In this age of increased global competition, facilities must adapt to remain competitive and financially viable. Cost-cutting methods like facility closures and employee layoffs are common because market prices and raw material costs are beyond a facility’s control. But, cutting costs through these methods is not enough. Improving reliability is crucial to improving cost and productivity. One of the key concepts in optimizing operations and asset reliability is operator-driven reliability or ODR.
Where to Begin with Operator-Driven Reliability?
To understand operator-driven reliability, we first consider the operator. The operator once worked “on the floor,” but this position was altered when we developed technologies that lessened production costs and increased yields. As a result, the operator now works closely with these technologies or equipment that do the work.
Consequently, the operator now has hands-on knowledge of said equipment or assets. In addition, the operator’s experience using these assets is valuable in developing reliability systems that monitor efficiency and predict failure.
Operator-Driven Reliability Basics
The “operator-driven” in ODR means that the operator’s valuable but sometimes unmeasurable insight into their equipment is reintegrated into the reliability program. With operator-driven reliability, the maintenance team can transfer basic inspection tasks to the operators who use the assets. This way, operators not only operate but also “own” their equipment. Much like you are responsible for keeping your car running, the operators are responsible for keeping the process equipment in their areas operational.
At this point, it is critical to note that this concept of operators’ ownership doesn’t mean sole responsibility or that you leave every man for himself. Techniques such as vibration analysis, infrared thermography, and preventive maintenance programs should still be in effect.
Implementing Operator-Driven Reliability
Now that you have a clear idea of what operator-driven reliability is, how do you implement it in your facility? Believe it or not, deciding whether to implement ODR is the most challenging aspect. With targeted resources and a well-defined timeline, this program can produce the desired financial outcomes.
Here are the steps for implementing ODR in your facility:
1. Secure management support
The most critical aspect of a successful ODR program is management buy-in. With backing from the top levels of the business, the program will obtain the resources, time, and support necessary for success.
2. Formulate mission and objectives
The next step is to identify what your ODR program is trying to achieve. It should include program metrics, goals, budgets, and facility-wide roles and responsibilities, developed by your leadership team.
3. Designate a champion to manage the implementation
Choose a candidate that is very visible and a highly regarded figure, as they will be managing mostly through influence. Thus, they will also need to possess strong leadership and team-building skills. To make it easier for the champion to navigate the particular political areas of their designation, this individual should be recruited and promoted as the program’s implementer within the facility as soon as possible.
4. Define ODR champion responsibilities and limitations
The champion for implementing the operator-driven reliability program is responsible for identifying and resolving bottlenecks in the facility, updating the leadership on the program’s progress, selecting a team to administer the program, and maintaining program visibility and expectations.
5. Identify key operational areas and pick a team member to represent each area
The ODR implementation champion will perform this step. The areas and personnel identified will depend on the facility and the processes involved. As with the program champion, team members should be well-respected in their respective fields, self-motivated, and able to work on numerous jobs simultaneously.
6. Identify equipment and operator routes
The chosen team member from each key operational area will identify the equipment that will be placed on operator routes, determine the walking order of the routes, and establish the inspection frequency. In addition, the team members are accountable for the area metrics, the area communications plan, the identification of analytical tool requirements, and the departmental recognition plan.
7. Maintain communications plan
With an effective communications plan included in your ODR program, you ensure that your operators and involved personnel are consistent and committed to the program. An effective communications plan should consist of well-defined rules and responsibilities, scheduling routes and follow-up paperwork, a feedback system, expectations, training, and how recognition will be handled in the area, regardless of the techniques used.
ODR Challenges: Analytical Tools
One of the most common reasons ODR implementations fail is issues with analytical tools and the expenditures and training connected with them. Most facilities utilize a comprehensive suite of analytical tools with benefits such as more precise readings, improved methods for reporting exceptions, real-time data trending in the field, lessening operators’ tendency to “pencil whip” data, and lending credibility to a new program.
Although a comprehensive suite of analytical tools is recommended, it is not essential in starting your ODR program. You may choose to incorporate tools in the future as your program and requirements evolve.
Nevertheless, the following is a list of some equipment that could assist you and improve your data collection.
- Infrared Temperature Guns – Without coming into contact with potentially hot equipment, operators can record accurate temperature readings.
- Vibration Pens – Although it requires the same point and angle for accurate trending, vibration pens allow operators to check the condition and trend bearing vibration levels.
- Stroboscopes – For in-service rotating equipment, stroboscopes help operators identify loose couplings or belts, missing bolts, or material defects.
- Smartphones or Tablets with CMMS – CMMS (computerized maintenance management system) software that is accessible on any mobile device will provide support for faster digital inspections, bar code scanning, electronic route compliance, and more.
ODR Challenges: Development of Routes
Another area that needs attention when implementing operator-driven reliability is route development. Understanding your process routes and which equipment to include form the foundation of effective ODR implementation. Additionally, neglecting the transition between pieces of equipment can pose a challenge to effective ODR implementation. Therefore, your ODR champion and team leaders need to design routes that allow enough time for the operators to examine equipment problems during these transition times.
