Unexpected equipment failure is a constant challenge for any organization in any industry that relies on equipment. Businesses must deal with this challenge to maintain excellent operating conditions, minimize downtime, and optimize productivity.
One of the most effective strategies used in dealing with equipment failure is Failure Mode and Effects Analysis (FMEA). Originally developed by the aerospace and automotive industries, FMEA has since become a cornerstone in ensuring safety and reliability in various sectors, including manufacturing, healthcare, and energy.
In this post, we’ll explore Failure Mode and Effects Analysis as a powerful tool in achieving maximum equipment reliability. We will delve into the different types of FMEA, outline the steps in conducting FMEA, and discuss the best practices to ensure effective results.
Whether you’re a seasoned reliability engineer or new to the concept, this guide will equip you with the knowledge and insights needed to implement Failure Mode and Effects Analysis successfully in your organization. If you prefer watching and listening instead of reading, head over to our recent webinar entitled How to Get the Most Out of Your Reliability Program with FMEA.
What is Failure Mode and Effects Analysis?
Failure Mode and Effects Analysis (FMEA) is a systematic and proactive approach in engineering and maintenance. This approach aims to identify failure modes, i.e., the ways something might fail, assess their impacts, and prioritize actions to reduce risks. FMEA is vital when maximizing equipment reliability because it helps in proactively addressing possible issues before they lead to major disruptions.
Why Conduct FMEA?
Below are the essential benefits of conducting Failure Mode and Effects Analysis:
- Improved equipment reliability – FMEA helps identify and address potential failures before they happen, thus ensuring that equipment and machinery operate optimally within their intended lifespan.
- Cost savings – FMEA deals with failures before they lead to costly repairs, downtime in operations, and equipment replacement purchases.
- Improved safety and compliance – FMEA enhances the safety of operations by dealing with potential equipment failures before they result in unsafe working conditions. In some industries, implementing FMEA is a critical requirement for regulatory compliance.
Types of FMEA
The following are the common types of Failure Mode and Effects Analysis used depending on the industry and operational requirements:
Design FMEA (DFMEA)
The purpose of DFMEA is to identify and address the potential failure of a product or system before it enters into production. Through DFMEA, designers and engineers can detect design flaws that can lead to equipment failure, safety hazards, or performance issues. Thus, these flaws can be improved, ensuring that the final products meet the expected quality and reliability standards.
Process FMEA (PFMEA)
The primary focus of PFMEA is the failure modes within the production or assembly process. PFMEA can identify and address process-related defects, inefficiencies, or safety issues by analyzing the risks of failure caused by process variances, equipment performance, or human error. PFMEA is typically applied while planning and validating a process to ensure that it is capable of producing high-quality and consistent products.
Functional FMEA (FFMEA) or System FMEA (SFMEA)
FFMEA examines the potential modes of failure within complex systems, focusing on how different components and subsystems interact or function together. Conducting FFMEA or SFMEA helps in understanding how failures in one component or subsystem propagate to other parts to cause major systemic failures. FFMEA or SFMEA is typically applied in complex systems like those used in aerospace, defense, or automotive industries.
Service FMEA
Service FMEA is the type of FMEA that focuses on identifying potential failure modes in service operations and maintenance activities. The primary goal is to enhance the reliability and quality of services by identifying and addressing potential failures in the service processes. This type of FMEA is typically applied in industries where service reliability is critical, such as healthcare, IT, and transportation.
Software FMEA
Software FMEA focuses on software systems that are critical to the operation of hardware or other systems. This type of FMEA aims to analyze sources of software failures to ensure the reliability of software systems and the systems using them. Software FMEA is implemented during software development and involves identifying bugs, logic errors, or compatibility issues that can lead to significant risks of software failures.
Steps in Conducting FMEA
The benefits of Failure Mode and Effects Analysis depend on the successful implementation of the following steps:
1. Define the FMEA scope.
Identify the product, system, component, or process to be analyzed. Also, you must define the boundaries and objectives of the Failure Mode and Effects Analysis to be conducted.
2. Assemble the FMEA team.
Assign the team members to be involved in conducting the FMEA, including representatives from various departments within the organization. Include members from the engineering, maintenance, quality control, and other departments to ensure that different perspectives and expertise are considered.
3. Identify the failure modes.
List all potential failures that can arise within the system or process. Consider every source of failure, no matter how unlikely they are to happen.
4. Analyze the effects.
Assess the identified failure modes and their consequences on the system or process. Evaluate the severity of these consequences based on their impacts on the reliability, safety, and performance of the system or process.
