Lubrication is no longer just another low-priority side task. Any modern and competitive industrial organization recognizes that lubrication is critical to achieving its bottom line: asset reliability. Additionally, a world-class lubrication program helps achieve and maintain optimal lubrication levels necessary for maximum asset health and lifespan.
At the center of any successful world-class lubrication program is the Reliability Manager or Engineer. This leadership role propels the program forward and champions its goals and objectives. The role is also essential in creating a lubrication culture that promotes the right lubrication values, motivating employees to support proper lubrication practices. This post will look into the Reliability Engineer’s key role in a successful world-class lubrication program.
Understanding Reliability and Lubrication
To start, let’s define some terms:
Asset or equipment reliability is the ability of an asset (can be a machine, equipment, or infrastructure) to perform its intended function without failure in any given period or operating conditions. Furthermore, asset reliability means continuous operations, minimal downtime, and low maintenance costs.
Lubrication is a major contributing factor to asset reliability. Proper lubrication is the main step that fights against issues that threaten reliability such as friction, premature wear, and corrosion.
Lubrication management is the systematic planning, implementation, and monitoring of lubrication tasks and activities to ensure proper lubrication. Lubrication management spans all the lubrication steps including selection, handling and storage, application, condition monitoring, and continuous improvement.
A world-class lubrication program is a highly coveted state of lubrication management characterized by well-structured lubrication strategies, standardized lubrication steps or processes, integration with proactive maintenance, alignment with global standards, and utilization of up-to-date technological innovations.
A Reliability Engineer is responsible for developing, implementing, and managing lubrication strategies and practices to ensure the achievement of its bottom line. Aside from these management responsibilities and other technical skills, this role must also show leadership by influencing, training, and inspiring others to prioritize and adhere to lubrication best practices.
Establishing a World-Class Lubrication Program
If you are a Reliability Engineer or any lubrication leader aiming to establish a world-class lubrication program, below are the necessary steps to achieve your ultimate goal:
1. Develop a comprehensive lubrication strategy.
A detailed and structured lubrication management strategy consists of guidelines, procedures, and best practices tailored to your organization’s needs. There are several methods and approaches to lubrication management, and each can be better than the other.
However, the best and most effective lubrication strategies depend on your specific conditions and requirements. To develop a comprehensive lubrication strategy for a world-class lubrication program, start by establishing a clear vision and setting specific objectives that align with your organization’s goals.
2. Promote a culture of lubrication for reliability.
The success of any lubrication program is founded on its leader’s commitment to the importance of lubrication for achieving reliability. This commitment will manifest and promote a culture where employees recognize and take this importance to heart, facilitating the effective implementation of lubrication strategies.
Show your commitment to the lubrication program by advocating for best practices and leading by example. Be aware of your personal actions and decisions as these reflect your attitude toward lubrication processes. Moreover, the behavior and actions you demonstrate will influence your team’s support or opposition towards lubrication practices.
3. Establish lubrication training programs.
Technicians, maintenance personnel, and other relevant staff need appropriate training on lubrication techniques, best practices, and the significance of lubrication for asset reliability. Otherwise, you leave the chances of lubrication success to experienced-based, inconsistent, and untransferrable knowledge.
Organize workshops and seminars to educate and engage staff. Develop training curricula and activities based on job roles, levels, and responsibilities. Schedule refresher training sessions periodically to retrain employees and update them on any changes or innovations in your lubrication program.
4. Encourage continuous learning.
Ongoing education and professional development are critical for any employee, especially for those working in lubrication. New methods and technologies are being developed and implemented in this industry all the time.
As a lubrication and reliability leader, you must encourage your team members to stay current with the latest lubrication information and trends. You can also promote learning by providing the necessary resources for your members. For example, you can create a lubrication handbook detailing best practices, procedures, and troubleshooting tips. Update this handbook as often as necessary.
5. Foster collaboration and effective communication.
Collaboration and communication promote a healthy working environment, facilitate the completion of tasks, minimize errors and losses, and provide many more benefits to any business area including lubrication management. Complex lubrication strategies require team members who can work seamlessly together in handling detailed and sensitive tasks.
