The Covid-19 pandemic caused a significant disruption to supply chains across the world. With lockdowns and travel restrictions, businesses closed or operated at limited capacity, halting the production of many goods. As a result, many companies are experiencing delays in receiving raw materials. This results in a shortage of finished products in a wide range of industries. This has led to increased costs for businesses and higher prices for consumers. Overall, the ongoing supply chain crisis exposes the fragility of global supply chains and the need for more resilient supply chain practices. But, companies that rely on equipment that need a consistent supply of lubricant can’t wait for the supply chain to improve. In this blog post, we will cover some ways you can minimize the impact of supply chain disruptions.
The Supply Chain Crisis’ Impact on Lubricants
The supply chain crisis requires companies to employ far greater planning of their lubrication management inventory. Lubricants now have greater lead times, and in some situations, they may not even be available. These days, it is more crucial than ever to optimize the lubricants you use, your inventory levels, and many other programmatic difficulties that result in higher lubricant usage.
How to Reduce the Impact of the Supply Chain Crisis
The main way to reduce the impact of the supply chain crisis is to make your inventory last longer. You can do this by making a few changes to your operations.
Check Your Relubrication Intervals
A great first step is to determine if the recommended relubrication intervals and volumes are being adhered to. When working with greases, this is often a significant problem. Every week or two, technicians often relubricate bearings and other grease-lubricated parts. This adds up to a significant amount of lubrication when spread across a plant with hundreds to thousands of bearings.
If you were to calculate the ideal intervals for greasing, you might find that the component to which you are adding grease every week actually only requires it once every few weeks or once every several months. Depending on the quality of your lubrication route charting and lubrication work order details, it’s easy to over-lubricate a component. This is an issue in times of a supply chain crisis because excessive greasing wastes a lot of lubricants. However, it also wastes another valuable asset–the time of your lubrication technicians.
Examine the Quality of Your Lubricants
As you likely already know, lubricants come in a wide range of qualities. That means not all lubricants are created equal. Some offer more protection in particular places and function better over time, even having a longer service life. If you’re using low-quality lubricant, and you have to change the oil often, you can consider switching to a higher-quality lubricant. While you will pay more, the higher-quality lubricant will last longer, resulting in a reduction in lubricant use.
Check your lube room and consider the function of your lubricants, including base oils, additive packages, and performance-related testing. To get an idea of how long a lubricant might last, users usually turn to tests like the Rotating Pressure Vessel Oxidation Test (RPVOT) and Turbine Oil Oxidation Stability Test (TOST). These tests provide insight into oxidative stability. However, you must first identify the most likely reasons why your equipment will experience lubricant failure before analyzing the relevant test findings.
For example, if your lubricants are more likely to fail due to water contamination, you should consider lubricants that perform better in hydrolytic stability tests. If you use more stable lubricants, the initial investment may be greater. But, in the long run, you will require fewer changes and, as a result, fewer gallons.
Implement Condition Monitoring
Condition monitoring is vital to lubrication management during a supply chain crisis because it allows for the efficient use of lubricants by accurately identifying when lubricants need to be replenished or replaced. This is an ideal way to dial in the frequency of relubrication and oil changes. Additionally, condition monitoring can provide early detection of potential equipment failures, which can prevent costly downtime and disruption of operations. You can also use it to help identify the root cause of equipment failures, which can assist in addressing the underlying issues and preventing future failures. Overall, condition monitoring is a crucial tool for maintaining equipment reliability and minimizing the impact of a supply chain crisis on operations.
You can begin with condition monitoring tools like ultrasound and grease analysis. Grease analysis ensures that you lubricate gears, bearings, and other components at the appropriate time with the correct amount. Similarly, oil analysis ensures that you only change the oil when necessary, getting the full useful life out of your lubricant. Also, by keeping an eye on the oil’s health, action may be taken when contaminant levels increase, extending the oil’s lifespan. You might choose to do a bleed-and-feed or partial oil change in some circumstances, depending on the oil’s condition, rather than changing it completely.
Use the Optimal Amount of Lubricant
While frequency is important, the amount of lubricant you use is equally important. If you go by the phrase, “Grease it ‘til you see it,” then you may be overlubricating. This can lead to seal damage and excessive lubricant consumption, which you want to avoid during a supply chain crisis. You can lessen this by choosing the right regrease volume. When you use the proper amount of grease, you reduce your lubricant needs, the equipment operates at a lower temperature, and your seals remain in better working condition.
Furthermore, the same goes for oil. Many splash-lubricated components lack a trustworthy way to assess the lubrication level while they are in use, which can lead to excessive fluid levels. Not only does this increase the amount of oil used during the initial fill, but it also raises the temperature at which the machinery operates. More frequent oil changes are required since the operating temperature is rising and shortening the fluid’s life. It’s crucial to take into account the higher energy expenses associated with processing the additional volume. So, optimizing your lubricant volumes is an essential best practice, even if there isn’t a supply chain crisis.
Follow Storage Best Practices
Storage is another area in a lubrication program where good lubricants might go to waste. Oil contamination runs rampant in many lube rooms, and it reduces the life of your oil. Also, additives might separate as well, resulting in disappointing results when put into service. You should follow the right storage procedures to prevent either of these from happening to your lubricants.
This involves, to the greatest extent possible, keeping lubricants sealed and in climate-controlled rooms. Additionally, this might involve the use of kidney-loop filters for tanks used for bulk storage. You should periodically circulate the stored oil to keep the additives in solution, eliminate any contaminants, and keep the lubricant in good condition before use. It is often necessary to dispose of lubricants that have been kept outside and exposed to humid air before they are ever used.
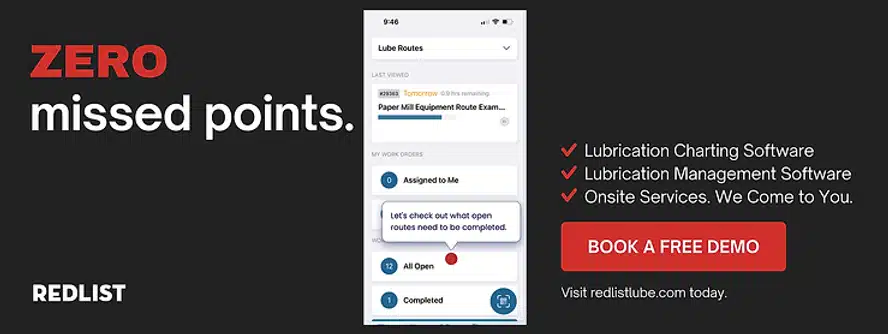
Planning is Key to Surviving a Supply Chain Crisis
Plan ahead for any oil changes if inventory levels can’t be kept at a certain level. Find an oil or grease that is compatible and whose operating characteristics are as similar as possible by working with your supplier. Compatibility testing in advance enables you to shift swiftly and informs you of the need to cleanse the systems or simply perform rolling changeouts. At the end of the day, these tips should help extend the life of your current lubricants. However, having a few backup options on hand in light of the current state of the market can prevent future issues.