For any business that relies on lubricants, reception and storage are core processes that you must monitor closely to maintain productivity. Keeping tight control of the incoming stock, usage rate, and environmental conditions of your lube room can help you get more from finite resources by recognizing when parts need replacement or preventive maintenance is due. But keeping track of all these important factors can be tricky. So, how do you make sure your system runs optimally? This blog post provides an overview of the most effective ways to keep track of your lubricant reception and storage process.
Lube Room Optimization Starts with KPIs
To have a world-class lube room, you have to measure and monitor the effectiveness of your processes. That’s where KPIs (key performance indicators) come in. They help you evaluate a program’s performance and can indicate if a program is moving in the right direction. There are several noteworthy KPIs to measure for lubricant reception and storage, regardless of whether you are just starting your lube program or you are working toward a fully operational lubrication program.
Why You Should Track Lubricant Reception and Storage
Receiving and storing lubricants is a crucial component of the lubricant life cycle. Your entire lubrication program may suffer if some duties are not carried out well or at all. For instance, it may be necessary to change suppliers if you consistently receive lubricants that don’t meet plant cleanliness standards. If your lubricant reception process doesn’t follow best practices, these lubricants could elude detection and wind up in a crucial machine.
The KPIs You Need for a World-Class Lube Room
Optimizing your lube room goes far beyond simply improving the organization and cleanliness. Those details are important too, but here are a few KPIs that will help you track the other stuff.
Lubricant Reception
To determine the total efficiency of the lubricant receiving process, you must measure a few factors. A handful of these parameters are related to the lubricant’s cleanliness and dryness.
As you already know, one of the best ways to improve asset reliability is to ensure that you use clean lubricants. You can use the reporting standard for fluid cleanliness, ISO 4406, to measure cleanliness with a particle counter. This standard will help you set cleanliness goals that will serve as a reference point for how clean different lubricants should be for specific purposes.
Second, you need to set dryness goals. The KPI for the maximum amount of water is reported in parts per million (PPM). For example, you may determine that all gearbox oils must have less than 300 PPM of water.
Finally, once your goals are set, your lubricant reception KPI requires tracking the number of lubricant deliveries that satisfy the targets and the number that do not. All is well if the lubricants consistently meet your goals. However, a conversation with the provider might be necessary if the lubricants consistently or excessively exceed the cleanliness and dryness goals. Sampling incoming lubricants for impurities is a crucial step in this process that is frequently skipped or neglected. A primary factor in the early failure of equipment and lubricants is the use of severely contaminated lubricants. This can be tracked and prevented by creating a metric for it.
Lube Room Inventory Rotation
Not only is it essential for facilities to be mindful of lubricant shelf life, but you must also ensure you rotate your inventory appropriately with the first in first out method. Like many other things, lubricants don’t last forever. Yet, you can walk into almost any lube room and find at least one expired lubricant still on the shelf. The manufacturer’s information is a great starting point when determining a lubricant’s shelf life. However, keep in mind that the manufacturer sets this date based on proper clean, dry, and climate-controlled lubricant storage. If your lube room doesn’t follow storage best practices, your lubricants could actually have a shorter shelf life.
Lube Room Inventory Management
The second issue with lube room management is making sure your purchasing frequency matches your usage. If you purchase more than you can use, you may end up with a lot of expired lubricants. You must strike the perfect balance of keeping enough lubricant in stock to have what you need when you need it, but not too much. To track this, measure how much oil is stored and how much goes into machines each month. If you have 1,200 gallons in storage but only use 200 gallons per month, the maximum amount may need to be lowered. When choosing how much oil to store, consider how long it takes the provider to deliver and the timing of oil changes for high-volume machines.
The final lube room inventory KPI is rarely used lubricants. When you switch to a new lubricant brand, you typically shelve the old one. Lubricant consolidation helps optimize your lube room inventory. Fewer lubricants to manage means technicians can get in and out of the lube room faster. However, you will need to gather inventory data before consolidating lubricants, as well as on an ongoing basis. Periodic lube room audits will help you notice stock rotation inconsistencies and identify areas for improvement.
Safety Incidents
Safety KPIs are vital, given the importance of workplace safety. Tracking accidents and near-misses can help identify safety deficiencies. Back injuries and forklift collisions are common when transferring lubricants around a facility. There are also several dangers while greasing or collecting samples from running equipment with many moving parts. Additionally, lubrication equipment can cause high-pressure injection injuries. The key to safety KPIs is to have all staff lubricant safety training documents easily accessible. Second, put your safety records in a system that enables you to pull reports and analyze trends. If your safety records can separate lubrication-related issues, it gives more insight than a general safety score or report.
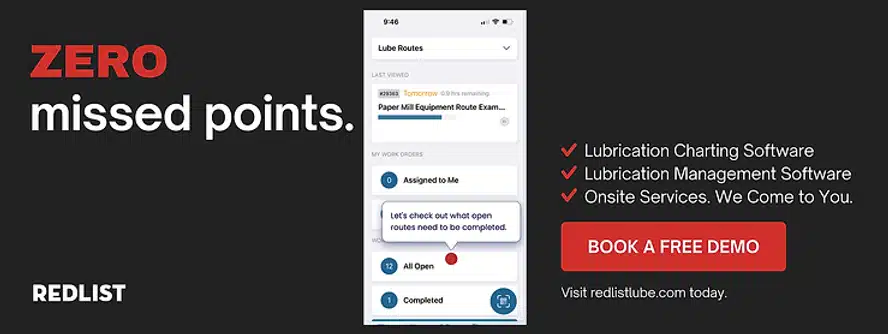
Your Lube Room is Key to Lubrication Management
How does your lubrication program fare in terms of receiving and storing lubricants? Are you monitoring KPIs to determine whether your program is advancing or regressing? The secret to both is gathering accurate data and organizing it in a way that makes it simple to follow from month to month. The secret to success, if you’re aiming for a better lubrication management program, lies in the figures.