The maintenance and reliability of your industrial turbines are critical to the success of your business. And, just like any other piece of machinery in your plant, regular turbine lube oil analysis is essential to keeping them running smoothly. Because turbine lubricants have a service life of 10 to 20 years, regular lubricant analysis is more important than ever. By checking the condition of the lube oil, you can identify and address issues before they become bigger problems. In addition, routine analysis can help you optimize your lubrication strategy and extend the life of your turbine equipment. In this blog post, we’ll explore the importance of turbine lube oil analysis and how it can help you maintain peak performance from your turbines.
Why is Turbine Lube Oil Analysis so Critical?
Both gas and steam turbines have large reservoirs for lubricating turbine bearings, and newer turbines may combine lube oil and hydraulic sumps. You should carefully monitor turbine lube oil to ensure it stays in good condition for its full 10 to 20-year lifespan. This includes checking the physical and chemical properties of the oil, as well as checking for common contaminants such as water and particles. Not only is this essential for used lubricants, but also new oil must meet specific performance standards prior to use.
Furthermore, turbine lube oils undergo a variety of tough conditions, such as:
- A high degree of heat
- Moisture
- Entrained air
- Dirt and debris contamination
- The potential of cross-contamination with different lubricants.
It is under these conditions that the hydrocarbon base stock degrades and the additive chemistries deplete, causing irreversible molecular changes to occur. In a lubricant that can last up to two decades, these changes can drastically reduce its serviceability.
Turbine Lube Oil Degradation
In turbine applications, oxidation and thermal deterioration are the two main processes of lubricant degradation. In the chemical process of oxidation, oxygen interacts with the molecules of oil to produce a variety of different chemicals, including carboxylic acids. This happens at different rates depending on a variety of variables. The most important factor is probably temperature, as it doubles the rate of oxidation for every 10°C temperature increase. The oxidation stability of the oil, the presence of catalysts, and pro-oxidant factors including water, air, certain metals, fluid agitation, and pressure all affect the temperature above which this happens.
Alternatively, thermal degradation occurs when oil molecules are broken down by heat, resulting in insoluble compounds known as soft contaminants. Electrostatic spark discharge, hot spots, and micro-dieseling are common causes of thermal degradation. Micro-dieseling is a process in which imploding air bubbles combust, generating adiabatic compressive heat that often exceeds 1,000°C. Another common issue with turbines is electrostatic spark discharge. When oil passes through tight clearances at very high flow rates, an electrostatic spark discharge results. This is due to the internal molecular friction that creates a high-voltage electric charge, generating temperatures of over 10,000°C and thermal degradation.
The Challenge of Detecting Degradation
Different lubricant base stocks exhibit varying oxidation performances. In terms of molecular degradation, group II turbine oils are non-linear as a result of their high oxidative resistance and specific antioxidant components. As a result, most standard oil analysis tests do not provide enough warning when the turbine lubricant begins to degrade. Rather than degrading linearly and predictably, many turbine oils go from normal function to failing rapidly.
The first conditions of oil degradation to affect turbine performance are typically changes in the oil’s molecular structure as a result of additive depletion and the formation of insoluble particulates. Commonly, the next issue that appears is the formation of sludge and varnish.
Supporting Equipment and Turbine Lube Oil Analysis
There are standard turbine lube oil analysis tests for steam and gas turbines. However, there are also turbine lube oil analysis tests for auxiliary equipment that supports power-generating turbines. Gears, hydraulic systems, diesel engines, pumps, compressors, and electrohydraulic control (EHC) systems are examples of auxiliary equipment you can monitor. Testing your supporting equipment is essential to improving the reliability of your turbines.
Recommended Turbine Lube Oil Analysis Tests
With so many different lubricant analysis tests available, it can be difficult to determine which tests to run on each asset. These are the most common turbine lube oil analysis tests.
