Machine downtime must be minimized in today’s fast-paced industrial environment in order to sustain profitability and efficiency. A very successful approach of reducing downtime is to apply the 5S concept, which is a lean manufacturing tool that emphasizes workplace organization.
“A place for everything and everything in its place” is the philosophy that best captures the essence of the 5S technique.
Marie Kondo created the “KonMari” system of house organization, which you may be familiar with. Homes that are disorganized can be made neat and simple with the KonMari approach. KonMari and the 5S principles are comparable. But to suggest that 5S is only about organizing things neatly is like arguing that speed is the only factor in successful manufacturing—there is much more to it than that.
The acronym for the 5S approach is Sort, Set Aside, Shine, Standardize, and Sustain. When used properly, it can greatly increase a workplace’s productivity and organization while also decreasing machine downtime. Understanding each stage and how it may be adjusted to support operations like overall machine downtime and lubrication management is essential to implementing 5S.
Let’s examine how each of the five S’s might boost operational effectiveness and decrease downtime.
The Benefits of 5’s
Despite having originated in the automobile sector, 5S is now commonly regarded as a necessary first step for any lean manufacturing program, regardless of the sector.
There is much more to integrating 5S into daily operations at your firm than just better organization, consistent cleaning schedules, and effective work processes. Operators are encouraged to eliminate waste and improve their entire work environment by implementing the 5S concept.
Among the main advantages of a 5S system are:
- Making room in your establishment by getting rid of extra tools and equipment.
- Arranging the workstation to cut down on needless motion waste.
- Lowering downtime and raising quality through regular equipment maintenance.
- Involving operators by giving them greater control over their workplace.
- Keeping the workplace neat and well-maintained to foster a safer atmosphere.
The 5 S’s
The 5S concept must be put into practice in order to minimize machine downtime, a chronic problem that has a significant negative influence on profitability and production. The five fundamental 5S principles—Sort, Set in Order, Shine, Standardize, and Sustain—all work together to produce an atmosphere at work that is efficient, safe, and well-organized.
The time needed to locate and retrieve tools and equipment is significantly decreased by emphasizing the removal of superfluous items and organizing them in a streamlined manner (Sort and Set in Order), which speeds up maintenance and repairs. Frequent cleaning and inspection (Shine) guarantees that possible faults are found and fixed before they become serious issues that lead to unplanned breakdowns.
By creating standardized processes, or standardizing, maintenance chores, errors that could result in equipment failure are avoided, and maintenance duties are carried out consistently and effectively. Lastly, businesses may maintain an environment that not only minimizes downtime but also promotes an efficient and responsible culture by sustaining these practices through ongoing audits and continuous improvement (Sustain).
Adding these procedures to cutting-edge programs, such as Redlist’s lubrication management software, makes the 5S process even more efficient. This all-encompassing strategy guarantees that equipment runs as efficiently as possible, reducing downtime and increasing output. Examples below explains the 5s in a detailed way.
1. Sort (Seiri)
‘Sort’ is the first step in the 5S process. Eliminating anything superfluous from the workspace is the main goal. This comprises any supplies that aren’t needed for ongoing business activities, such as tools, parts, and equipment.
The Way It Cuts Downtime:
– Elimination of Clutter: It is simpler to find the tools and parts required for maintenance and operations quickly when the workspace is bare of anything but necessities.
– Increased Safety: Eliminating superfluous items makes the workspace safer by reducing trip risks and creating more room. This lowers the risk of accidents and unscheduled downtime.
– Tool Efficiency: Workers focus more of their time on productive work and less time on finding supplies.
For instance:
Due to a shortage of tools for repairing machinery, a manufacturing plant was frequently delayed. They kept only the tools they needed in their immediate workspace by using the ‘Sort’ approach. Consequently, there was a 25% reduction in tool search time and a significant decrease in machine downtime caused by delayed repairs.
2. Set in Order (Seiton)
“Set in Order” emphasizes making sure that everything that is required is arranged as efficiently as possible and has a designated spot.
How Does It Minimize Downtime?
– Optimized Layout: Logically arranged tools and parts cut down on time spent getting them during maintenance.
– Effective Workflow: Parts and equipment that are used in tandem are kept close to one another in order to reduce movement and expedite procedures.
– Easy Identification: Tool accessibility and identification are facilitated by zones and storage options with clear labels.
For Example:
Lubricants that are kept in specific, clearly marked places improve the efficiency of lube management, especially for complex machinery. Redlist offers complete solutions that simplify lubrication management and organization. Delays brought on by improper or absent lubricants can be prevented by methodically organizing lubricants according to their application.
3. Shine (Seiso)
“Shine” entails routinely checking the equipment and tidying the workspace. Maintaining equipment in top shape to avoid unplanned breakdowns is the basic idea.
