No matter what industry you work in, there’s one thing that’s always important for your equipment: Lubrication management. One of the best ways to automate lubrication for large plants is to have the right lube oil system in place. Not only does this ensure your equipment runs smoothly and reliably, but it also helps prevent wear and tear, which can save you time and money in the long run. So how do you choose the right lube oil system for your business? There are many factors to consider, such as the type of equipment and the operating environment. In this blog post, we’ll discuss some of the most important things to keep in mind when making your decision.
What is a Lube Oil System?
You may know a lube oil system as a lube skid or a circulating oil system. It continuously supplies lubrication and cooling to gas turbines, blowers, gearboxes, bearings, and other industrial equipment. Lube oil systems help by:
- Storing lubricant
- Minimizing temperature changes
- Reducing circulation of contaminants by causing them to settle
As part of a single-source system, your bearing manufacturer may provide a lube oil system. If you don’t have a lube oil system, but your bearings are overheating or displaying wear, then you should consider implementing a lube oil system.
How Does a Lube Oil System Work?
Lube oil systems may not require any type of control at all, except for their power supply. Until you need to replace a filter, the system operates in a loop and works without interruption. While not every lube oil system will be the same, these are some common features:
- Cooling
- Installed at a lower elevation than equipment, so lubricant is pumped to equipment and returns by gravity.
- A baffle in the reservoir settles larger contaminants
- An additional strainer traps particles that didn’t settle in the reservoir
- Another filter catches fine particles before the oil returns to the machinery.
- A bypass valve allows excess lubricant above the ideal flow to return to the reservoir.
Tips for Choosing the Right Lube Oil System
You can configure a lube oil system for many different applications and setups. You should check with your equipment manufacturer for the precise flow rate, system pressure, fluid type, and operating temperature. However, you will have control over the size of the connected pipework, line lengths, installation location, ambient temperature, power availability, and safety factors.
To handle challenging environments or provide data on operation, you can incorporate instruments and electrical controls. For example, you may want your lube oil system to have automatic warnings and backup support in the event of a malfunction or breakdown. A fail-safe system can make sure that the equipment receives a continuous flow of lubrication, even if something happens. Such safety measures might be necessary if the equipment starts and stops frequently, if the load or rotation speed fluctuates, if the temperature varies, or if the environment is prone to dirt and debris.
Occasionally, bearings must operate uninterrupted, which requires the lube oil system to do the same. You can include system redundancy in the design. A dual filter system features separate piping and control valves so that the oil flow continues even while you’re changing the filter. Another example is a secondary pump and motor built into the system. This serves as a backup during service or replacement of the original pump and motor, allowing the lube oil system to remain operational at all times.
Lube Oil System Requirements to Consider
Flow Rate
The flow rate must match the total requirements when the lube oil system is supplying more than one bearing. At the delivery point, you will have a needle valve to regulate the flow into the bearing. Also, it is essential to size the pump and motor to provide the maximum flow rate necessary, plus a little buffer.
Pressure
A common operating pressure is 35 psi (pounds per square inch) or less. You many need higher pressures for specialized applications, like a system that suspends a bearing in lubricant during startup to prevent metal-to-metal contact. The capacity of the pump is the main factor in determining the highest amount of pressure possible. You can increase system pressure by adjusting the bypass relief valve so that less oil enters the bearing.
Pumps and Motors
Different voltages, frequencies, and phases of motors are available to best match the available power sources. The usual motor has a TEFC (totally enclosed, fan-cooled) rating and is appropriate for a variety of industrial settings. You may require an explosion-proof rating, if your system will be near flammable vapors and dust. For an explosion-proof motor, you need to identify the class, division, and group.
Filtration
Most lube oil systems have three types of filtration. First is a baffle that divides the reservoir. This creates passive filtration as particles settle and oil flows over the top of the baffle. To achieve the second stage of filtering, the fluid passes through a mesh strainer on its way out of the reservoir. Final filtration, often using a 23-micron filter, takes place before the fluid returns to your machinery. To maintain lubricant cleanliness, you should regularly clean the strainer and monitor the filter for timely replacement.
Gauges
Gauges are essential for tracking the operating conditions of your lube oil system. A pressure gauge between the pump and bypass valve prevents excessive pressure buildup. Next, a liquid-level gauge with a built-in thermometer enables you to see the temperature of the fluid inside the tank. If you need to monitor lubricant temperature after going through a heat exchanger, you can install a temperature gauge in the piping. Additionally, you can even have a differential pressure gauge to monitor the pressure loss from filtration. If system pressure drops, it may be time to replace your filter.
