Many of the organizations we have worked with recognize how critical lubrication is in the optimal performance of their assets. It is the reason they come to us in the first place. But with our lubrication management experience, we have met our fair share of lubrication myths that often hinder our clients from reaching their bottom line. We have put together these common myths in this post and try to shed light on each. Understanding these common lubrication myths may help you avoid them to reach your lubrication goals and achieve optimal performance for all your assets.
#1: Equipment lubrication is a simple task.
Lubrication is often seen as a simple task of applying and reapplying oil or grease. But simple tasks are often the easiest to take lightly and thus are more prone to mistakes or errors. Very few organizations research their lubricant choices thoroughly, standardize their lubrication application method, provide technical training for applying lubricants, or consider all the factors that affect the success of lubrication. Hence, most lubrication measures are a wild guess, the success of which is never tested or confirmed.
For lubrication to be successful in increasing asset productivity and lifespan, it must follow the “Five Rights of Lubrication,” which means: the right lubricant at the right place, right amount, right time, and using the right procedure. Following these five rights is not meant to complicate the simple task of lubricating machines, but it should ensure that lubrication delivers the results that it is meant to deliver. And that you get the optimal benefits from investing in lubrication expenses.
#2: Lubrication plays a small role in asset maintenance.
Because lubrication is often a routine task in asset maintenance, it is seldom prioritized or given careful attention. As a result, lubrication’s impact on asset performance and reliability is often missed. In recent research, root cause analysis shows that the bulk of mechanical, bearing, and equipment failures can be traced because of wrong or inadequate lubrication.
Once you recognize the critical role of lubrication in asset maintenance, you can target costly and complex asset issues at the root cause level. As a result, you can save on the costs of maintenance and related operational losses.
Lubrication Myth #3: Lubrication expense reduction is possible by limiting lubricating tasks.
It is also a common misconception that reducing the application of lubricants results in reducing lubrication expenses. However, limiting lubrication without proper evaluation often leads to more expenses due to increased machine failures, more spare parts replacements, extended downtime, and lower productivity.
Efforts to lower the lubrication budget do not start with buying less lubricant or applying them less frequently. Instead, these efforts should start with looking into current lubrication measures and identifying ways to improve on them. Thus, you can plan cost-cutting methods such as replacing current lubricants with cheaper but equally effective brands or using the lowest yet still effective lubricant levels.
Lubrication Myth #4: Lubrication products are all the same.
Lubrication is not a one-size-fits-all process. What works for one does not always work for the other. Many facilities we have worked with often use one type of oil or grease for their wide range of assets. Most machine technicians and operators even use the same products for different machine parts at similar levels and application frequencies.
Lubrication products are made up of different formulas for varying applications. A lubricant’s components, functional properties, performance, and other characteristics should be applicable to the asset and its intended uses. To illustrate, a machine used in food manufacturing should use food-safe lubricants, especially for parts that encounter food. Otherwise, facilities risk food safety and regulatory compliance in their operation, not to mention the potential asset damage from using inappropriate lubricants.
Lubrication Myth #5: More lubricant is better.
More lubricant is not always better. Too much grease in the bearing, for example, is a major cause of bearing failure. Most facilities make the mistake of applying substantial amounts of lubricants to save time in replenishing or reapplying them. In fact, over-lubrication not only wastes lubricants but also promotes wearing, contamination, heat and stress build-up, and high energy usage.
The use of automated lubrication systems is a valuable way to control over-lubrication and maintain optimum levels of lubricants. Controlling over lubrication for manual lubrication can be done through proper personnel training, the use of standard lubricating tools, and regular monitoring of lubricant levels.
Lubrication Myth #6: Some grease colors are better than others.
Grease colors are identifiers of type and properties, but they do not guarantee effectiveness. As such, blue grease can only be better than white grease if its base oil, additive, viscosity, and other properties are applicable to its intended use. Colorants are simply for quick identification and safety from incorrect usage, not as markers of quality. What color you use still comes down to the properties of the lubricants and your specific asset requirements.
Lubrication Myth #7: Tacky and viscous lubricants are better.
A lubricant works by creating a thick film between surfaces, which is possible through its tacky or viscous properties. But as in the case of too much lubricant, too much viscosity can also result in damaging effects on assets.
Lubrication Myth #8: Lubricants must always follow the manufacturer’s recommendations.
Using a lubricant recommended by the makers of a machine or equipment is always a good start. However, the type and usage of lubricants may vary depending on the actual working conditions the machine is subjected to. Thus, if the manufacturer’s recommendations are not applicable or fail to provide the expected results, it is the user’s responsibility to adjust their lubrication accordingly.
Optimize Your Lubrication Management with Redlist
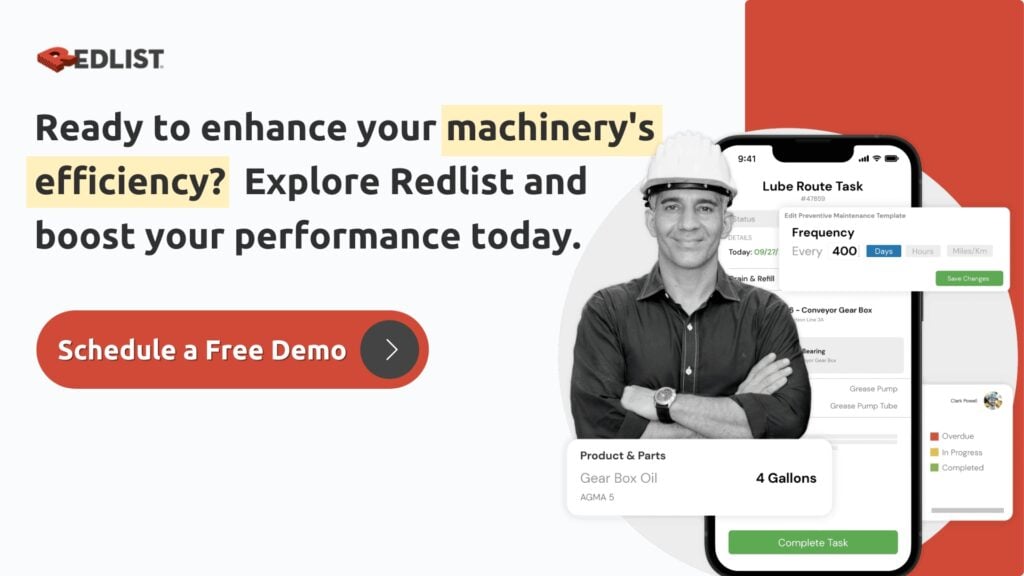
The above are only some of the more common myths and misconceptions in lubrication management. Facilities must rely on proper research and study their actual process to overcome these misconceptions and prevent their negative consequences. And this is easily done with Lubrication Management Software. With Redlist’s all-in-one lubrication management support, lubricant selection, planning, monitoring, analysis, and reporting are simple, effective, and efficient. Request a free demo and experience Redlist today!