The effectiveness of any maintenance plan, preventive or not, relies on your inventory and spare parts management. The challenge is finding the balance between having parts on hand when you need them and not having capital tied up in inventory you won’t need for months. Striking that balance allows you to minimize downtime by eliminating extra repair time due to lacking the necessary parts. However, this is proving to be even more difficult since the pandemic with global supply chain issues. Now, you need to forecast planned maintenance alongside your parts inventory and extended lead times on ordered parts. Redlist provides a solution to optimize maintenance planning with visibility into available staff, parts, and planned downtime.
The Issues with Spare Parts Management
If your maintenance department needs to run on a lean budget, then you are typically stocking parts on an as-needed basis. Managing inventory and costs is the number one issue. But, there are more issues that can complicate your spare parts management:
Ordering Parts
From sourcing vendors and placing orders to tracking the orders, many companies lose track of this process. Often, it is siloed information that only a few people have, or it lives in a binder or spreadsheet.
Receiving and Stocking Parts
Inspecting shipments for defects at delivery is essential, as well as having a log of the part’s storage location. One study found that employees in the construction industry spend 90 minutes per day “looking for stuff”. If your storeroom is unorganized or unclear to the team, your technicians are likely spending more time looking for parts than they need to.
Maintaining Spare Parts
Spare parts have a limited shelf life and require a specific storage environment. For example, rubber should remain out of sunlight, belts should not be hung, and large motor shafts need regular rotation. This has a direct impact on equipment reliability and downtime. Your preventive maintenance plan must include actions to inspect and maintain the health of your spares.
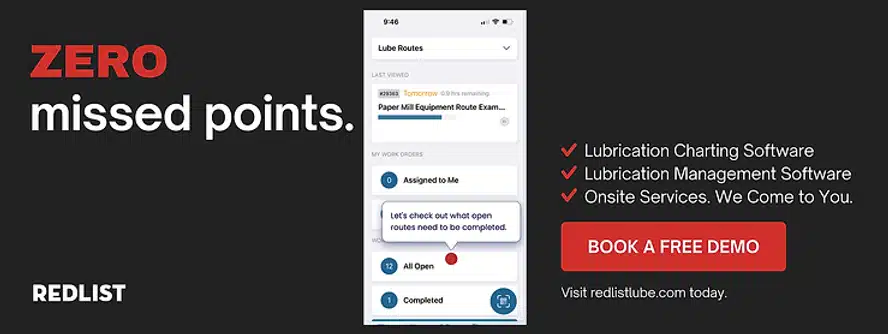
Why Use Redlist for Spare Parts Management?
Redlist’s Enterprise Asset Management (EAM) software gives you visibility into every step of your spare parts and preventive maintenance processes. Moving from paper or spreadsheet-based systems to a cloud-based EAM allows you to:
- Better track inventory
- Identify gaps in parts management for your most critical assets
- Reduce inventory levels
- Plan ahead for various lead times
- Automate maintenance and inspection of spare parts
Redlist is configurable to your specific needs, including setting stock thresholds to trigger an automated restocking notification and automating the maintenance and inspection of spare parts. Furthermore, all of your procurement, usage, and asset data is in one system that fully integrates through your entire maintenance process. Using an EAM means you can create automated work orders for planned preventive maintenance that link directly to the spare parts’ information, even directing your technicians to their precise storage location. You can even utilize the data to rank your most critical assets to prioritize spare parts spend on the equipment that has the biggest downtime impact.
Whenever you’re shutting down a piece of equipment, there’s money involved. Redlist enables you to forecast the parts, people, and time needed to make that repair as efficient as possible. Having access to the right parts at the right time is only one piece of the puzzle. If you can eliminate the issue of missing parts, defective parts, or scheduling maintenance when your technicians aren’t available, then you’ll reduce equipment downtime and its associated costs. An EAM puts all of that information at your fingertips, so your spare parts management and preventive maintenance can run like a well-oiled machine.