Every facility relies on equipment to carry out its daily tasks with high productivity and energy efficiency. Having machines and equipment prone to failures and malfunctions, i.e., having low reliability, results in expensive repairs and prolonged operation downtime. Predictive maintenance can significantly increase equipment reliability, thus, increasing productivity and cutting monetary losses for the company.
Predictive maintenance, or PdM, is the method that effectively identifies possible problems before they arise. The predictive maintenance of machines and equipment for manufacturing operations may involve oil analysis, vibration monitoring, and infrared imaging. Such procedures identify potential faults and provide actionable data to maximize equipment reliability.
Keep reading to learn about the essentials of implementing predictive maintenance and achieving equipment reliability for the success of your business.
What is Equipment Reliability in Manufacturing?
In manufacturing, equipment reliability is the capability of machinery or equipment to function consistently over time. Equipment reliability is also a measure of an equipment’s performance or whether a machine is operating at its optimum and providing consistent output without unexpected interruptions. A manufacturing facility’s productivity and costs are dependent on equipment reliability.
But equipment reliability does not mean zero failures or interruptions. In reality, even the most dependable equipment will undergo wear and tear and, over time, will need the necessary maintenance services. Equipment reliability means having a system that can proactively predict and delay the occurrence of such failures and interruptions. It also means having an adequate system that can handle these failures effectively and efficiently when they do occur.
To achieve optimum equipment reliability, facilities must execute proactive and targeted preventive maintenance procedures. These procedures should result in manufacturing operations that are on time, cost-effective, and have no major unplanned interruptions.
Poor Equipment Reliability & Consequences
Poor equipment reliability happens when a piece of equipment is not performing to its expected level, frequently fails and interrupts operations, and costs a lot to maintain and operate. The following are the consequences of poor equipment reliability:
- Expensive repairs
- Costly downtime
- Reduced overall productivity
- Dangerous working environments
- Not eco-friendly (high energy consumption or larger carbon footprint, and more waste products)
Measuring Equipment Reliability: Traditional Metrics
The following are the traditional ways that facilities can measure equipment reliability:
Mean Time Between Failures (MTBF)
MTBF is one of the most common measures of equipment reliability. The MTBF is the average amount of time that a machine or equipment functions in between failures or repairs.
To calculate MTBF, you take the total number of hours a machine or equipment is in operation and divide it by the number of failures. The higher the MTBF value, the higher the reliability of the machine.
You must maintain high MTBF values and develop strategies to improve machines with low MTBF. Note, however, that frequency of use is a critical factor that affects MTBF. You must consider that equipment seldom used can have low MTBF values.
Mean Time to Failure (MTTF)
Similar to MTBF, MTTF also measures the average time that a machine or equipment operates before it fails. MTTF, however, is applicable for machines that require system or machine replacement, while MTBF is for repairable equipment. You calculate MTTF by taking the total hours of operation and dividing it by the total number of those components or assets in your facility.
MTTF estimates the time it takes before you replace or retire a component or piece of equipment. It gives you valuable insight into the performance of equipment and machines. If your MTTF values are lower than the expected values of the equipment manufacturer, you might need to look into your operations and maintenance to improve MTTF values.
Availability Rate
The availability rate measures equipment reliability based on the ratio of available time to operation time. To calculate the availability rate, you take the total hours that the machine or equipment is running and divide it by the total operation time and multiply it by 100. For example, a machine that ran 9 hours during its 10-hour operation time would have a 90% availability rate.
The lower the availability rate, the lower the equipment reliability. A low availability rate may mean more time spent on repairs and downtime. But it can also mean other procedures are reducing the availability of the machine. For example, you can increase your availability rate by minimizing pre- and post-operational procedures whenever possible.
By calculating the availability rate, you also identify if a machine is exceeding its intended hours of use. Overworked units may need adjustment of operation hours and require closer maintenance attention.
Disadvantages of Traditional Metrics
While they provide valuable insights into equipment reliability, traditional metrics are seldom accurate in predicting failure and foreseeing issues to prevent expensive repairs. When using these metrics, therefore, facilities need to consider the unique characteristics of their machines, environment, and processing steps.
In general, traditional metrics can only collect data as the issue happens or after it happens, in most cases. Developing and executing maintenance decisions based solely on traditional metrics will not be effective in preventing early equipment failure.
Equipment Reliability: Advanced Solutions
Businesses now have access to innovative equipment reliability solutions. These solutions can provide a complete picture of a facility’s operations. They can also detect issues early enough to prevent or delay failure. These solutions utilize predictive analytics and machine-learning algorithms to anticipate when a problem will emerge.
