There are several important pieces to keeping a business running and productive. However, workplace safety may top the list. Naturally, safety managers have come up with phrases or safety slogans to keep safety top of mind for employees. One of these safety slogans is the take 5 safety procedure. You may have seen safety posters or training using the phrase, “Take 5. Stay alive.” But, what is the take 5 safety procedure? It is a 5-step process that breaks down to:
- Stop
- Look
- Assess
- Control
- Monitor / Proceed
This safety procedure is all about thinking through the work you’re about to do and assessing your environment. Increased awareness can catch small or big things that help prevent accidents.
The Steps of the Take 5 Safety Procedure
1. Stop & Think
The first step of take 5 safety is to pause and think through your day or next task. It’s easy to be distracted or tired at work, or even grow lackadaisical as you do the same work every day for years. If you work in an industry with a lot of hazards present and a high risk of accidents, then you must always have safety at the forefront of your mind.
While you may not feel like you have the time to take 5 minutes before every task, even a quick mental review and preparation can make a difference. These are some important questions you can think about before beginning your work:
- What task are you about to perform?
- Where are you performing the work?
- What equipment will you need to use?
- What parts, tools, or materials will you be using?
- Are any other employees or contractors helping you or in your workspace?
2. Look & Identify
If you only spend a short time on step one, spend a bit more time on this portion of your take 5 safety process. Check your surroundings, workspace, and equipment to identify any hazards that are present or potential risks. For example, if you’re doing crane work near overhead powerlines, your hazard list would include confirming whether the powerlines are energized or not.
That could make a huge difference in your workplace safety if the lines are energized and aren’t supposed to be. However, don’t write off the seemingly small hazards. If you work outside, something as small as an uneven or slippery surface could be a hazard for using a ladder.
3. Assess Hazards
The next step of take 5 safety is to assess the list of hazards you made. While a literal list can be helpful, even keeping a safety mindset throughout your workday to regularly assess your environment is good practice. Assessing hazards involves measuring the potential risk of damage or injury that the hazards could cause.
4. Control Hazards
While steps one through three mostly involved observing and thinking, step four involves taking action. It is all about reducing the risk by taking some action to control the hazards. To continue with our crane and powerline example, controlling the hazard would be contacting a colleague to confirm whether the lines are energized.
The other example of surface conditions for ladder use would require securing the ladder appropriately or simply finding a better spot to place it. Taking action to control hazards puts your safety in your hands.
5. Monitor & Proceed
There is some inconsistency with the final step of take 5 safety. Some references say monitor and others say proceed, but the essence is that you can now safely complete your task. Still, you will want to proceed with caution, awareness, and continue to monitor the hazards. If your preventive action turns out to be inadequate for that hazard, then you’ll likely have to deal with it while you are performing your task.
Also, there may be hazards you did not identify because they occur as a result of your work. This is why monitoring is a necessary part of proceeding safely.
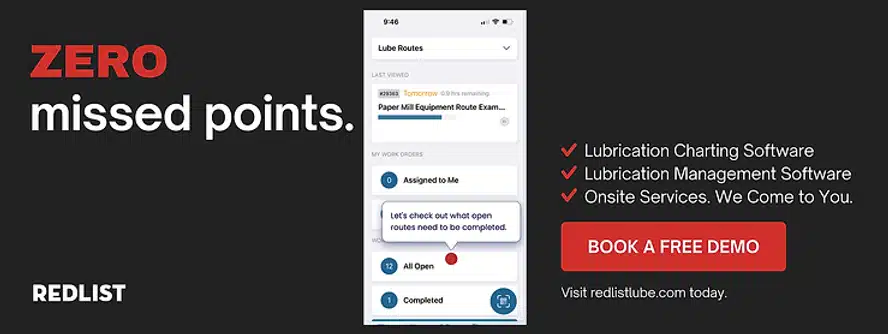
How to Improve Workplace Safety Beyond Take 5 Safety with Redlist’s HSE Software
Employees may not take the time to go through this 5-step process before every task. Nevertheless, the essence of the take 5 safety procedure is to create greater awareness of your surroundings, the work you’re about to do, and the possible hazards. However, workplace safety is so important that it requires more than a simple take 5 safety procedure.
Redlist’s HSE software facilitates the transition from paper-based safety checks to a streamlined cloud-based software that empowers every team member to contribute to a culture of safety. This shift allows for quick creation and distribution of digital safety forms, real-time monitoring of safety metrics, and automated reporting, ensuring that safety trends and compliance metrics are promptly identified and addressed.
Seamless integration of the HSE software with current systems is another key point, which ensures that safety is not isolated within the company but is part of a holistic approach to organizational safety goals. Additionally, Redlist provides expert services and support, acting as a partner in safety and sharing specialized experience to help achieve safety goals.
Incorporating these points into the content will highlight the advanced capabilities of Redlist’s HSE software, showing how it builds upon the Take 5 Safety Procedure to create a safer workplace.
Discover how Redlist’s advanced HSE software can revolutionize your safety management beyond the Take 5 Safety Procedure. One customer reduced all of their safety-related incidents by 50% after the implementation of Redlist’s HSE solution. If you’d like to see how we can help you build and improve your safety culture, schedule a demo today.