The Way It Minimizes Downtime:
– Early Detection: Frequent inspections brought about by regular cleaning aid in the early identification of possible problems.
– Reliable Equipment: Equipment that is kept clean and well-maintained runs more smoothly and is less likely to break down.
– Enhanced Morale: A spotless workplace fosters a happy culture, which can raise worker engagement and output.
For instance:
Redlist’s cutting-edge lubrication management software was included by a plant into its cleaning schedule. This made it possible to track lubrication schedules in real time and receive alerts for any deviations right away. They observed a 30% decrease in lubricant-related machinery downtime by routinely maintaining adequate lubrication.
4. Standardize (Seiketsu)
The goal of “standardizing” is to establish guidelines for practices and procedures that will guarantee sustainability and uniformity throughout the company.
How Does It Minimize Downtime?
– Consistent Processes: Standard operating procedures prevent errors and breakdowns by reducing variability.
– Predictive Maintenance: By creating and adhering to maintenance plans, equipment gets serviced when it is most needed, preventing unexpected breakdowns.
– Training Enhancement: Standardized procedures facilitate the onboarding of new staff members and guarantee uniformity and continuity of operations.
For instance:
By employing Redlist’s lube management systems, businesses may establish uniform lubrication procedures for all of their equipment. The program makes sure that all the machinery is lubricated accurately and on schedule, following a standard that extends the life of the machinery and lowers the likelihood of unplanned breakdowns.
5. Sustain (Shitsuke)
“Sustain” refers to keeping up and evaluating the 5S procedures that have been put in place to guarantee long-term success and ongoing development.
How Does It Minimize Downtime?
– Continuous Monitoring: Audits conducted on a regular basis guarantee that the 5S principles are followed, maintaining an orderly and productive workplace.
– Timely Corrections: The implementation of continuous improvement processes facilitates the prompt identification and correction of deviations prior to their causing downtime.
– Involvement of Employees: Upholding the 5S culture requires participation from staff members at all levels, encouraging a sense of accountability and ownership for keeping a tidy environment.
For instance:
Businesses can maintain their lubrication programs more successfully with the support of Redlist’s powerful lubrication management systems. The analytics and reporting features of the program offer insights that enable ongoing observation and enhancement, guaranteeing consistent performance and equipment availability.
Get Redlist to Achieve the Best Lubrication Management
As a pioneer in the lubrication management sector, Redlist provides all-inclusive solutions that work in unison with the 5S methodology. In this way, Redlist can assist:
Why Choose Redlist?
– Advanced Feature: The software from Redlist has features like thorough analytics, automated lubrication scheduling, and real-time monitoring.
– User-Friendly Interface: All staff members can utilize the platform because it is simple to use and needs little training.
– Custom Solutions: Designed to satisfy the particular requirements of different industries, guaranteeing peak performance and minimal equipment downtime.
Businesses may improve their lubrication management procedures, cut down on maintenance time, and eventually reduce downtime for their machines by implementing Redlist.
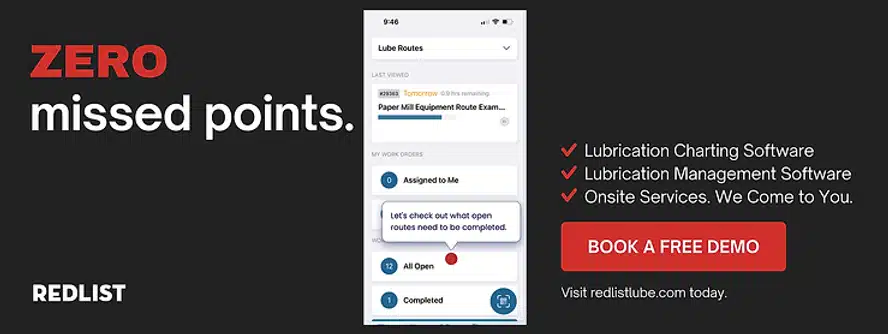
Conclusion
Putting the 5S concept into practice is a great way to streamline the workplace, increase productivity, and decrease downtime for equipment. Sort, Set in Order, Shine, Standardize, and Sustain are the steps that contribute most to the optimization of operations by reducing wasteful time and resources.
Incorporating a reliable lubrication management system such as Redlist guarantees that machinery is constantly in optimal condition and expedites procedures even more. Avoid letting equipment failures affect how productive you are. By utilizing Redlist’s cutting-edge features and adopting the 5S philosophy, you may start down the path towards a more efficient and organized workplace.
Are you prepared to change the way you manage your lubrication and see a major decrease in downtime for your machinery? Schedule a free demo now to see its possibilities. See for yourself how our cutting-edge technologies can transform your maintenance procedures and boost productivity.