The advanced solutions listed below work best when integrated into predictive maintenance (PdM). Maintenance programs focusing on PdM and utilizing these advanced technological data-gathering techniques are essential for optimizing equipment performance and minimizing repair and downtime expenses.
Infrared Imaging
Infrared imaging produces thermal maps of equipment to identify temperature spikes or dips, which can warn technicians of potential equipment failure. This technology can help you focus maintenance efforts on critical machines and assign inspection routes, allocate resources, and delegate workforce more efficiently.
Oil Analysis
Oil analysis is a method that involves testing the oil from a machine or equipment. Inspection and chemical analysis of this oil can identify potential problems such as premature wear and contamination. Early detection of these changes in the oil chemistry helps predict future issues and severe consequences. Your maintenance program should include a regular sampling of oil for oil analysis, the frequency of which depends on the criticality of your machines or equipment.
Vibration Monitoring
Vibration monitoring involves the regular checking and recording of equipment’s vibration levels. Changes in vibration levels can indicate potential issues that, if uncorrected, can lead to failure. The resulting breakdown would eventually lead to downtime and loss of productivity.
Computer-based Monitoring
Computer-based monitoring utilizes probes and sensors that monitor various indicators of potential issues. Such indicators include temperature, pressure, flow rate, current, etc. A valuable preventive maintenance technique, computer-based monitoring eliminates human errors during reading and testing. Thus, this technique can be an accurate, albeit more expensive, way to detect and prevent failure.
Ultrasonic Testing
Ultrasonic testing is a PdM technique that uses sound waves to detect changes in metal components that may signal possible problems. This technological testing is beneficial for detecting invisible but significant cracks and other structural flaws that can lead to failure. Incorporate ultrasonic testing into the maintenance program of machines wherein cracks and dents are critical indicators of potential failure.
Tips on Implementing Advanced Predictive Maintenance
As seen above, advanced PdM solutions can be valuable in enhancing equipment reliability. But these solutions are successful only if they are executed effectively. Below are some tips when implementing advanced PdM solutions for your facility:
Advanced PdM Techniques Rely on Your Maintenance Program.
\The advanced PdM techniques listed above will provide optimum results for equipment reliability only if they are part of a comprehensive maintenance and lubrication program. Regular oil analysis is useless if you do not observe basic procedures such as cleaning, lubrication, and contamination inspection.
Human Expertise is Required.
Advanced technological tools should work hand-in-hand with intuitive human expertise. Operators who have worked with their machines and equipment for years are sensitive to the intangible indicators of failure, such as the feel, look, or sound of the machine. These indicators, plus the accuracy of technologically advanced tools, can better predict failures and increase reliability than these tools alone.
Consider Technology Suitability.
Advanced technological tools and testing are effective and optimized only if they are suitable to your system and operations. Invest only in appropriate predictive maintenance technologies and trustworthy developers, analytics, or manufacturers.
Before investing in monitoring systems, vibration sensors, temperature probes, and computer software, you must ensure that these can work seamlessly with your system and current procedures. You can get the most sophisticated system and acquire the best tools. But, these solutions will be useless if they are difficult to integrate into your operations.
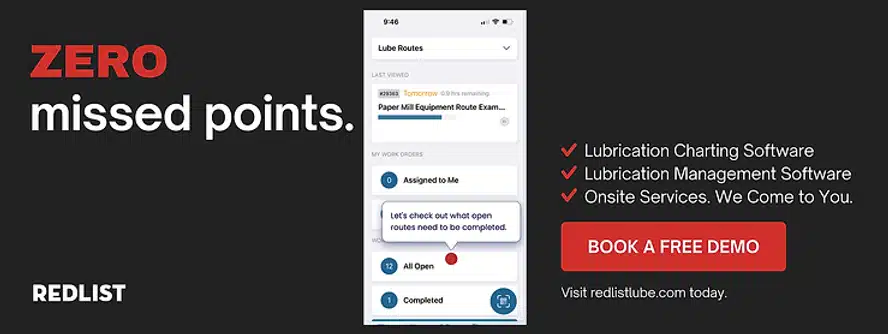
Advanced PdM Solutions with Redlist
Equipment reliability is the goal of any facility’s maintenance program. And equipment reliability is attainable through predictive maintenance that utilizes advanced technological solutions. Redlist is user-friendly, customizable, and intuitive, thus guaranteeing fast and easy PdM procedures. Additionally, Redlist integrates with a wide range of PdM tools and can evolve along with your maintenance program. Want to learn more about Redlist and equipment reliability? Schedule a demo with us today!