The lifespan and performance of lubricants for machine maintenance depend on proper storage and handling. Although steel oil drums and oil-suitable barrels are effective in protecting lubricants from contamination, the conditions during storage and handling are essential for maintaining their effectiveness.
Improper storage and poor handling of oil drums can cause the contamination of your lubricants and degradation of oil additives. This further results in a decline in the performance of your lubricating oil, ultimately affecting the life of your machinery and equipment.
Best Practices for Storing and Handling Oil Drums
1. Protect from Potential Contamination
The major contaminants in oil drums are dust and humidity. Dust can come in the form of small debris from production, metalworking, or welding. Humidity can come from process steam, washdown areas, or the climate of the storage space.
You can protect oil drums from contaminants by storing them in a sealed and controlled storage room away from constant personnel and equipment traffic. Ideally, this room has some form of climate control to regulate the humidity. Additionally, using clean pallets when storing and transporting oil drums prevents them from coming in contact with the factory floor, which contains dust contaminants.
2. Control Temperature
Temperature variations can have major effects on the integrity of oil drums during storage. Heat causes the drums to expand, while cool temperatures cause their contraction. This “breathing” effect of temperature differences on oil drums can weaken their seal against dust and humidity.
Proper ventilation and air conditioning can lessen temperature variations, but these measures can be costly. Regularly checking and ensuring the tightness of drum bungs can also be a great way to prevent the negative effects of temperature variations. Another is the use of desiccant breathers or particle breathers to keep out moisture and dirt.
3. Keep Away from Direct Sunlight
The prolonged exposure of oil drums to direct sunlight also promotes “breathing” and increases the risk of contamination. In addition, the ultraviolet (UV) rays in sunlight can cause the degradation of additives in the lubricant, lessening their effectivity.
Minimize the exposure of oil drums to direct sunlight by keeping them in dark areas of your facility. You can also invest in drum covers with anti-UV properties.
4. Use Drum Covers and Store Oil Drums in a Horizontal Position
You can practice these storage methods in cases when there is no available secure and isolated room to keep your oil drums. Drum covers are effective barriers against dirt and humidity. Keeping oil drums in a horizontal position during storage allows the oil to cover the drum bungs, preventing contaminants from entering the drum.
5. Clean Drums Regularly
Cleaning the oil drums regularly further prevents the accumulation of contaminants. Regular cleaning also allows you to inspect any missing labels, leaks, and other irregularities.
6. Practice First In First Out (FIFO)
FIFO means using the oldest stock first before the new one. This method ensures good stock rotation and prevents instances when old stock is stored too long and has a high risk of contamination. This also prevents oil stratification or the separation of different oil components, resulting in decreased effectivity as a machine lubricant.
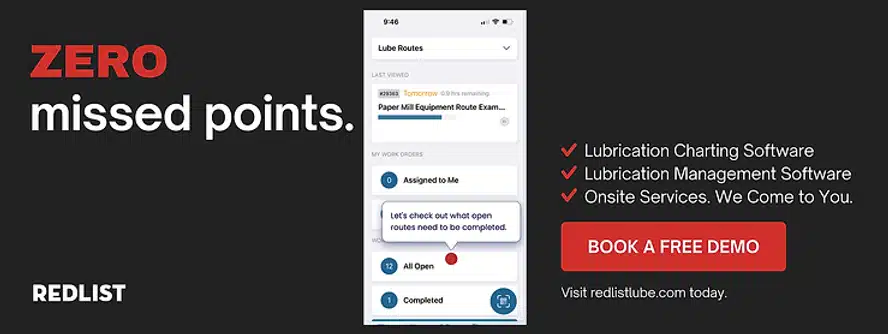
Redlist Lubrication Management
A Lubrication management software like Redlist can help you execute your lubrication program and keep track of your process. And this program includes monitoring the storage and handling of your lubricants and other supplies. With Redlist, you can schedule the regular checking of your oil drums to ensure that they are clean, intact, and not exposed to direct sunlight, heat, and other factors illustrated above. Redlist can also be valuable in stock control, ensuring that you practice FIFO in the utilization of your lubricants and other supplies. Optimizing your storage and handling of oil drums will only improve the rest of your lubrication management program.