Lubrication is crucial for the smooth functioning of machinery. Replacement intervals are a key aspect of that maintenance. However, finding the right lubrication equipment replacement interval is challenging. If you do, you can ensure that your equipment functions efficiently without costly breakdowns or downtime. In this blog post, we will discuss how to optimize lubrication equipment replacement intervals to ensure that your machinery operates at peak performance. We will look at the factors that influence replacement intervals and provide tips and best practices to help you establish the ideal replacement interval for your lubrication equipment. This blog post will provide valuable insights to help you optimize your lubrication equipment replacement intervals.
What Factors Affect Lubrication Equipment Replacement Intervals?
Several factors can impact the replacement intervals for lubrication equipment. The original equipment manufacturer (OEM) typically provides recommendations for when to replace lubrication equipment based on studies conducted during equipment development or lubricant approval. However, these intervals may not always be suitable for specific operating conditions. Factors such as the operating environment, equipment design, lubricant quality, and maintenance practices can all play a role in determining the appropriate replacement interval. Therefore, it is essential to consider these factors and conduct an oil analysis to evaluate the condition of the lubrication equipment. This will help you determine the optimal replacement intervals for your facility.
What are the Benefits of Optimizing Lubrication Equipment Replacement Intervals?
Optimizing lubrication equipment replacement intervals can have numerous benefits. First and foremost, it can extend the lifespan of the equipment, which ultimately saves money on replacements and repairs. By avoiding premature wear and tear caused by improper lubrication, the equipment can continue to perform at its best for longer periods. Additionally, optimizing replacement intervals can lead to improved equipment reliability, reduced downtime, and increased productivity. This can also improve workplace safety by reducing the risk of equipment failures and accidents. Finally, optimizing replacement intervals can help reduce the environmental impact of equipment maintenance by minimizing the amount of waste generated from premature replacements.
Best Practices for Optimizing Lubrication Equipment Replacement Intervals
To optimize lubricant replacement intervals, there are several best practices that you can follow.
Implement an Oil Analysis Program
It is crucial to establish an oil analysis program that includes regular testing and evaluation of the lubricant’s condition. This will help to identify potential problems early on, allowing you to take corrective action before more significant issues occur.
Consider Original Equipment Manufacturer Recommendations
It is essential to understand the original equipment manufacturer’s recommended operating conditions and lubricant specifications that drive their replacement interval. If your equipment operates in a harsher environment than their recommendation is based on, you may need to change your lubricant more frequently. These guidelines will help ensure that your lubrication equipment operates efficiently and prolong its lifespan.
Monitor Operating Conditions
Monitoring operating conditions and the environment is crucial in optimizing lubricant replacement intervals. It is essential to ensure that the equipment is operating within the OEM recommendations. Any deviation from these specifications can affect the lubricant’s performance and reduce its lifespan. Regular monitoring of these conditions can help detect any potential issues and allow for corrective action to be taken before any damage occurs. This can ultimately lead to longer lubricant life and less downtime for equipment maintenance. Monitoring these factors can be done manually or through the use of sensors and automated systems, which can provide real-time data and alerts when conditions deviate from acceptable levels.
Follow Lubrication Best Practices
It is crucial to utilize high-quality oil filters and other maintenance best practices to keep your equipment running smoothly. By following these best practices, you can optimize your lubrication equipment replacement intervals and save money on unnecessary equipment replacement and repairs.
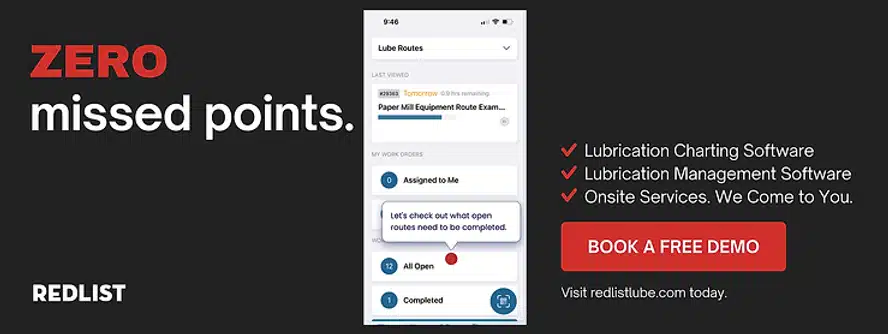
Turn to Lubrication Management Software for Support
Lubrication management software can be a valuable tool for optimizing lubrication equipment replacement intervals. This software can monitor lubrication equipment in real-time, providing alerts when maintenance is needed or replacement intervals are approaching. It can also track data from oil analysis programs and provide recommendations for oil replacement intervals based on this data. Additionally, lubrication management software can help ensure that the correct lubricants are being used and that they are being applied in the right quantities and intervals. By using lubrication management software, companies can reduce equipment downtime, extend equipment life, and increase overall productivity.
In conclusion, optimizing lubrication equipment replacement intervals is critical for ensuring the long-term efficiency and reliability of your machinery. By understanding the factors that impact replacement intervals and following best practices, you can maximize the lifespan of your equipment, reduce downtime, and increase productivity. It is crucial to implement an oil analysis program, consider OEM recommendations, monitor operating conditions, follow lubrication best practices, and utilize lubrication management software for support. With these strategies, you can make informed decisions about lubrication equipment replacement intervals and ensure that your machinery operates at peak performance, ultimately saving money and improving workplace safety. Request a demo today!