The prevention and control of oil contamination result in significant savings on the costs of lubrication, machine repairs, and downtime. And awareness of the sources of oil contamination is the first step to preventing and controlling it. In our recent webinar with reliability expert Tim Dunton, we discussed the importance of contamination control in maintaining a successful lubrication program. The webinar is a mine of information on the fundamentals of oil contamination, and the sources and ways to prevent it.
In this post, we look further into the types and sources of oil contamination. Here, you’ll learn to identify the potential contaminants unique to your machine and process, thus helping you focus your efforts on controlling these contaminants.
Types of Oil Contaminants
Oil contaminants can come in the following forms:
Solids
The majority of solid oil contaminants are dirt, soot, metal particles, and soft insolubles. Dirt can come from the environment, such as soil, dust, and sand. Industrial processes can also produce dirt, such as concrete dust, fibers, clinker, and coal or coke fines. Being aware of your environment, processes, and operating conditions can help you better identify the sources of oil contamination in your facility.
Soot is the fine dust produced as diesel and similar fuels burn. Although very small, soot particles that dissolve in the oil can clump together and become large enough to cause damage.
Metal particles are products of the wear and tear of machine parts or when these parts slide, rub, or cut against each other. Solid contaminants are also produced when metal parts experience fatigue, erosion or corrosion, cavitation, polishing, fretting, and electrical discharge.
Soft insolubles are products of oil oxidation that naturally occur over time. The additives and base oil in lubricants can degrade and produce insoluble materials. Examples of these soft insoluble oil contaminants are sludge, varnish, lacquer, etc.
Liquids
The main liquid contaminant in lubricants is water. Water is present everywhere, in the air and even in the oil in small amounts. Water is present in lubricants at typical concentrations of below 100 ppm (parts per million) or 0.01%. Highly contaminated lubricants can contain water at 30% and above. Water decreases lubrication performance and promotes oxidation, the root cause of wear and tear in machines.
However, other lubricants can also serve as liquid contaminants. The presence of other lubricants results in cross-contamination, affecting the properties and lubricating performance of oils. When mixed, incompatible additives and base oils can react and decrease the viscosity, foam resistance, water separation, and other lubricant properties.
Next, fuel contamination can affect oil performance. Fuel dilutes the lubricants and decreases the viscosity, thus reducing lubricant detergency or cleansing power, wear protection, oxidation resistance, and acidic corrosion resistance. Extreme fuel dilution of oils can lead to operational failure due to low oil pressure and even explosion in the oil pan due to high oil volatility.
Another source of oil contamination to be aware of is coolant or glycol contamination. Coolant contamination leads to oil thickening, formation of corrosive acids and abrasive oil balls, additive degradation, and overall reduction of lubricating performance.
Lastly, cleaning chemicals used to wash down machines can also contaminate oil lubricants. These types of contaminants are common in processing equipment used in food and beverages that need to be cleaned and sanitized regularly. Frequent relubrication is recommended for these types of machines.
Gasses
This is a source of oil contamination you may not think of. But, air is the most common gas contaminant in lubricating oils. Gas is typically present in oils at 5% concentration and below. Too much air in oil results in an increase in oil viscosity, depletion of the additives, and speeding up oil oxidation. Air trapped in oil also promotes microdieseling, cavitation, foaming, rusting, corrosion, and formation of sludge or varnish, all these leading to physical damage to machine parts and functions.
Gas dilution can also be a form of oil contamination. Oils used in gas compressors can absorb natural gases or refrigerants. These gases react with the lubricants or dilute their lubricating properties.
Other Contaminants
Heat and radiation are other types of contaminants that can affect the performance of lubricants. Often overlooked, heat is the main cause of oil oxidation. At temperatures above 60℃ (140℉), a temperature increase of 10℃ (18℉) can double the rate of oxidation or oil degradation. High heat also decreases oil viscosity which decreases the lubricating properties of oils.
In nuclear power applications, radiation exposure can be a major type of contamination of lubricants. Oils for these types of applications must be resistant to radiation and maintain lubrication performance in case of exposure.
