Lubrication safety is a crucial component of workplace maintenance procedures that you must not overlook. Not only does proper lubrication ensure optimal performance from equipment, but it also has its own unique safety risks. As a maintenance manager or business owner, you must be aware of the dangers associated with lubricant handling and how to properly prepare for these hazards. At the same time, those who work in direct contact with oils and greases need to understand which guidelines apply so that they can safely handle their supplies without adversely affecting workplace operations.
Why are Lubrication Safety Guidelines so Important?
When determining how to successfully perform a task, the primary concern for any company should be ensuring their employees’ safety. No matter how important a maintenance or repair job may be, you must always complete it safely. The benefits that lubrication has on safety are real, despite the fact that people tend to forget about them.
A plan must be in place to ensure that all workers handling lubricant products understand and can recognize potential hazards. Lubrication is often thought of as a routine and simple task, but the safety hazards are no less important than other tasks. Additionally, lubrication tasks, such as topping off fluid levels and greasing moving machinery, involve moving equipment, hot engines, and sometimes tight spaces. This requires lubrication experts to exercise extreme caution to avoid getting themselves or their tools caught in machinery or burnt. You carry the risk of suffering serious injuries if you come into contact with a shaft that is turning quickly or if you get a finger caught between two surfaces that are meshing.
Lubrication safety guidelines covering proper storage, worker training, personal protective equipment (PPE), emergency response plans, disposal procedures, and more can equip you and your team with the knowledge needed to create a safe lubrication program at your facility.
5 Hazards to Address with Your Lubrication Safety Guidelines
Lockout-Tagout Procedures
Because lubrication involves tight spaces or rotating equipment, the majority of this equipment comes with safeguards to guarantee that people remain away from these potentially hazardous areas. If you must remove a guard for lubrication, the standard procedure is to make sure the equipment is locked out and switched off to prevent anyone from accidentally turning it on. This is called a lockout-tagout procedure.
Leaks and Spills
Facilities with equipment and lubricants have a high likelihood of oil leaks or spills. If you come across even a small oil leak, it must be cleaned up and fixed as soon as possible. Leaks, no matter how small, can easily contribute to slips, trips, and falls. Additionally, if you don’t repair the leak, it can get out of hand and become expensive in terms of make-up fluid and contaminant intrusion. So, make spill containment easy and accessible for your team by placing spill-containment tools and supplies in strategic locations throughout your facility. Also, all employees should receive training on how to utilize these tools and the organization’s lubricant waste disposal policy.
Sampling a High-Pressure Fluid
Dedicated sample valves are used to extract oil samples. The valve serves as a safety measure to lessen the dangers involved with taking a sample from a pressurized system. This is especially vital for machinery with high fluid pressure, such as hydraulics. Your sample valve in those systems should be a pressure-reducing sample valve. This will reduce the oil stream’s pressure, making it safer and simpler to collect in a sample bottle.
Grease Gun Maintenance
Grease at high pressures poses additional dangers. A manual grease gun, something that your lubrication technicians likely use almost daily, can generate up to 15,000 pounds per square inch of pressure. With proper operation and maintenance of your grease guns, this is relatively safe. However, if your grease gun has a buildup of dried grease on the lines and fittings, then that pressure can’t exit appropriately and will find or create another opening. Oftentimes, the grease will shoot out at the connection between the grease gun coupler and the fitting. This is a prime lubrication hazard, as it can cause grease to push through the skin or create an injection wound. To avoid this hazard, you should not hold the grease gun coupler in your hand when greasing.
Skin Contact with Lubricants
The final lubrication safety guidelines tip is to minimize and address skin contact with lubricants. While it doesn’t pose a significant risk, some synthetics and additives do have some potential health risks. Considering that lubrication is very much a hands-on job, it is best to practice caution. You can minimize skin contact by using gloves or barrier creams. Or, you can quickly and regularly address skin contact by washing often with soap and water. The majority of lubricant safety is simple, but you should always consult the lubricant’s safety data sheet to find out how to handle it.
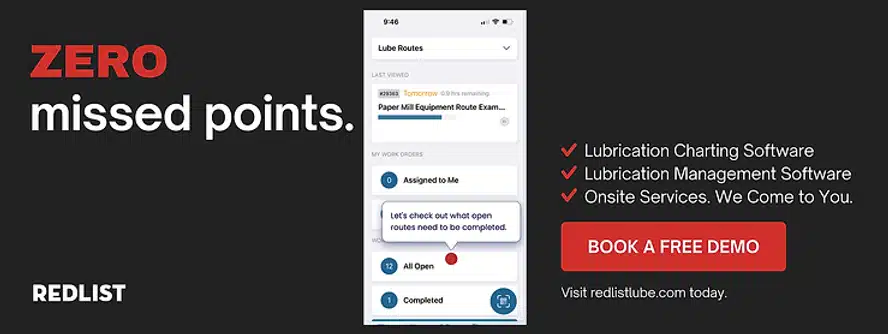
Take Steps to Improve Your Lubrication Safety Guidelines Today
Lubrication safety guidelines are important for a variety of reasons. By taking the time to develop and implement proper procedures, you can avoid many hazards associated with lubricants. By taking steps to improve your lubrication safety guidelines today, you can create a safer work environment for everyone in your facility.