Condition-based monitoring is a process that can help you better understand the condition of your lubrication system. It is an important tool for determining when and how much maintenance a piece of equipment needs. Condition-based monitoring involves analyzing factors such as vibrations, temperatures, and lubricant conditions to make predictions about the health of machinery. Furthermore, in the field of lubrication, you can use this information to optimize grease and oil schedules and ensure machinery is well-lubricated. This helps to prevent failures and keep your equipment running smoothly and efficiently. In this blog post, we will discuss how condition-based monitoring works and how you can use it to improve your lube operations.
What is Condition-Based Monitoring?
Condition-based monitoring is a type of predictive maintenance that uses sensors to monitor the condition of equipment in real-time. By continuously monitoring for signs of wear and tear, condition-based monitoring can predict when equipment is likely to fail and identify problems early on. This allows for proactive maintenance to be carried out, which can help to reduce downtime and improve safety. In addition, you can use condition-based monitoring to improve equipment performance by detecting issues that would otherwise go undetected. As a result, condition-based monitoring is an increasingly popular way to manage equipment maintenance.
Why Do You Need Condition-Based Monitoring for Lubrication Management?
In today’s fast-paced operating environments running on tight budgets, lubricating equipment on a calendar schedule is no longer acceptable. If you’re maintaining your lubricant properly, you may be changing your lubricant too early. That means you’re spending more than you need on lubricant, labor hours, disposal, and downtime. For the most cost-effective and efficient lubrication strategy, you need to change lubricant only when conditions call for it. Additionally, getting more life out of your lubricants goes a long way for company sustainability.
The End of Time-Based Lubrication?
Time-based maintenance and lubrication is a tried and true method that maintenance departments have been using for decades. When it comes to lubrication, it’s an easy approach to go the time-based route. You simply schedule the lubrication task on a recurring calendar basis, such as weekly, monthly, quarterly, yearly, etc. Alternatively, you may schedule the task after a certain number of hours according to your equipment’s run-time clock.
While time-based maintenance has its merits, several disadvantages have led many companies to reconsider this approach in favor of condition-based maintenance (CBM). One of the biggest drawbacks of time-based maintenance is that it can lead to over-servicing and the waste of valuable resources–both human and material. In addition, time-based maintenance doesn’t take into account the actual condition of the equipment, which can lead to unnecessary repairs and downtime.
Is Condition-Based Monitoring the Answer?
Given these concerns with a time-based approach, it’s not surprising that condition-based monitoring has gained favor in recent years as a more efficient and effective alternative to time-based maintenance. Many organizations are rethinking their approach to lubrication and preventive maintenance as they search for ways to reduce costs and improve efficiency. With a condition-based approach, service events are scheduled based on the actual condition of the equipment – not on an arbitrary timeline. This provides a number of advantages in terms of cost savings, efficiency gains, and improved equipment uptime. For these reasons and more, CBM is quickly becoming the new standard for industrial maintenance programs. It prevents maintenance from happening too early (as with time-based tasks) or too late (as with equipment failure).
Implementing Condition-Based Monitoring for Lubrication
While condition-based monitoring requires a significant investment of time and resources, the benefits can be substantial. For companies looking to improve their lubrication practices, condition-based monitoring is an essential step.
This approach involves monitoring the condition of machinery components and lubricants, and then lubricating based on need. By lubricating only when necessary, condition-based monitoring can help to reduce lubricant waste and save money. The key is to monitor the conditions that commonly cause failures. This can include these most common conditions for lubrication:
- Lubricant Analysis – The most popular condition monitoring option for lubrication is to track lubricant conditions with either in-line sensors or by sending lubricant samples to a lab.
- Vibration Analysis – You can monitor the vibration of any rotating component, and even negligible fluctuations can alert you of underlying issues.
- Thermography – With more friction comes more heat, making temperature monitoring a critical component of condition-based monitoring for lubrication.
- Pressure Monitoring – This is common for tracking lubricant, fluid, or air pressure in hoses, compressors, tanks, or other equipment.
- Ultrasonic Monitoring – Ultrasonic sensors monitor for high-frequency sounds to help detect leaks or holes in equipment and its components.
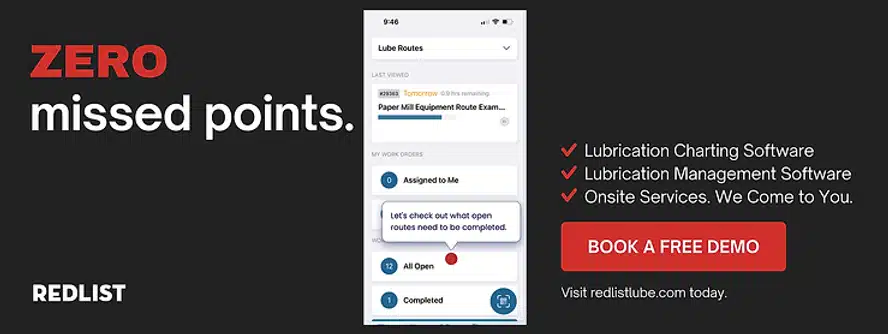
Optimize Your Lubrication Management
Lubrication is a vital part of keeping machinery running smoothly and efficiently. Condition-based lubrication, which involves monitoring the lubricant itself for signs of wear and tear, is an increasingly popular way to extend the life of machinery and prevent unexpected breakdowns. By understanding the parameters used to define lubrication values and using state-of-the-art technology, lubrication engineers can keep machinery running reliably and efficiently while reducing maintenance costs. Condition-based lubrication is an important part of any world-class lubrication program.