When it comes to heavy equipment, machinery lubrication is crucial to keeping it in work-ready shape. It is also vital for protecting your investment and ensuring you get the full service life from your equipment. Before starting your work for the day, you likely already do a daily inspection. However, you need to make sure that checking your machinery lubrication is part of that inspection to keep your equipment adequately lubricated and greased.
Why is Machinery Lubrication Important?
You need machinery lubrication in order to avoid metal-on-metal contact between components. The majority of the joints, linkages, and moving elements that make it possible for your excavator, loader, dozer, or any other machine to function rely on lubrication. Just like the engine in your machine needs oil, moving parts need grease to perform smoothly and prevent heat, friction, and unnecessary wear.
Failure to keep moving components adequately lubricated will cause them to dry out, resulting in rapid component failure. Your machines are at an increased risk if they function in high-cycle, heavy-load operations. The manufacturer’s recommended greasing intervals are the best approach to ensure that your heavy equipment performs well and has a long service life. Additionally, machinery lubrication aids in preventing costly, unproductive downtime.
Machinery Lubrication Best Practices
Identify Lubrication Points
The first step of machinery lubrication is taking note of all your lubrication points and the grease or oil that they require. Most grease locations on most machines are visible from the outside. However, some might not be visible. To ensure that you are aware of all the points and that you hit them all in your daily grease rounds, it is important to consult your equipment owner’s manual. If it doesn’t have a graphic showing the lubrication spots, check the equipment itself for a drawing often on the inside of the door. Lastly, you can look online.
Keep it Clean
Before manually lubricating pinpoints and bearings, it is important to clean all your grease fittings and your grease points. If you don’t, the dirt or debris on the fittings or your machinery will be pushed into the joint when you pump the grease in. The mixture of dirt and grease will then rub on the metal components, causing excess and premature wear. Using clean grease and oil (and keeping it clean) for machinery lubrication is vital to prevent these detrimental effects.
A second step in keeping your lubrication clean is to remove all of the old grease before using new grease. This is especially important because some grease is not compatible with others. Additionally, your grease may contain wear particles or debris that you should remove from your equipment.
Make Machinery Lubrication a Routine
We already mentioned adding machinery lubrication to your daily inspection, which is crucial. Furthermore, you can develop a machinery lubrication routine. It’s a good idea to grease your lubrication points in the same order every day, so you establish a routine and don’t ever miss any. Additionally, your inspection should include checking for any missing or damaged grease nipples.
Carefully Select Your Lubricants
Always use the lubricant that the manufacturer has recommended for your particular equipment. While it may be tempting to use the same lubricant on all of your equipment, doing so will be detrimental to both you and your company. Instead, choose a grease that is appropriate for each machine and the environment it operates in. In addition, based on their intended use and operating temperatures, various components of your equipment may need a different kind of grease. The recommended grease will always be listed in the operating instructions for your equipment. Different kinds of lubricants may be suggested for summer, winter, or wet weather depending on your climate.
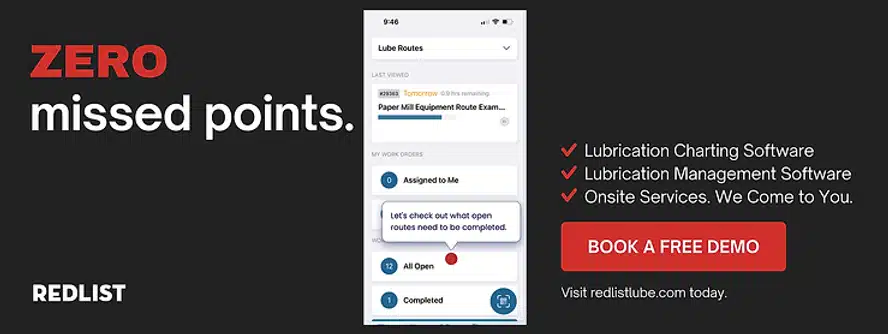
Machinery Lubrication Pays Off
In conclusion, your equipment is not cheap, and machinery lubrication is a vital part of maintaining and protecting your investment. By following the best practices outlined in this blog, you can ensure that your equipment is properly lubricated, clean, and ready for operation. By identifying lubrication points, keeping your lubrication clean, making machinery lubrication a routine, and carefully selecting the right lubricant for your equipment, you can help prevent costly downtime and prolong the service life of your equipment. Remember, investing in the right lubrication and following the manufacturer’s recommended intervals can pay off in the long run.