Equipment failure is one of, if not the most, critical challenges that reliability engineers face. If unmanaged, equipment failure can lead to reduced productivity, high operational costs, increased downtime, and poor safety. By understanding the top causes of equipment failure, reliability engineers can develop strategies to prevent them. Ultimately, this will reduce the occurrence of equipment failure and its negative impacts on the business.
Understanding Equipment Failure
Equipment failure is any instance when a machine or equipment partially or completely fails to perform its intended functions. This comes in many forms and levels of severity, from small issues or decreased usefulness to full non-operational conditions. Equipment failure can be categorized into three types based on their occurrence patterns:
1. Sudden Equipment Failure
This type of failure happens abruptly and without warning. Sudden failures typically result in immediate and total loss of function and often cause significant disruptions to operations.
2. Gradual Equipment Failure
This type of failure develops over time with progressive deterioration. Gradual failures often show tell-tale signs such as decreased performance, visible damage, or abnormal noises. These signs warn operators and allow maintenance or repair before total failure or breakdown.
3. Intermittent Equipment Failure
This type of failure occurs occasionally at irregular intervals and is unpredictable. Intermittent failures are often temporary and the equipment can return to normal function afterward. The unpredictable nature of intermittent failures makes them challenging to diagnose and manage.
How to Prevent the Common Causes of Equipment Failure
Professionals like reliability engineers tasked with ensuring the optimum performance, availability, and maintainability of assets must know and understand the following top causes of equipment failure. You can use this list as a guide when investigating the root causes of these failures. Understanding the root cause of equipment failure is the number one step to prevention! This allows you to develop strategies to predict, prevent, or at least minimize their future occurrence.
Physical Factors
Equipment that is put to regular use will inevitably experience physical degradation that leads to failure. Some common examples of these physical factors include:
- Wear and tear – mechanical components undergo wear that decreases a machine’s ability to function properly or perform optimally
- Fatigue – subjecting equipment to repeated stress cycles can also lead to material fatigue and failure
- Electrical – issues like short circuits or power surges cause damage to mechanical components
- Contamination – moisture, dirt, dust, and other foreign materials can enter equipment and cause damage
Being inevitable, the best way to control these physical factors is to watch out for their appearance and fix them before they lead to failure. Reliability managers should implement routine inspections that will help identify these physical factors and repair or replace the relevant machine parts as necessary.
Operating Errors
Every equipment has its set of operating conditions and procedures that ensure its optimum performance and long lifespan. Not following these standard procedures or recommended conditions can lead to operating errors that result in damage, and ultimately, equipment failure. Such operating errors can come in the form of:
- Overloading – going beyond the set loading capacity leads to excessive stress that causes damage and failure
- Incorrect assembly – incorrect assembly causes parts to misalign leading to uneven wear and eventual failure
- Human error – operators, maintenance technicians, and other people who work with equipment can cause damage to it by not following set operating or maintenance procedures
To prevent equipment failure due to operating errors, reliability managers must develop and strictly implement Standard Operating Conditions (SOPs) to ensure correct, effective, and safe equipment operation and maintenance.
Mismanaged Resources and Assets
Several materials, spare parts, expert labor, and other resources are required to maintain the optimum performance of equipment. Not maintaining the availability or proper condition of these resources can lead to decreased performance, and ultimately, failure.
Furthermore, not having a close eye on the equipment or asset itself can promote failure. Tracking the location, usage, condition, and other relevant equipment information helps identify discrepancies and irregularities that determine the need for pre-failure maintenance and other measures of failure intervention.
Therefore, reliability managers must develop and implement strategies for efficient resource management like monitoring inventory levels, planning maintenance tasks, and tracking technician schedules. In addition, reliability managers must also include asset tracking and condition monitoring for asset visibility and more effective maintenance.
Incorrect Maintenance
It’s a fact that maintenance procedures play critical roles in preventing or keeping equipment failure under control. However, these procedures must be performed properly and efficiently to be beneficial. Below are some of the key maintenance areas that reliability managers must consider when dealing with equipment failure:
- Lubrication – It is a key maintenance task that has a major impact on the longevity of equipment parts. Proper lubrication management involves the appropriate selection, storage, handling, application, and monitoring of lubricants to ensure that they are effective in reducing friction and wear that cause equipment failures.
