Lubrication is an essential part of machinery maintenance for nearly every production facility. On average, lubricant purchases only amount to 3% of a maintenance budget. But, lubrication-related activities can influence an average of 40% of total maintenance costs. Facilities can reduce wear and tear, extend equipment life, and improve overall efficiency with proper lubrication. In addition, lubrication can help prevent costly downtime due to unexpected repairs. As a result, regular lubrication is an essential part of any machinery maintenance plan. While lubrication tasks can be done manually, you may look to automatic lubrication to save time and ensure consistent lubrication. In this post, we’ll consider the benefits of each and how to decide between the two.
Lubrication Management Factors to Consider
There are numerous factors to attain the highest levels of reliability and benefits from a lubrication management program. The five R’s of lubrication encompass these factors:
- Right Lubricant
- Right Quantity
- Right Time
- Right Point
- Right Method
The complete mapping of all lubrication routes, including their operating circumstances, lubrication needs, and criticality, will serve as the foundation of an efficient lubrication program. This information is required to determine the best lubricant, the necessary amount, and the appropriate relubrication intervals (the first three R’s). To prevent cross-contamination, the fourth R refers to best practices, such as labeling, color-coding, or other methodologies of both lubricating points and tools. After considering the above variables, you’re finally ready to look at your method and choose between manual or automatic lubrication.
Benefits of Automated Lubrication
Improved Machinery Uptime
One of the biggest advantages of using an automated lubrication system is that it can help improve the overall uptime of your machinery. When done manually, lubricating your equipment can be a time-consuming process that takes away production time. However, with an automated system, you can set it and forget it. This frees up your employees to focus on other tasks. In addition, because these systems are designed to dispense the right amount of lubricant at the right time, you can be sure that you are properly lubricating your equipment at all times. This is something that can be difficult to guarantee with manual lubrication.
Reduced Maintenance Costs
In addition to improved uptime, automating your lubrication process can also help to reduce your overall maintenance costs. When machinery is properly lubricated, it can run more efficiently and with less wear and tear on parts. This not only prolongs the life of your equipment but also reduces the number of repairs you must perform over time.
Fewer Lubrication Management Health and Safety Risks
Another benefit of automated lubrication systems is that they can help to improve health and safety in the workplace. When done manually, applying lubricant to machinery can be a messy and dangerous job. However, with an automated system, you can complete this task without putting employees at risk.
Benefits of Manual Lubrication
Cost Savings
One of the biggest benefits of manual lubrication is that it can save your business money. Automatic lubrication systems require electricity to operate, which adds up over time. Manual lubrication, on the other hand, does not require any electricity to operate, which means that you’ll be able to save money on your energy bills.
Increased Lubrication Management Flexibility
Another big benefit of manual lubrication is that it offers your business increased flexibility. With an automatic lubrication system, you’re limited to the size and shape of the reservoir that you choose. This can be problematic if you need to change the amount of grease that you’re using or if you need to access tight spaces. With manual lubrication, however, you’re not limited by the size or shape of the reservoir, which means that you’ll be able to get into those tight spaces and apply just the right amount of grease.
Less Maintenance
Manual lubrication requires less maintenance than automatic lubrication systems. Automatic lubrication systems have pumps and moving parts that are susceptible to wear and tear. That basically adds another asset to your list of equipment that needs to be regularly serviced and maintained. Manual lubrication systems, on the other hand, don’t have any moving parts, which means that they don’t require as much maintenance.
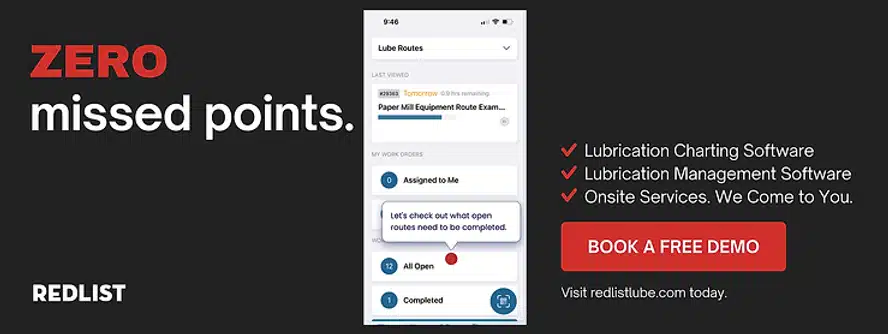
How to Choose the Best Lubrication Management Method
You should take into account the benefits and drawbacks of manual and automatic lubrication while making your choice. Additionally, lubrication-related expenses account for about 5% of labor expenditures. If you do decide to add automatic lubrication to your lubrication management, there is one final detail to consider: Asset Criticality Ranking.
A comprehensive criticality analysis of each asset will show the impact of a failure in terms of:
- Total Production Cost
- Total Cost of Maintenance
- Environmental Consequences
- Personnel Health and Safety
Typically, the most critical assets are the first targets of automatic lubrication.
So, which is the right choice for your business? As you can see, there are benefits to both manual and automatic lubrication systems. The best way to decide which one is right for your needs is to consult with an expert who can assess your specific situation and make a recommendation. Whichever type of system you choose, proper lubrication management will help extend the life of your equipment and improve overall efficiency.