Machinery vibration is a common and unavoidable occurrence in industrial equipment. And, there are many components and operating factors that contribute to this occurrence. Careful analysis of vibration characteristics and measurements helps develop a clear understanding of these components and factors, and ultimately an understanding of how vibration affects machinery.
By understanding machinery vibration, you can prevent significant damage to assets. Hence, you can prevent equipment failures, downtime, and repairs, all while improving safety in your facility. In this blog post, we will explore what machinery vibration is and the common techniques used to measure and analyze it.
What is Machinery Vibration?
Machinery vibration happens when a motorized machine moves or shakes due to moving or rotating parts. Standard manufacturing and assembly tolerances for a machine result in clearances and imbalances within its parts, causing normal machinery vibration.
As you use the machine, it experiences normal machine wear, which causes a natural rise in machinery vibration over time. Drastic and major spikes in machinery vibration, however, can indicate that a machine or its components are being subjected to increasing stresses, loss of stiffness, and premature wear.
Vibration analysis makes it easy to identify whether machinery vibration is nearing or has reached dangerous levels. But, pinpointing the causes of high machinery vibration is a much more complicated task. This task requires careful analysis of the frequency and amplitude of the vibrations. Analysis allows engineers and technicians to determine the source of the vibration, its severity, and ways to mitigate it.
Frequency of Machinery Vibration
The vibration frequency is the fundamental parameter in machinery vibration analysis. Machinery vibration frequency indicates the number of times the machine oscillates or vibrates per unit of time. The common unit of frequency is cycles per second (CPS), but other units like Hertz (Hz) and cycles per minute (CPM) are also used.
Every machine part vibrates at a unique frequency or frequency range. Therefore, determining the frequency of machinery vibration can be valuable in narrowing down the potential vibration sources.
Amplitude of Machinery Vibration
The amplitude of vibration indicates its magnitude or intensity. The higher the amplitude, the more severe or violent the vibratory movements. Thus, high amplitude vibrations cause more stress and damage to machine components and structure.
Depending on oscillation characteristics, the amplitude of vibration can be measured in three ways resulting in three types of amplitudes:
- Velocity
- Displacement
- Acceleration
These different types of amplitude can give you varying insights into the vibration of your machines.
Velocity Amplitude
Velocity amplitude indicates the speed of machinery vibration. It considers both vibration frequency and displacement, or the distance traveled by vibrating parts as they oscillate. Velocity amplitude can be expressed as either the peak value or, more frequently, the root means square (RMS) value, which measures the vibration energy.
Velocity amplitude is the industry standard for evaluating machine conditions based on vibrations. ISO (International Organization for Standardization) standards even refer to velocity amplitude when identifying the vibration severity.
Displacement Amplitude
Displacement amplitude measures the displacement or the distance traveled by vibrating parts as they oscillate. Vibrations with high displacement amplitude can cause machine components to exceed their yield point and experience a catastrophic failure. Measuring the displacement amplitude provides valuable vibration insight when vibration frequencies are low.
Acceleration Amplitude
Acceleration amplitude denotes the force exerted by the vibration. Measuring acceleration is helpful when determining the possibility of fracture in machines that rotate at high speeds. Lubrication breakdown can also happen due to high acceleration in high-speed operations, resulting in excessive wear, intense heat, and premature failure.
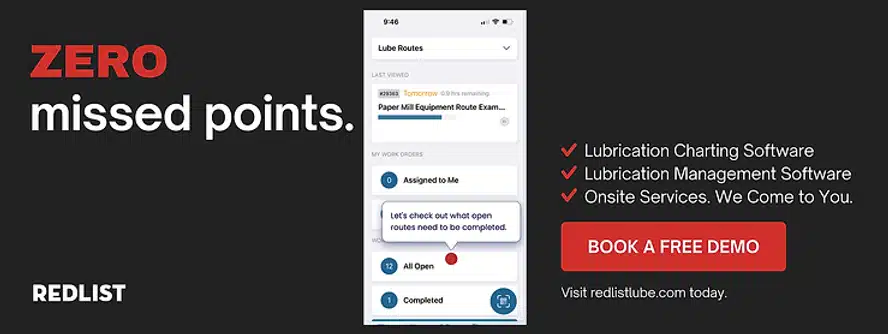
Implementing Machinery Vibration Analysis
Vibration analysis is one of the methods used to monitor the conditions of machines, equipment, and other assets. With a clear understanding of machinery vibration, vibration analysis can help detect signs of machine failure and their severity. But the success of vibration analysis depends on establishing acceptable vibration limits for machines.
Redlist’s Lubrication Management software can be a valuable tool in establishing acceptable vibration limits for vibration analysis. The software makes it easy to record, analyze, and store vibration measurement results and relevant information. Schedule a free demo to learn more about the benefits Redlist can provide to your maintenance and reliability program.