspection and Lubrication Standards
This will be different for each piece of equipment and may vary based on how or how much you use the equipment. Redlist’s mobile app puts these standards in an accessible, convenient location so your operators don’t have to commit it all to memory.
5. Monitor and Inspect
Every maintenance strategy needs to be monitored and tracked for effectiveness. For example, if you implement autonomous maintenance and suddenly have an increase in equipment breakdown, you could pull asset data from your EAM to determine if it may be linked to your autonomous maintenance tasks. Your operators may need more training, or it may just be a coincidence. Having accurate, real-time asset data at your fingertips will ensure you notice trends and make adjustments.
6. Implement Visual Aids
Your operators can track their time spent on autonomous maintenance tasks in the EAM app, which allows you to understand if they’re working efficiently. Many companies support their operators by implementing visual aids to guide various steps of the maintenance process. This may include color-coded tags, switching to transparent covers, open and close direction labels, or even marking the direction of fluid flow in pipes.
7. Ongoing Improvement
Autonomous maintenance is just one step in an ongoing process. There will always be room for improvement, and your operators can provide a lot of feedback on that. Providing EAM software gives your operators an easy way to communicate with the maintenance team and management.
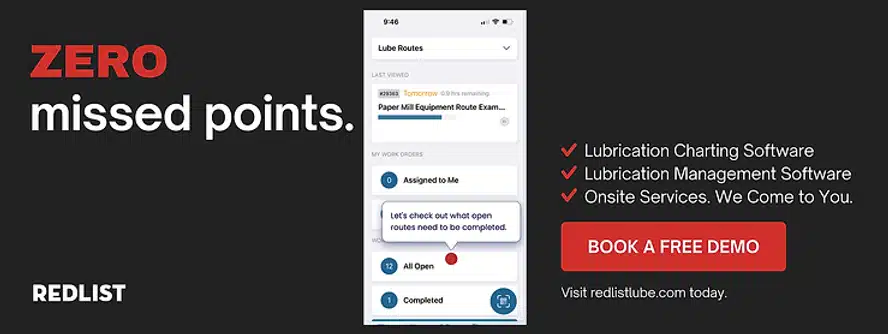
Achieve Your Maintenance Goals with Redlist
If you’re looking to implement new strategies to achieve your goals, then you can’t overlook your maintenance workflow. EAM software brings your people, assets, and data together to optimize every step of the process. It empowers you to standardize and centralize your data, making asset maintenance a truly collaborative team effort. And, that’s what autonomous maintenance is all about.