As any seasoned maintenance manager or business owner knows, organization and maintenance are key components for success in any workspace. The 5-S system is a valuable tool for optimizing lubricant storage and creating an efficient and well-organized workspace. In this blog post, we’ll discuss why utilizing the 5-S system for lubricant storage is an effective choice for maintaining reliable operations and how to do it.
Why Do You Need to Optimize Lubricant Storage?
The lube room serves as more than just a location for storing and dispensing lubricants. It is where you can develop and maintain a culture of precise, and efficient lubricant handling standards. Additionally, your lubricant storage practices can boost uptime and revenue by providing your equipment with clean, dry lubricants. With the right storage systems in place, including clear labeling, your technicians can easily see what you have and what you need.
What is the 5-S System?
Implementing 5-S into your lubricant storage and handling is one approach to accomplish this. The 5-S system is a set of guidelines of Japanese origins that aims to reduce waste and promote efficiency in the workplace. It consists of five steps:
- Sort
- Straighten
- Shine
- Standardize
- Sustain
The principles of 5-S produce an effective visual aspect when everything is tidy and ordered, making issues and dangers easier to spot. For instance, keeping the lube room floor clean makes it easier to detect leaks or spills. By placing tools and other materials in the proper locations, organizations can reduce wasted time. This may seem like a small thing, but it adds up. So, using this system for lubricant storage can streamline your lubrication processes while reducing waste. Many organizations in different industries use the 5-S system to improve maintenance procedures, reduce downtime costs and enhance employee safety – all while decreasing overhead expenses.
How to Incorporate 5-S for Your Lubricant Storage
1. Sort
It’s easy to acquire extra stuff and old things over time. So, step one is sorting it all out. Determine anything you no longer need including used filters, greasy rags, used funnels, used oil buckets, out-of-date lubricants, empty lubricant containers, worn-out transfer containers, etc. This is an opportunity to remove any unnecessary, old, dirty, or broken items. If you’re not sure about an item, have a team discussion to confirm if anyone still uses it.
2. Straighten
It’s time to organize the lube room after everything has been removed. Make a spot for everything and label it. Put lubricants in a position that reduces waste and travel while simultaneously giving the best ergonomics. The first in first out (FIFO) system should be supported by clearly labeled, easily accessible, and strategically placed bulk lubricant storage.
Each workspace should be organized so that it is easy to see when something is out of place. With only a fast glance, you should be able to view everything required for a space or cabinet. Be persistent and patient with this process. You and your team may need some time to get used to the new organization.
3. Shine
This phase involves thoroughly cleaning the lube room, which is above and beyond a quick wipe-down. Now that the room contains only the necessary items and everything is in its proper location, you may clean it properly. This includes degreasing, cleaning surfaces and transfer equipment, cleaning the interior and outside of cabinets, and sweeping, vacuuming, and mopping the floor.
If necessary, now is the time to make repairs and improvements as well. For example, fix any damaged areas of the floor, improve the lighting, replace worn-out cabinets and components, and, of course, repair any leaks. With an ultra-clean lube room, you may even reduce lubricant contamination because there is less dust, dirt, and debris in your lubricant storage area.
4. Standardize
Take photos of your clean and tidy lube room to display in each area as the lubricant storage standard. This will serve as a reminder of the level of cleanliness that is possible and expected. Communicate to your team the importance of maintaining the standards in the photos. Also, you can keep track of exactly what is in each cabinet and where it is located by posting a benchmark image on each workstation or cabinet. To lessen the chance of cross-contamination, utilize color codes on labels for machines, transfer equipment, and lubricant storage.
5. Sustain
The final step of the 5-S system is to sustain your lubricant storage organization. This includes doing periodic audits of your lube room. Also, you can design and display a cleaning plan with a simple sign-off sheet to hold employees accountable. The photos from step four provide support in sustaining the lubricant storage standard. These images are also beneficial when performing audits and communicating the results to the team. The audit results and opportunities for improvement should also be displayed in the area. Hold meetings to share images of your progress and celebrate as a team to develop your organization’s culture.
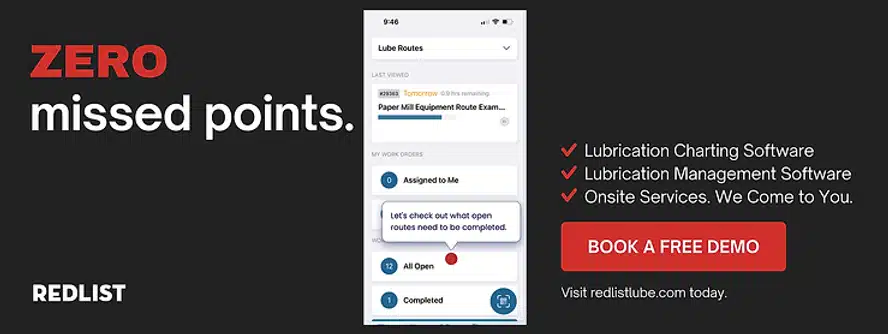
5 Steps to Better Lubricant Storage
To get the most out of your lubricants, it is important to optimize lubricant storage using the 5-S system. This comprehensive approach considers every aspect of storing lubricants, from organization to cleanliness. By sorting, straightening, shining, standardizing, and sustaining your lubricant storage, you can be sure that you are getting the best possible performance from your products. Not only will this save you money in the long run, but it will also help keep your machinery running smoothly and efficiently. Implementing the 5-S system for your lubricant storage is easy and straightforward, and we hope that this article has given you the tools you need to get started.