Since the pandemic, many companies are experiencing the impact of global supply chain issues. Before, when an asset broke down, you could get a spare part in a few hours. Now, it can take weeks for parts to come in, which greatly extends unplanned downtime. To counter the lengthy lead times, maintenance departments have to shift their inventory management to be more proactive and less reactive. But, how do you take a proactive approach to spare parts inventory when you can’t predict equipment failure? The answer is not to start stocking up on everything. Instead, you can find the right balance for your business by tracking these top maintenance inventory metrics.
Stockouts
Stockouts Percentage = (# of inventory requests with stockout / total # of inventory requests) X 100
This metric is more important than ever because it’s the key to navigating supply chain issues. Stockouts occur when a technician needs a part and you don’t have it. Looking at historical inventory data to determine stockouts will guide you to what parts you need urgently the most. Then, you can take that list and see what the current lead times are. If any of those parts take weeks to get instead of hours, then you should consider ordering them now.
As a metric, your goal should be less than 2%. It is challenging to determine your optimal inventory level and reduce stockouts. This is why you have to look at more than one metric. You should consider stockouts alongside your inventory turns.
Inventory Turns
Inventory Turns = cost of purchased inventory over a set period / cost of current inventory
You can measure inventory turns over any amount of time to determine how long your inventory is sitting in the storeroom. Typically, a lower value is a slow-moving inventory, and a higher value is a fast-moving inventory. Alternatively, a lower value may mean that you overstock your inventory. Different parts will have different goals for inventory turns. Spare parts for critical assets that you keep on hand just in case will have a low inventory turn, which is acceptable for their purpose. You will see a high inventory turn for other parts or consumable materials. Your goal should be a value of 3 when you exclude critical spares or a value of 1 when you measure all inventory types.
Combining your analysis of stockouts and inventory turns will help you identify overstocking issues. A low stockout value is ideal. But, when the part also has a low inventory turn, you may have an overstocking issue.
Inactive Stock
Inactive Stock Percentage (Based on Records) = {[# of inactive inventory records – (critical spare records + non-stock records)] / [total # of inventory records – (critical spare records + non-stock records)]} X 100
Inactive Stock Percentage (Based on Cost) = [(cost of inactive inventory – cost of critical spare inventory) / (total cost of inventory – cost of critical spare inventory)] X 100
Whichever way you decide to calculate your inactive stock metric, it measures your inventory that has been sitting unused for a year or more. This is an essential metric for managing your spare parts budget and working capital. However, this metric excludes your critical spares and non-stock materials that are not physically stocked but are in your inventory records.
Vendor-Managed Inventory
Vendor-Managed Inventory Percentage (Based on SKUs) = (# of vendor-managed inventory / total # of inventory) X 100
Vendor-Managed Inventory Percentage (Based on Cost) = (cost of vendor-managed inventory / total cost of inventory) X 100
If your business is feeling the impact of supply chain issues, then vendor-managed inventory (VMI) is both a solution and a metric. First, some vendors offer VMI to help their customers optimize their inventory levels. With VMI, the vendor maintains an agreed-upon inventory of the part or material for you. Depending on the part and vendor, this may solve your supply chain issue. But, the vendor may also have supply chain issues, so you will still want to be proactive about your inventory. For the best results, the vendor will need an accurate forecast of your usage, and you will want clear communication about lead times and orders.
Bonus Inventory Metric: Maintenance Material Costs
Maintenance Material Cost Percentage = (maintenance material cost over a set period / total maintenance cost over a set period) X 100
If you’re investing time and money to collect data and pull reports on these metrics, then you’ll want to look at your maintenance material costs too. This metric includes more than maintenance inventory. It includes all non-stock materials, spare parts inventory, supplies, and consumables necessary for maintenance. This is a useful metric to help you determine areas for improvement. For example, when you compare your maintenance material costs to your labor costs, you can gain insight into your preventive maintenance plan and maintenance schedule. A higher percentage of material costs could mean that there is an issue with your preventive maintenance plan. Alternatively, a high percentage of labor costs could mean that your maintenance technicians are not scheduled efficiently.
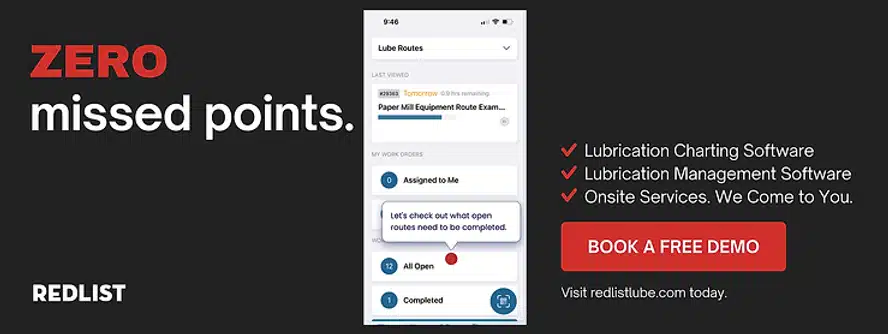
Track Your Maintenance Inventory Metrics with Redlist
The global supply chain issues create an opportunity and motivation to improve your spare parts management. All of these metrics can support you in optimizing your maintenance inventory. However, you need a system to effectively measure and track these metrics. Redlist’s Enterprise Asset Management (EAM) software digitizes the data collection and auto-populates reports on the metrics you need. Having software to streamline this process enables you to become proactive about your maintenance inventory management, regardless of what is happening with the supply chain.