Switches
Electronic controls can use switch signals to activate alarms, control how a unit operates, communicate data to monitoring stations, or shut down machinery. The heat exchanger can be signaled as the temperature rises or turned on using a temperature switch. In the event of system loss or insufficient fluid return from the bearing, a liquid-level switch can signal that there is not enough oil in the tank. If there is an unanticipated limitation of flow in the piping or at the bearing, you can also use a liquid-level switch to notify when the tank level is high.
If the flow falls below a preset threshold, a low-flow switch turns on. This can occur because of a clogged filter, a broken pump, a power outage, or drained fluid. The switch’s signal can provide an important advance warning for corrective action. Finally, after passing through the filter, a differential pressure switch alerts the user that the pressure has increased. This suggests that the filter needs to be changed.
Heat Exchangers
Bringing the oil’s temperature down before reintroducing it to the bearing is the function of a heat exchanger. Through the use of heat exchangers, heat transfers from the lubricant to the air or water. In the case of an air-cooled heat exchanger, oil circulates through a network of smaller pipes with air blown over them by a fan. Alternatively, a water-cooled heat exchanger involves the piping passing through a cylinder that receives a constant flow of water.
To choose the right heat exchanger for your application, you need to know the temperature of the oil as it leaves the bearing and the requisite temperature for its return. Then, you can calculate the BTUs (British thermal units) to remove per hour. When using an air-cooled heat exchanger, the oil temperature can only go as low as the temperature of the ambient air. A bigger heat exchanger will be necessary as the ambient temperature rises. A water-cooled heat exchanger provides greater efficiency with a lower water temperature and higher water flow. An attendant can run a heat exchanger manually, it can run nonstop, or it can be automated using a temperature switch or data from a temperature gauge.
Immersion Heaters
Immersion heaters work in contact with the lubricant in the reservoir to increase the temperature. This is ideal for systems in cold climates, as it warms the lubricant for a better startup. Before being circulated to the bearing, the immersion heater warms the oil until it is at the proper viscosity. When it reaches the optimal temperature, the heater self-regulates with a built-in thermostat.
Installation Environment
The environment arround a lube oil system can impact its performance. For best results, the design should take into account the altitude, climate, and exposure to the elements. The dimensions of the tank, location of components, and the layout of the piping are all influenced by the space available for the unit.
For the oil to return to the lube oil system by gravity, the bearing needs to be located higher up than the system. To prevent backup, the return line needs to be vented and two sizes larger than the supply line. Elevation of the bearing, decreases in pipe size, and any obstructions from manifolds or nozzles can all have an impact on the pressure needed to provide oil to the bearing.
Reservoirs and Piping
A typical reservoir is made of welded steel with a heavy-gauge steel cover. It serves as a platform for mounting system parts. Typically, national pipe thread (NPT) fittings are used on iron pipes and fittings. To prevent corrosion, the entire system needs to be painted or coated. However, stainless steel can also be used for reservoirs and pipes. Before being put into service, lube oil systems should be checked for component functionality and leak detection.
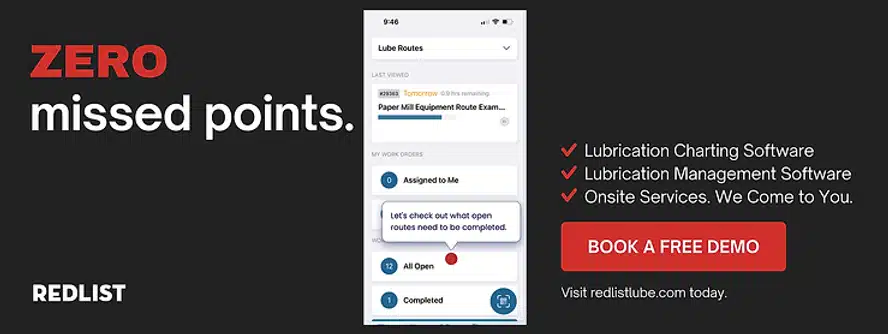
Thorough Lube Oil System Planning Makes a Difference
When it comes to lube oil systems, there is no one size fits all solution. Determine the ideal operating circumstances in close consultation with the bearing manufacturer. Inform your lube oil system builder of the tasks you require the system to do. Include in your design the fail-safes, upkeep, and durability that are appropriate for your application. The system’s effectiveness will depend on how well you thought through all of these details for the design.