Reliability is all about ensuring the optimum performance, longevity, and safety of machinery. It is the bottom line of any organization whose operations depend on machinery and technology. Reliability reports are central to the efforts to achieve this bottom line. This post explores the critical role of reliability reports in enhancing machinery performance, longevity, and overall machine reliability.
What is a Reliability Report?
A reliability report is a document that contains a detailed record and analysis of reliability information. This information may include but is not limited to machinery performance, maintenance, failures, and operational requirements. Reliability reports provide information that can highlight a machine’s performance trends, potential for failure, and areas of improvement.
Key Components of Reliability Reports
The information that reliability reports contain can vary depending on the industry and assets involved. Most reports, however, typically include the following components:
- Failure Analysis – Reliability reports record all the information on failures encountered by a machine, including description and frequency of failures, possible causes, and the impact on operations.
- Performance Metrics – Reliability reports present metrics such as Mean Time Between Failures (MTBF) and Mean Time To Repair (MTTR) to provide insight into machinery performance and availability.
- Maintenance Records – Reliability reports also contain the schedules, procedures, recommendations, and other pertinent information on all maintenance activities, including preventive and corrective maintenance.
- Condition Monitoring Data – Reliability reports also present data on current condition monitoring techniques like vibration analysis or oil analysis, providing insights into machinery health or condition.
- Risk Assessment – Reliability reports can contain a section that identifies potential failures and their associated risks, analyzes the impacts of these failures, and recommends measures to mitigate them.
- Cost Analysis – Reliability reports include a component that analyzes the costs involved in the pursuit of reliability, providing insights that can help minimize expenses while still achieving and maintaining reliability.
- Recommendations – Reliability reports provide suggestions for improving any current reliability-involved framework or procedures, pushing the continuous enhancement of reliability in an organization.
Reliability Reports Enhance Machine Performance
In essence, reliability reports enhance machine performance due to systematic data collection and analysis. This is through several ways, which include:
Identifying weak points.
The data in reliability reports highlight the weak points or problem areas in machine performance. Thus, maintenance teams can more effectively enhance machine performance by planning and executing the necessary actions to target these points.
Optimizing maintenance strategies.
By collecting and analyzing maintenance data, reliability reports help in the effective scheduling and prioritization of maintenance activities. With this, organizations can ensure that no maintenance efforts go to waste and that all are contributing towards improving machine health and performance.
Improving operational procedures.
Reliability reports provide accurate performance data that aid in implementing operational best practices that maximize efficiency and minimize wear and tear. This data also helps in adjusting standard operating procedures (SOPs), lubrication practices, and workflows to produce the least amount of stress on machinery.
Facilitating decision-making.
Reliability reports make data-based decision-making possible. If backed by actual data, decision-makers can easily approve major capital investments or allocate resources to reliability strategies. Thus, the investments and strategies that are necessary for enhancing machine performance are more accessible through reliability reports.
Reliability Reports Promote Machine Longevity
On top of supporting optimum machinery performance, the practice of creating reliability reports also promotes machine longevity. This is through the following ways:
Preventing failure proactively.
Through reliability reports, teams can have a better understanding of the failures that shorten the lifespan of machinery. Thus, they can develop more proactive measures to prevent these failures and extend machinery longevity.
Allocating resources effectively.
Reliability reports shed light on reliability activities and the resources used to implement them. Hence, reliability reports help teams in allocating the necessary resources to activities that are critical for promoting machine longevity. Regular parts replacement or recalibration, for example, require a sizable budget because they are critical activities for machine longevity.
Training machine users properly.
Reliability reports provide critical and continuously updated machinery information. Thus, they are essential tools in training operators, maintenance staff, and other users of the machinery on the proper ways to operate, maintain, troubleshoot, or repair them, hence promoting machine longevity.
Ensuring safety and compliance.
Reliability reports help teams in keeping historical records and documentation on all maintenance and reliability activities. These records ensure safe operating conditions and compliance with industry regulations. By operating machines and equipment in safe, industry-approved conditions, you are sure to achieve their maximum lifespans.
Implementing Reliability Reports: A Practical Example
Below is a practical example to illustrate how to successfully implement the creation of reliability reports.
- Define objectives and scope: Reduce production downtime by 20% by focusing on the reliability of production machinery.
- Gather data: Use a centralized system to collect and store data. Train maintenance team members to promptly and accurately collect data.
- Organize and analyze data: Review data and arrange them by asset, type, and frequency. Conduct regular reviews to ensure data are complete and properly collected. Analyze data using root cause analysis and other appropriate methods.
- Issue recommendations and actions: Implement actions to address the analysis results. Prioritize areas with high impact or criticality. Address lubrication issues.
- Improve continuously: Update reports monthly. Measure the impact of actions by gathering data and analyzing them continuously. Track monthly downtime and maintenance costs to measure the impact of actions taken.
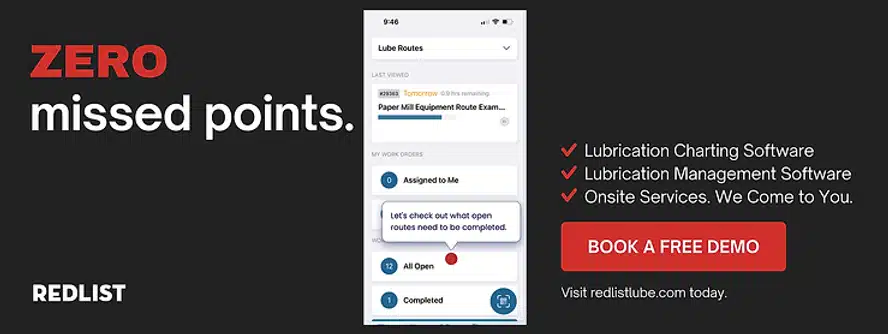
Create Reliability Reports with Redlist
Do not let the seemingly complicated idea of reliability reports intimidate you. You can leverage technologies like Redlist to create accurate and effective reliability reports to achieve your reliability goals.
Redlist is a computerized maintenance management system (CMMS), powerful software that can systematically collect, analyze, and present data on machine performance, failures, and maintenance activities. With this tool, you are only a few clicks away from generating accurate and real-time reliability reports.
Simply set up your system, collect your data, and let Redlist analyze, visualize, and document the results for you. Start using Redlist to create your reliability reports today. Contact our reliability experts to schedule your free demo now!