Viscosity
The primary physical characteristic of lubricants is viscosity. A sufficient supply of lubricant must reach parts at various operating temperatures, which is why lubricants must have the proper flow properties. According to their grade or classification, level of oxidation, and level of contamination while in use, lubricants’ viscosities differ. With time and usage, you can expect viscosity to increase. In fact, a loss of viscosity is seen to be more severe than an increase.
Acid Number
The ideal acid number is typically mentioned on equipment or lubricant manuals. Performing turbine lube oil analysis for acid number provides a way to track the oxidative degradation of oil while it is in use. When the TAN (Total Acid Number) value for a certain lubricant and application reaches a set threshold, it indicates that it is time to change the oil. An abrupt increase in TAN would be a sign of unusual operating circumstances, such as overheating. This can be a guide for equipment conditions that need attention.
Antioxidant Trend
Oil degrades and often becomes slightly acidic as oxidation byproducts build up. Furthermore, the lubricant will corrode the equipment’s vital surfaces if oxidation progresses to a serious level. Turbine oils have a long life, so they generally contain additives to reduce the effects of oxidation, including sludge and varnish.
Water Contamination
Too much water causes a lubricant to be less effective at separating moving parts. This can result in severe wear and significant frictional heat. For the majority of equipment, water shouldn’t be more than 0.25%. For turbine lube and control systems, water contamination shouldn’t be more than 100 ppm.
Particle Counting
Oil cleanliness testing is a crucial procedure for hydraulics, turbines, and filtered gearboxes. While this test can help you gauge filter efficiency, it does even more than that. Modern turbine lube oil analysis technology provides insight into where the particles are coming from and why. Additionally, it allows you to see the amount of ferrous material contributing to the count, as well as dirt and debris particles.
Elemental Spectroscopy
This turbine lube oil analysis test is a method for identifying and measuring metallic elements in used oil. Metallic elements are typically a result of wear, additives, and oil contamination. The test determines the concentration of each element by energizing the sample and measuring the amount of energy each element absorbs. This test is the foundation for all on-site and off-site oil analysis equipment, since it promptly and precisely identifies machine contamination and wear problems.
Wear Debris Analysis (WDA) or Analytical Ferrography
Using WDA, magnetic wear particles are separated from oil and deposited on a glass slide called a ferrogram. Next, the turbine lube oil analysis technician analyzes the slide to identify the wear mode and probable sources of wear. This form of turbine lube oil analysis is known as analytical ferrography. It is a vital test for recognizing abnormal wear on ferrous and non-ferrous metals.
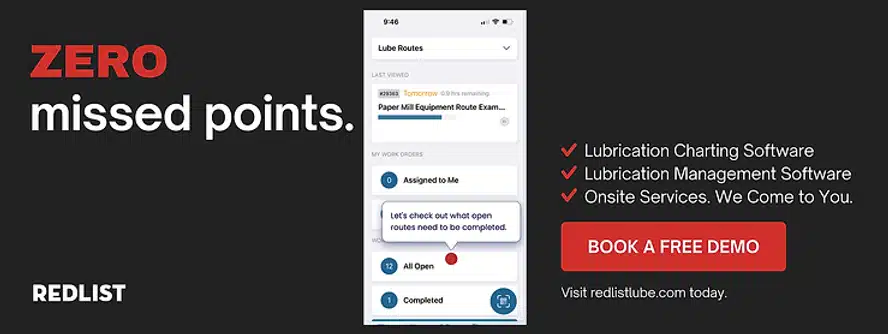
The Bottom Line on Turbine Lube Oil Analysis
In addition to oxidation and thermal degradation byproducts causing varnish and deposit problems in steam turbines, they interfere with demulsibility and air detrainment properties of steam turbine lubricants. Thus, it is necessary to perform regular turbine lube oil analysis to detect these conditions in such sensitive and critical lubrication systems. Furthermore, the support of lubrication management software to analyze turbine lube oil analysis trends or integrate with in-line sensors can go a long way to maintaining your turbines. Schedule a demo or contact us to learn more about how we can support your turbine lube oil analysis.