Foster collaboration by building multi-departmental teams with specific roles and responsibilities for each member. Use tools that prevent communication gaps and promote faster document sharing. Encourage your team members to freely provide their feedback, concerns, and suggestions and have a system to gather and process these inputs.
6. Utilize advanced technologies.
There’s no doubt that technology can enhance every aspect of our lives. Learn to leverage modern technologies to enhance lubrication management processes. There are tools available that can help in gathering lubrication monitoring and other data for asset health visibility and tracking.
You can use advanced data analytics to track lubrication performance, identify trends, and make data-based decisions to enhance reliability. Advocate for and oversee the implementation of lubrication management software to streamline processes and enhance data accuracy.
7. Maintain continuous improvement.
A world-class lubrication program must continuously improve and evolve with the changing demands of any business in any industry. Regularly reviewing a lubrication program and its strategies helps continuously refine and improve these strategies.
You must initiate lubrication audits to identify gaps and areas for improvement. You can also establish a mechanism for feedback for team members, relevant staff, and other stakeholders to gather insights into these improvement areas.
8. Champion problem-solving and root-cause analysis.
Problems and failures are learning opportunities. A world-class lubrication program has a system in place for analyzing problems, using systematic methods that identify root causes and develop corrective actions.
As the leader, you must initiate and support investigations into lubrication-related failures. From the investigation results, you can then develop and lead the implementation of preventive measures for these failures.
9. Ensure proper documentation and standardization.
Lubrication activities must be documented for future reference and accessibility of information. They must also follow standardized processes for consistent results and accuracy. Few organizations consider documentation and standardization to be as essential as other lubrication tasks and thus, are often at the bottom of the lubrication task list.
You must recognize that although documentation and standardization of the lubrication processes seemingly serve no purpose, they provide long-term and substantial benefits. Monitor all documents to ensure the data are correct, organize them accordingly, and store them securely for future needs.
10. Highlight environmental and safety compliance.
World-class lubrication programs comply with environmental regulations and safety standards. These protocols ensure that an organization is upholding its social responsibility and is committed to protecting employee health and well-being.
Ensure the regulatory adherence of your lubrication practices by keeping updated with regulatory laws and ordinances in your areas of operations. Develop, implement, and continuously improve the safety protocols that protect employees from potential workplace hazards.
11. Recognize and reward performance.
Acknowledging excellent performance through recognition and reward boosts lubrication compliance and ultimately enhances asset reliability. A world-class lubrication program uses recognition and reward schemes to motivate and encourage continuous improvement and commitment to high standards.
Develop recognition and rewards programs to fit your team’s needs, dynamics, and available resources. Use a fair and comprehensive set of performance criteria, levels, and reward types (monetary and non-monetary rewards). Measure the impact of your recognition and rewards program by analyzing lubrication performance. If there are minimal or no positive effects, identify improvements and implement them accordingly.
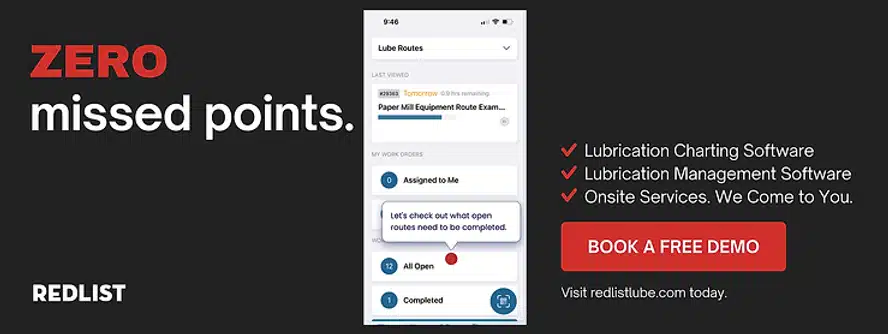
For a World-Class Lubrication Program, Get Redlist!
Leaders of lube management like Reliability Engineers can rely on Redlist for effective and world-class lubrication practices. This all-in-one easy-to-use digital and mobile software is the only platform you’ll need to strategize, collaborate, communicate, track, analyze, improve, and document your lubrication program. Accomplish your reliability goals and more with Redlist.