Sources of Oil Contamination
Knowing the above types of contaminants should give you an idea of their possible sources. Depending on your industry and machine types, a combination of these contaminants may be present. In general, oil contamination can happen during transport, storage, and use.
Transporting Lubricants
Contamination can happen even before you receive lubricants inside your facilities. In our webinar, Tim Dunton discusses the many sources of contamination during lubricant transport based on his first-hand experience. Transfer lines and transfer containers are major sources of solid and liquid contaminants. Tim also explains in the webinar how filtering oils is the first defense against oil contamination.
Storing Lubricants
Storage conditions also contribute to oil contamination. Unsealed storage containers, exposure to water and heat sources, and unclean storage practices are all common sources of oil contamination. Good warehousing practices (GWP) should apply to your raw materials and finished products as well as to your maintenance items and lubricants.
Using Lubricants
The majority of contamination of oil lubricants happens when they are used. Oils absorb heat and friction debris from machine parts. Solid and liquid contaminants also come from the processing environment, such as debris from manufacturing and water from steam or hydraulic systems. Maintenance managers should consider these in-process contaminants for effective lubrication management.
Controlling Sources of Oil Contamination
The effective control of the sources of oil contamination involves the processes of exclusion and removal. This is what Tim Dunton explains in the webinar as a 2-pronged attack.
In exclusion, you stop the contaminants from getting into the oil in the first place. And removal is where you get the contaminants out of the system as quickly as you can. An example of contamination removal is filtering brand-new oils before storage, and exclusion can be the use of sealed storage containers.
Optimized Contamination Prevention with Redlist
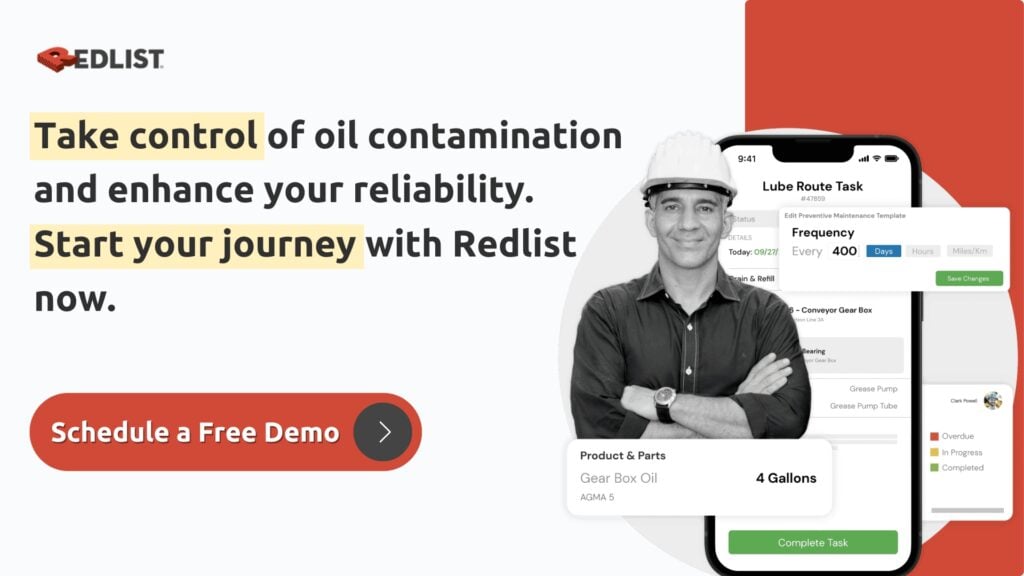
Effective lubrication management is easy with digital Lubrication Management Software, like Redlist. Redlist helps you evaluate the sources of oil contamination faster and better manage your lubrication status. Tracking and monitoring lubrication storage and application routes are digitized. Thus, historical data and other lubrication information are accessible whenever you need them to make valuable decisions. Redlist can also help you analyze and produce actionable results on your lubrication data. From there, you can improve lubrication processes and control issues such as oil contamination. Find out more about Redlist’s Lubrication Management Software by scheduling a demo today!