Many organizations consider lubrication management to be a reactive maintenance strategy. But when managed proactively, lubrication can actually be a key component of an effective proactive maintenance program. By planning and scheduling lubrication tasks according to wear patterns and machine conditions, you can maximize equipment uptime and availability while minimizing the need for expensive repairs. In this blog post, we’ll take a closer look at proactive maintenance and the role lubrication management can play to help your organization achieve its maintenance goals.
What is Proactive Maintenance?
Proactive maintenance is a strategy that focuses on taking measures to protect equipment and systems before problems occur. Alternatively, run-to-failure maintenance means waiting until equipment breaks down to perform maintenance. So, instead of the run-to-failure saying “if it ain’t broke don’t fix it”, you can think of proactive maintenance as “if it might break, let’s prevent it!”
The goal of this maintenance strategy is to extend the lifespan of assets and minimize downtime. Common proactive maintenance activities include routine inspections, cleaning, lubrication, and replacement of worn parts. By taking these steps, businesses can avoid costly repairs and unexpected interruptions in operations. While this can require a significant upfront investment, it is often more cost-effective in the long run than waiting to address problems as they arise. In addition, it can improve safety by reducing the risk of accidents and injuries. For these reasons, proactive maintenance is a key part of any effective asset management program.
Types of Proactive Maintenance
Preventive maintenance (PM) is the most common type of proactive maintenance. In fact, many people use these terms interchangeably. Preventive maintenance is typically done according to a pre-set maintenance schedule, such as changing an asset’s lubricant after a specific number of operating hours. Proactive maintenance carries a larger focus on identifying and resolving the root cause of potential failures.
Condition-based maintenance (CBM) is a type of proactive maintenance that is driven by condition monitoring data. This may include lubricant analysis with a lab or in-line sensors, vibration analysis, or thermography to name a few. Condition monitoring is essential to continuous improvement because it can alert you of potential problems before they cause major issues or downtime.
Scheduled and routine maintenance is the final type of proactive maintenance. This may include routine inspections or cleaning, as well as other recurring maintenance tasks.
Proactive maintenance can take many forms, and sometimes the solution is one you wouldn’t even expect. For example, if your lubricant analysis comes back showing high levels of contaminants, the next step would be to determine the cause. In this example, let’s say you find that you recently hired a new lube tech and the machinery with contamination was on his lube route. The proactive solution here is likely to train that employee on your standard operating procedures and best practices to prevent future contamination of lubricants.
Benefits of Proactive Lubrication Management
For starters, improper lubrication causes:
- 43% of mechanical failures
- 70% of equipment failures
- 50% of roller bearing damage
So, a major benefit of proactive lubrication management is resolving the cause of these failures before equipment breakdown even happens. This requires you to shift your perspective of lubrication management from a reactive maintenance task to a proactive one. Then, you can start detecting and eliminating failures before they develop. While there is an investment of time and money to implement proactive maintenance, it allows you to reduce your maintenance and equipment costs long term. Also, the reduction of unplanned equipment downtime is a huge savings in and of itself. As asset health, reliability, and availability increase, so does asset lifespan. This offers further savings as you won’t have to replace equipment as often. Finally, proactive maintenance can actually reduce the risk of safety incidents. Proactive lubrication management prevents equipment from overheating or reaching catastrophic failure, which prevents any potential safety issues that would cause.
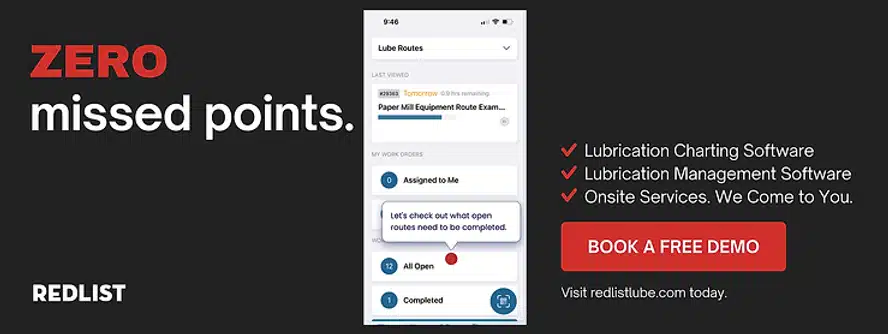
Striking the Maintenance Balance
World-class maintenance programs typically recommend a balance of 10% reactive and 90% proactive maintenance. This proactive number is broken down further to between 25-35% preventive maintenance and between 45-55% predictive maintenance. By performing these types of maintenance on a regular basis, it is possible to detect and fix potential issues before they cause major damage or require extensive repairs. With the right planning, you can ensure that your proactive maintenance strategy strikes the balance between being cost-effective and beneficial to your maintenance goals.