- Preventive Maintenance (PM) – This is a popular maintenance strategy that involves regularly scheduled inspections, parts replacements, minor repairs, cleaning, calibration, and other tasks necessary to prevent equipment failure. A robust PM program should be adequate to prevent equipment failure but not too much that there are wastes on technician’s time, spare parts, materials, and other resources. If implemented properly, PM strategies help minimize Corrective Maintenance (CM) or maintenance that is performed only when failure occurs.
- Predictive Maintenance (PdM) – PdM is a maintenance strategy that helps predict equipment failure through the use of technologies like sensors, the Internet of Things (IoT), data analytics, etc. To be effective PdM strategies must collect data correctly and analyze these promptly for immediate and relevant decision-making.
- Condition-Based Maintenance (CBM) – This strategy is similar to PM in that it helps identify and prevent equipment failures before they happen. It also uses technologies similar to PdM in monitoring equipment conditions. What sets CBM strategies apart from the other two is that the maintenance tasks and schedules are assigned according to the equipment’s current conditions and maintenance needs. CBM is a more focused form of PM that uses PdM technologies, i.e. it relies on data to target specific equipment issues. CBM is best implemented with a digitized and automated system that allows fast and accurate transfer of information and sophisticated computer analytics.
Inadequate Training
Maintenance consists of a complex interplay of tasks and activities the management of which can be time-consuming and prone to errors. Everyone involved in creating and implementing maintenance strategies and programs must have the relevant skills and knowledge to ensure the success of these strategies.
Undergoing training is one of the best ways to develop people’s skills and expand their knowledge. In addition, training helps minimize human errors that can cause equipment failure. Training technicians, for example, will promote their skills in executing error-free repairs and promote their awareness of PM strategies. Equipment operators and supervisors also need regular training to keep them updated on equipment usage and SOPs.
Absence of Reliability Culture
A reliability culture refers to the mindset within the organization where reliability is the priority in operations, maintenance, and decision-making processes. The absence of such a culture promotes equipment failure. It is the critical role of reliability managers to cultivate this culture through:
- Leadership – involves leading by example, developing policies, and improving resource allocation
- Reliability strategies – including developing and implementing robust maintenance strategies like PM, PdM, and CBM
- Training and education – means supporting training programs on reliability principles and best practices
- Tracking metrics – involves analyzing data and monitoring reliability metrics like Mean Time Between Failures (MTBF) and Mean Time To Repair (MTTR) to push for continuous improvement
- Collaboration and employee involvement – supporting the sharing of information, working together among different departments, and soliciting the contribution of all employees in aiming for high reliability in all assets.
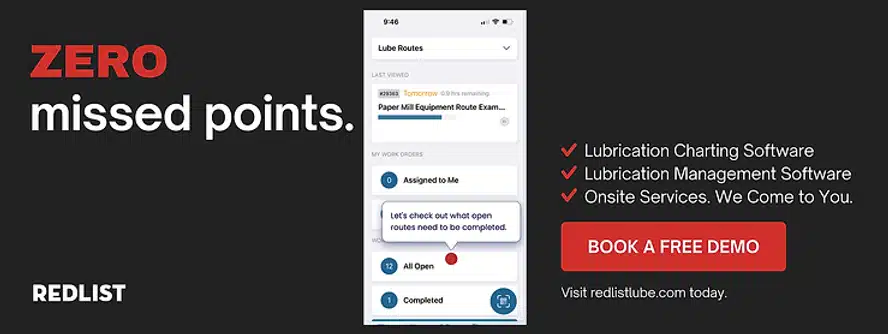
Equipment Failure Management with Redlist
Redlist provides the ultimate equipment failure solutions through its sophisticated and genuine Computerized Maintenance Management System (CMMS) and Lubrication Management Software (LMS). Using these solutions helps reliability managers keep on top of every critical maintenance area and prevent equipment failure through:
- Digitized data collection and storage
- Mobile access and cloud-based data sharing
- Automated task scheduling
- Integration with other management systems
- Connectivity with sensors and monitoring devices
- Data Analytics
Experience the benefits of Redlist’s solutions firsthand. Schedule your free demo today and empower your maintenance team to ensure your equipment runs smoothly, efficiently, and reliably!