Lubrication management is an important part of any organization’s maintenance strategy. By implementing proper lubrication practices, you can improve performance, safety, and equipment reliability, reduce operating costs, and extend the life of your assets. In this blog post, we will discuss the benefits of lubrication management and provide tips for improving your organization’s lubrication management program.
Where to Begin with Lubrication Management?
An effective lubrication program requires a holistic and systemic approach to reduce operating costs and improve reliability. There are many factors to consider, and it can be overwhelming to decide where to start. An excellent starting point, no matter the industry, is to review and plan for every step of a lubricant’s life cycle. This includes lubricant:
- Selection
- Reception and Storage
- Handling and Application
- Contamination Control
- Analysis
- Disposal
What are the Lubrication Management Best Practices to Follow?
Lubricant Management Software
Your lubrication management program can work far more efficiently through the use of lubrication management software. You can access everything you need from any mobile device, including offline capability for technicians in the field. Furthermore, you can create standardized processes and ensure technicians follow them by providing photos, videos, checklists, and written instructions for each lubrication task. Additionally, your assets will have more consistent lubrication procedures with the software supporting lubricant specifications and relubrication schedules.
The benefits are seemingly endless, as it is even easier to manage inventory with real-time updates. Also, complete integration with current business platforms, as well as condition monitoring sensors and oil analysis labs, puts all of your lubrication data at your fingertips. Implementing lubrication management software can streamline all of the best practices below and better support your continuous improvement.
Lubricant Selection
Choosing the right lubricant is one of the first questions to answer when putting a new machine into operation. In most cases, you can find lubricant recommendations in the operating manual and by consulting the technical service representative of the equipment manufacturer. However, that often leads to companies having multiple different brands of the same lubricant application. So, a better solution is to consult with your lubricant supplier in this process. You likely already have a lubricant on hand that serves this application.
There are several factors to consider when it comes to lubricant selection. These include the specification and performance requirements, the possibility of lubricant consolidation, the amount of stock needed for handling and application, lubricant identification across the plant, purchasing procedures, and delivery. Furthermore, you should also determine any lubrication-related hardware at this time.
Lube Room Storage
A crucial yet often overlooked detail of lubrication management is proper storage. How you store lubricants is one of the determining factors for their life cycle and condition. Additionally, storage and organization directly impact identification and use. If you clearly organize and color-code your lube room, then your technicians are far less likely to accidentally cross-contaminate lubricants.
Another key element of storage is inspecting your lubricant when you receive it. This will ensure that it meets quality standards, comes in the correct quantity, and arrives on time as promised. Filtering new lubricants and even testing to establish baselines are key at this stage.
Lubrication Handling and Application
When the lubricant is prepared for application, care must be taken to ensure integrity, safety, and environmental protection. Filtering the new lubricant before use is an excellent proactive practice. Obtaining the cleanliness targets established for each product may require filtration for particle contaminants and dehydration systems for water contamination.
Lubricant application is any lubrication management task, such as oil changes, top-ups, filtering, regreasing, oil condition inspections, and machine condition inspections. Training your technicians on application and handling best practices goes a long way in supporting the success of your lubrication management. However, it is helpful to have supporting resources including detailed documentation of the machine’s status, safety procedures, and tasks to be completed.
Contamination Control
One of the most important parts of a proactive lubrication management program is contamination control. All practices relating to lubricant cleanliness are considered contamination control. To consistently maintain clean lubricants, there are four important steps to follow:
- Identify a specific level of cleanliness for each machine based on its criticality and sensitivity to contaminants.
- Revise operation and maintenance practices to restrict the introduction of contaminants.
- Implement filtration for the removal and ongoing control of contaminants.
- Regularly monitor contamination levels to ensure that your lubricants are staying within the target level for your assets.
Lubricant Analysis
Monitoring the health of your lubricants and your assets is made easy with the help of oil analysis. Its objectives include confirming the lubricant’s quality and type, measuring its health and condition, estimating its remaining useful life, locating the causes of failures, identifying and measuring contaminants and abnormal wear, and supporting the optimization of lubrication intervals and other maintenance procedures.
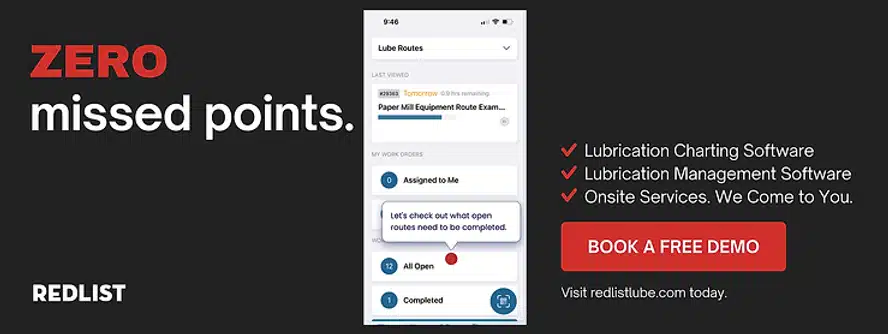
Choosing the Right Lubrication Services
There are many factors involved in the setup, ongoing maintenance, and continuous improvement of your lubrication management program. Many businesses look to lubrication services to provide support in different areas to keep their program working efficiently. Depending on your needs, you may hire a full-time reliability or lubrication engineer. Alternatively, you can talk to your lubricant supplier about any additional lubrication services they provide. However, if you just need help getting started, charting lube routes, and setting up your comprehensive lubrication management program, our certified lubrication team is here for you. They can come to your facility and create a turnkey lubrication program in a matter of weeks. Schedule a demo to learn more about how we can support you in your lubrication management goals.