The U.S. Department of Energy estimates that more than 70% of industrial electricity consumption is for the use of electric motors. Motors rely on bearings, and bearings rely on good lubrication. Further, electric motors power 25% of all rotating equipment, which needs proper lubrication to last for long periods without fail or breakdowns. So, the right lubrication with the right electric motor grease can make a big impact on your lubrication management, asset reliability, maintenance costs, and equipment uptime.
How to Select the Right Electric Motor Grease
You must properly lubricate electric motors for equipment to operate effectively because they are so prevalent and play such a key role. Choosing the proper electric motor grease is the first step towards achieving that. Electric motor shafts rotate on bearings, much like any other moving part, which require lubrication. The main purposes of electric motor grease are to lessen friction and wear, shield the motor bearings from corrosion, and keep debris and moisture out of the bearings. Due to its properties and convenience of use, grease is frequently chosen as the best lubricant for this application.
Grease is simply a base oil (either mineral or synthetic), a thickening agent, and additives in the form of a semi-solid lubricant. Most electric motor grease contains mineral oil. However, synthetic oil-based grease is useful in situations with greater operating temperatures or when it’s important to maximize the time between re-greasing. The thickening agent is an essential component, as it stops the grease from leaking out of the system.
5 Electric Motor Grease Variables
It might be difficult to choose the proper grease for electric motor bearings because it is put through a variety of working circumstances, such as high and low temperatures, mechanical shear, exposure to corrosive substances, and exposure to moisture and pollutants. Therefore, the best electric motor grease for your applications should be chosen based on its physical, chemical, and performance traits. In general, go with the grease that the motor supplier recommends rather than the bearing supplier. Additionally, you can only use a select number of non-toxic greases for food preparation applications.
These are the properties to be aware of when selecting your electric motor grease:
- Viscosity is its most crucial component. Be aware that a mineral oil-based grease has a viscosity of 500–600 SUS (Saybolt universal seconds) in the majority of “normal” motor bearing applications. Consult your motor manufacturer for their suggestions.
- The consistency or firmness of the grease is the next aspect to take into account. This influences the pumpability of the grease, which determines if it will reach all the necessary surfaces. An index of grease firmness from 0 to 6 has been created by the National Lubricating Grease Institute. In motor bearing applications, you will frequently use an NLGI2 grade grease.
- Next is shear stability, which refers to the grease’s tendency to soften after usage. In the ASTM D217 Cone Penetration of Lubricating Grease test, the firmness of grease is evaluated after 100,000 cycles. A leak could develop if the grease softens excessively while in use.
- A good electric motor grease will have strong oxidation resistance over the range of temperatures it can operate at. This characteristic will help with adequate lubrication and lengthen the life of motor bearings. The ASTM D 3336 High-Temperature Grease Life test aids in determining the grease’s resistance to oxidation. The ideal grease has a long oxidation life.
- Finally, consider the grease’s dropping point. This is the temperature at which a grease starts to “melt” or break down. Basically, this is the point when the base lubricating oil starts separating from the thickener. After ensuring that it meets all other requirements, choose the grease with the highest dropping point.
Electric Motor Grease Additives
Some motors’ mountings result in an applied load on the motor bearings. Some greases are infused with anti-wear compounds to lubricate against this load. These are extreme pressure (EP) additives. Choose a grease without extreme pressure additives unless you need them because these compounds reduce the usable life of a grease.
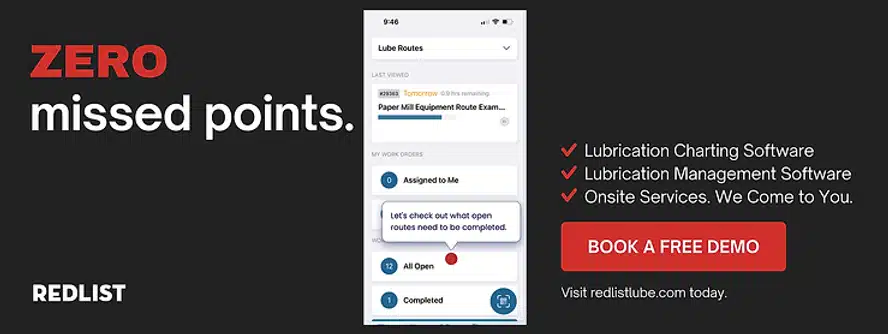
Lubrication Mistakes to Avoid
Cross-contamination, using the incorrect electric motor grease, over-, under-, and no lubrication at all are all typical issues that can result in early electric motor failures. A busy operator or technician may grab the wrong grease gun and use the incorrect grease on the electric motor. The results of mixing incompatible greases can be disastrous, with a considerable decrease in grease performance eventually leading to bearing failure. You can greatly improve the protection and functionality of bearings by choosing the proper electric motor grease and optimizing your electric motor grease lubrication.