Furthermore, the development of routes should also consider the current responsibilities of the operator. Collecting data is not their main responsibility and, thus, should not take up large chunks of their time. Fast and user-friendly analytical tools paired with a CMMS would significantly lower operators’ extra time complying with the ODR program.
Finally, your ODR program can also be affected by your assigned route frequency. Ideally, frequent routes will let you catch all failures before they occur. But doing so is not cost-effective as it requires additional personnel and downtime. Hence, your route frequency can prioritize the most likely failures and adjust according to the occurrence and trends of future failures.
Based on our experience, routes are also much easier to handle when all equipment is examined at the same time, rather than using separate route frequencies for different pieces of equipment within an area. Also, many teams find it useful to choose your frequency through trial and error. You can start by running the routes weekly. Then, detect any inspection that was left off the route and include it in the succeeding week.
ODR Challenges: Training
Your operator-driven reliability program can also neglect the fact that operators need adequate training for the said program to be effective. It is easy to launch your ODR program, assuming that an operator’s familiarity with their equipment makes them experts in collecting inspection data. Often, this is not the case. Even operators who know their equipment by heart need to orient themselves with analytical tools and management systems before they can effectively use them.
Also, operators need to align their knowledge of equipment, parts, and processes with the information on the ODR program. For example, you may come across operators who use names for parts different from those in your CMMS.
Another issue that proper training can resolve is the turnover of information between operators who use the same equipment. Not understanding the purpose of taking data from their equipment, these operators won’t effectively transfer data and recommendations to their “co-owners.”
Effective ODR program implementation requires training operators and their managers in these areas:
- Routes
- Analytical Tools
- Inspections
- Forms / Recordkeeping
- Area Communications
You can also organize a hands-on route walking or trial run of the whole process. This will be valuable for the operators and managers, allowing them to experience the program and raise their questions and concerns before ODR implementation.
ODR Challenges: Sustainability
Your ODR program must become ingrained in the facility’s culture to be effective and viable. Operators should find it easier to handle their equipment failures. If they find the program an added burden to their workload, sustainability will be a problem.
To be sustainable, any ODR program must extract constant input from the operators and adapt to them. It is called ‘operator-driven’ after all. Your ODR program will need sufficient time to transfer resources before it gains sufficient momentum. The goal is for the respective key areas or departments to acquire responsibility for maintaining operator-driven reliability routes.
Recognition and incentives can also further support ODR implementation. For example, giving out departmental awards or gift certificates for ODR-complying employees can be a great way to sustain the program’s awareness and reinforce the area’s efforts to foster operator ownership.
ODR Challenges: Housekeeping
The implementation of an effective ODR program is closely tied to housekeeping. After all, you can link many equipment failures to unclean and disorganized equipment or work areas. Improper cleaning of equipment causes higher temperatures, undetected leaks, and other costly equipment failures.
If your facility already has a housekeeping expectation and culture in place, it may not be a considerable challenge. However, disregarding your housekeeping policies and schedules when implementing your ODR program can cause issues down the line.
Implementing your ODR program should involve an adequate review and confirmation of current cleaning and housekeeping responsibilities. This way, your operators and related personnel will have a clear understanding of their cleaning duties, preventing finger-pointing when cleaning is not done. The best way to address any housekeeping issues is during the training of operators and their managers.
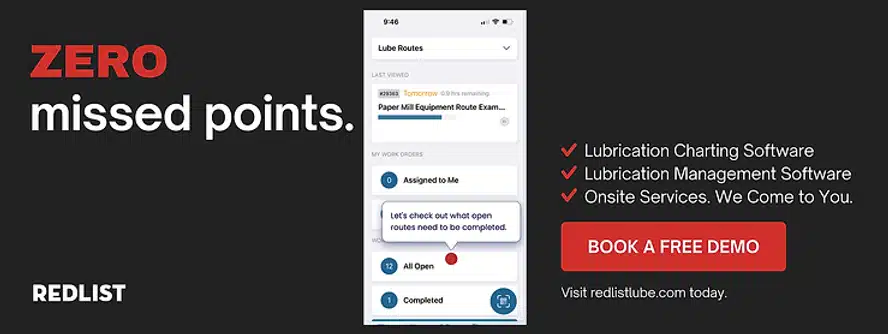
Success in Operator-Driven Reliability
The concept of ODR is gaining popularity for a reason. It is one of the best ways facilities can maximize their assets, improve productivity, and minimize costs. The steps outlined here are simple and straightforward, but as with all steps in a program, they need effective implementation and follow-through.
We at Redlist understand how daunting it is to develop and implement new programs. During the development of CMMS software and lubrication management, we have seen companies struggle before reaching their reliability and maintenance goals. We hope this article has given you the information you need regarding operator-driven reliability. Please feel free to contact us if you have further questions or browse our blogs for other helpful topics. We wish you success in your ODR program implementation!