Your lubricant is an important part of your business. Not only does it help keep your equipment running smoothly, but it also plays a key role in preventing wear and tear. However, most people don’t think about the importance of lubricant storage until there is a problem. Improper storage can lead to faster lubricant degradation, equipment failure, and even safety risks. In this blog post, we will discuss some tips for improving your lubricant storage. By following these tips, you can help ensure that your lubricants are stored safely and effectively.
Why Do You Need to Improve Your Lubricant Storage?
Optimizing lubricant storage and handling are essential in any industrial or commercial setting. With lubricants being such an important part of many operations and systems, it is necessary to ensure that you properly store and handle lubricants for optimal performance. Not storing lubricants correctly may lead to a mixing of lubricant types, oxidation due to long-term storage, and contamination from improper storage conditions. Additionally, lubricant handling procedures can cause lubricant loss through spills and overages or under-lubrication due to incorrect application.
Having dedicated space for lubricant storage, as well as staying up-to-date on the latest lubrication best practices, can help prevent these issues and make efficient use of lubricants. Optimizing lubricant storage and handling ensure that lubricants remain clean and uncontaminated, minimizing waste and extending equipment life. Ultimately, proper optimization of the lube room is key to providing safe, reliable performance in any industrial setting by keeping maintenance activities running smoothly.
The Lube Room Struggle Many Facilities Face
There are some very common lubricant storage and handling issues that many facilities face, including:
- Lubricants are often stored in various parts of the plant because the lube room is too small.
- Excessive numbers of the same lubricants.
- Inefficient and unorganized lube room.
- The lubricant is exposed to the elements or contaminants or stored outside.
- Storage conditions require technicians to perform labor-intensive lubricant handling.
- Cross-contamination is a risk since many lubricants share a single pump.
- Oil-transfer containers and funnels are left open, allowing dust to enter during the filling process.
Tips for Improving Lubricant Storage and Handling
Designate a Proper Lube Room Space
Your lube room space should have enough room for all of your lubricant storage, but, more specifically, room for the proper storage containers. For example, you need closed cabinets inside the room for storing oil-transfer containers, grease guns, and other accessories. Also, the space you choose for your lube room should be a closed environment free from dust infiltration, large temperature swings, and excessive humidity. Finally, you must include systems for spill containment in your lube room.
Consolidate Your Lubricants
Oils and greases with the same viscosity and grade from multiple suppliers take up more space than necessary. Another issue with redundant lubricants is that they are a major contributor to disorganized lube rooms! So, what do you do? Whenever possible, use a single lubricant vendor. As a result, redundant oils and greases will no longer be an issue. When you consolidate lubricants, you reduce the amount of area required for storage. In addition, this minimizes the mixing and cross-contamination of lubricants.
Implement a Labeling System
Everything in your lube room, including oil containers and grease guns, needs to be labeled to match the labeling of grease application points as well. You can customize your labeling system to even include part numbers and minimum/maximum quantities. This is a vital step in improving your lubricant storage because it greatly reduces cross-contamination! Using colored tanks, transfer containers, and fill points reduces application errors when oils are dispensed.
For example, you can add color-coded plastic washers under grease Zerks to correspond with the correct color-coded grease gun and grease to help you designate a grease gun for each type of grease. You can even ensure that your grease guns are calibrated and outfitted with tags that include the volume distributed in each pump and the date checked to take grease gun labeling to the next level. Finally, your labeling system should support first in first out (FIFO) inventory management. This ensures that the oldest lubricants are used first.
Setup Equipment and Procedures for Contamination Control
A few simple procedures can make a huge impact on the cleanliness of your lubricant. For example:
- Performing lubricant analysis and filtration on all new oils entering the facility.
- Outfitting all oil drums and totes with premium desiccant breathers.
- Having separate sealable and reusable (S&R) containers and filter carts for each lubricant.
- Controlling the climate in the lube room to minimize temperature changes and humidity.
- Filtering all lubricants before use in equipment.
Plan Preventive Maintenance for Your Lubricant Storage
To maintain your new lubricant storage and handling habits, you can carry out a variety of preventive maintenance tasks. Inspecting and maintaining automatic lubrication systems, looking for items that have expired, calibrating grease guns, and checking seals, filters, breathers, and any other lubrication equipment are a few of these.
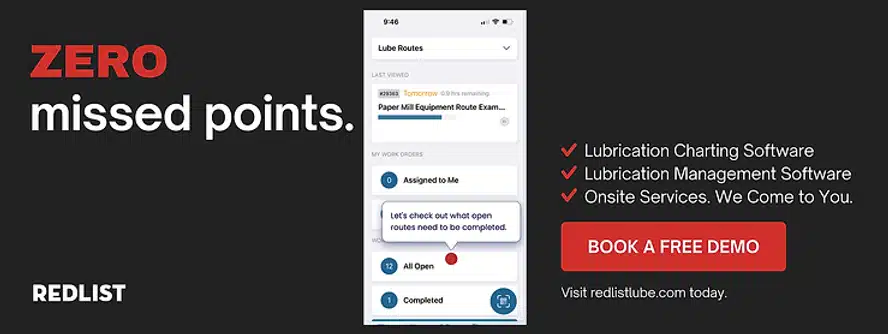
Proper Lubricant Storage is Crucial to Lubrication Management Success
Lubricants are an important part of running any industrial machinery, and having your lubricant storage and handling area properly optimized can make a huge difference in the efficiency of machine operation. Proper lubricant handling decreases waste, prolongs lubricant life, reduces the risk of contamination, and ensures an efficient lubrication planning process. When lubricants are not stored or handled correctly, lubrication plans are disrupted and machines have to work without lubricants. This leads to undesired wear-and-tear on essential machine components from inadequate lubrication, as well as premature breakdowns due to thermal expansion without lubricant. By optimizing your lube room for lubricant storage and handling, you safeguard vital equipment from breakdowns and reduce overall maintenance costs for your plant.