Any effective maintenance strategy should include lubrication contamination control in its objectives. And contamination control starts with the identification of different contaminants and their sources.
Lubricant contaminants can be solid particles from various sources, water, heat, air, and even cross-contamination from other lubricants. It is, therefore, essential to keep lubricants clean, cool, dry, and isolated from other lubricants.
The identification of lubrication contamination sources also comes with assessing their degree of influence or the ways they can damage the machinery and oil components. From this step, it will be easy to formulate the measures to maintain the excellent condition of the lubricants.
Factors Affecting Lubrication Contamination
There is a wide variety of contaminants commonly found in oils and lubricants. And each has varying effects on the durability and reliability of lubricants and machines. For the effective identification of contamination sources, it helps to understand the factors affecting contamination.
The types of contaminants present in a lubricant depend on environmental conditions, the specific materials used in the production process, and the chemicals that already exist or are formed inside the lubricating system. Maintenance activities and how the machines are operated can also affect contamination.
Common Contaminants in Oil and Their Impact
For effective lubrication contamination control, you should identify all the potential contaminants in your lubrication systems or machine. Below is a list of the common contaminants in oil and how they affect the oil’s lubricating properties and the machines.
Solids
Solid contaminants include dirt, metal particles, soft insolubles, soot, etc. When these are dissolved in the oil, they promote oxidation. This is the process where the oil reacts with oxygen resulting in degradation and decreased performance. Solid contaminants in oil further reduce its quality by depleting the additives and affecting its viscosity. Using contaminated oil causes the solid contaminants to adhere to machine surfaces leading to mechanical destruction through abrasion and surface fatigue.
Water
Similar to contamination by solid particles, water in oil also causes oxidation and additive depletion resulting in decreased performance. Additionally, water can emulsify with the oil and increase its viscosity and decrease its lubricating abilities. Water-contaminated oil promotes rusting and acidity destruction of machine surfaces. Furthermore, water can damage machine surfaces by promoting cavitation and loss of film strength.
Fuel
Fuel contaminants can be diesel, gasoline, or natural gas. This type of contaminant also causes additive depletion in oils in addition to causing the production of aromatics and sulfur. These effects further degrade lubricating performance by increasing vapor pressure and lowering flash point and viscosity. Fuel-contaminated lubricants cause the production of sulfuric acid on the machine surfaces, which promotes corrosion and loss of film strength.
Glycol or Antifreeze
Glycol contamination also promotes oxidation and produces sludge by increasing the viscosity of the oil. When used as a lubricant, the oil contaminated with glycol attacks machine surfaces with acidity and deposits. Machine surfaces also experience lubricant film strength loss and abrasion.
Air
Air contamination promotes oxidation and micro-dieseling or the pressure-induced thermal degradation of the oil. Also, air dissolved in the lubricant leads to foam formation and viscosity increase. Lubricants contaminated with air attack machine surfaces by promoting rusting and corrosion, and varnish formation from micro-dieseling. Air in oils also causes cavitation on machine surfaces.
Heat
Heat causes thermal degradation, oxidation, and volatility in oils. Furthermore, heat can cause viscosity to increase or decrease through cracking or the separation of oil molecules due to high heat. Lubricants heated to high temperatures cause damage to machines by promoting varnish formation, increased acidity, and film strength loss.
How Lubrication Contamination Happens
It’s not enough to identify the potential contaminants. You should also understand all the possible ways contamination can happen in your facility. Below are the common ways contaminants can enter and degrade lubricants and machines.
Built-in
This means the contaminants were already present before the lubricant was applied or used. Oil contamination can happen through servicing or manufacturing processes. A solid contaminant, for example, can come from the new oil added or the new filter installed. It can also come from the contaminated components used or from manufacturing debris left behind in a brand-new machine.
Ingested
Contamination can also be a result of using the machine or equipment. Processes such as the use of compressed air or gas, catalysts, and chemicals can result in lubrication contamination. Contaminants in the atmosphere, such as dust and slag particles, provide another way contamination happens. Combustion can also produce contaminants such as soot.
Generated
Machine surfaces and oil can also generate contaminants when in use. Machine surfaces undergo mechanical and corrosive wear over time which produces solid contaminants. Lubricants also generate solid contaminants as they oxidize and undergo additive degradation.
Lubrication Contamination Control
The next steps after identifying contamination sources are planning and executing contamination control. These are critical steps because contamination control is specific to the machine or equipment and the process involved. Even within similar machines in the same facility, the methods used to control contamination may differ.
In addition, it is essential to consider the relative significance of the contaminants and their sources. Ensure that your controls are cost-effective by prioritizing the most significant sources of contamination and addressing them in accordance with their importance.
Effective, efficient, and sustainable contamination control requires good judgment and knowledge of the machines, their components, their operation, and the environment. It is also recommended to conduct an in-depth investigation to identify the precise components, locations, and times at which contaminants enter the machine.
Contamination control in lubricants and lubricating systems requires continuous corrective action, relevant training, improving procedures, and close monitoring of the machines through oil analysis and machine inspections.
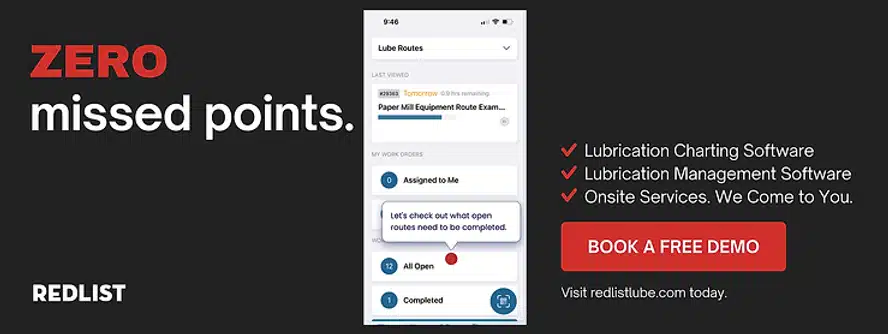
Contamination Control with Redlist
With our Lubrication Management software, managing contamination is as simple as working your phone or computer. Redlist’s sophisticated and high-quality lubrication management software lets you easily track the contaminants and their sources specific to your machine and processes. This provides you and your team with a user-friendly way to monitor your lubricating system, execute contamination control steps, and perform corrective actions. Contact us for a demo to learn more.