5. Identify root causes.
Determine the causes of the failure modes. This may include looking into design flaws, process variations, or human errors.
6. Evaluate controls.
Identify current controls or measures that prevent the failure modes from occurring. Evaluate the effectiveness of these controls and identify the strengths and areas of improvement, if any.
7. Assign Risk Priority Numbers (RPN).
Establish and follow an RPN system that ranks failure modes based on the severity, occurrence, and detection ratings. Use the RPN assignments to prioritize the failure modes that require the most urgent attention.
8. Develop action plans.
Create strategies to minimize or eliminate high-RPN failure modes. Consider making design changes, process improvements, proactive maintenance, etc.
9. Implement and monitor.
Implement action plans and monitor their effectiveness by data-gathering. Improve the FMEA as new data, insights, or changes become available.
FMEA Best Practices
To ensure the effective implementation of FMEA, the following are the recommended best practices:
- Update regularly – FMEA should be a living document that must be updated and revised as new information about the system or process comes to light.
- Document thoroughly – FMEA relies on the thorough documentation of all processes and decision-making steps. Clear and complete documentation ensures a transparent and traceable FMEA.
- Integrate with tools – FMEA works best if integrated with other reliability tools, such as Root Cause Analysis (RCA) and Reliability-Centered Maintenance (RCM).
- Train regularly – All team members must be trained about FMEA information and its importance. Regular training helps update the members’ knowledge and improve FMEA efforts.
FMEA Real-World Applications
Failure Mode and Effects Analysis has been adopted in various industries to enhance equipment reliability and performance. Here are some real-world examples demonstrating the effectiveness of FMEA in achieving reliability goals:
Example 1
An automotive company produces a component that is showing high numbers of recalled units and failure complaints, damaging the company brand and lowering total sales. The company conducted FMEA to identify the failure modes of the design and the production process. The analysis revealed that the design was sound, but the material used to make the component was not thermally stable. The team prioritized changing the material to a more heat-stable one. The outcome of the FMEA is a change in the component material and a reduction in failure rates. Ultimately, the company saw an overall decrease in failure complaints and warranty claims for the component.
Example 2
A manufacturing plant producing electronic parts is experiencing high downtimes due to the failures of the assembly line’s robotic arms. The company conducted an FMEA to evaluate the failure modes associated with the equipment. Data on recent failures show that the high downtime is mainly caused by the misalignment of the robotic arms, which in turn is caused by the normal wear and tear of its critical components. The company identified that this wear and tear is a high-priority failure mode and developed effective maintenance schedules and component upgrades to prevent constant misalignment. Thus, the process downtime due to robotic arm failure was significantly reduced. Ultimately, the company increased its production efficiency and boosted its productivity.
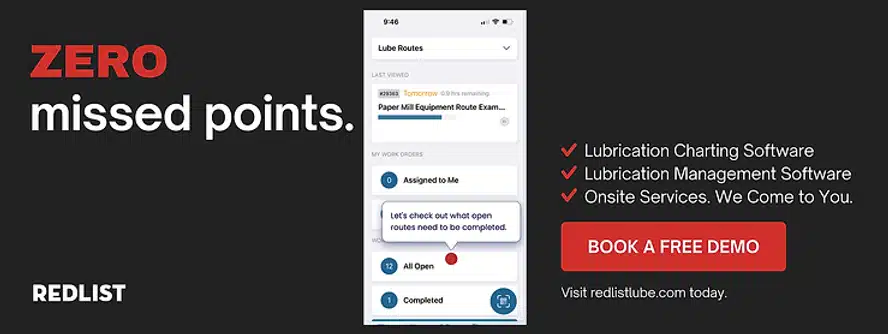
Conduct FMEA with Redlist
Through Failure Mode and Effects Analysis, organizations can systematically identify and address potential failures and achieve their reliability goals. However, conducting an FMEA can be a complicated process involving departmental processes that are prone to errors and miscommunications. With a cloud-based and digital platform like Redlist, a streamlined and accurate FMEA implementation is within your reach.
Redlist supports FMEA through its centralized documentation of FMEA-related documents, data, and analysis, ensuring accessibility of up-to-date information and collaboration among team members. Redlist can also automate the calculation of RPN and prioritization, streamlining the FMEA process and allowing teams to focus on high-risk areas efficiently. Redlist’s all-in-one platform also allows teams to create action plans, track their progress, and monitor effects.
For more FMEA-related information, listen to the complete webinar here. To experience a headache-free FMEA implementation, contact our reliability experts for a free Redlist demo.