Every organization, regardless of industry, must modernize to remain competitive. Technology is a tool, if used properly, that can make a big difference in a company’s goal to minimize costs and increase revenue. One of these essential tools is software applications for managing maintenance and lubrication programs. In this post, we explore how Redlist, a next-generation application, improves lube management more effectively than commonly used alternatives such as Lube-IT and MAINTelligence.
What is Lube Management?
To understand how Redlist works, you must start by understanding the basics of lubrication management. Lube management, in general, is the process of systematically controlling lubrication processes such as selecting, applying, monitoring, and disposing of lubricants.
Lube management aims to optimize the use of lubricants, ensuring that every lubrication step benefits the efficiency and lifespan of company assets while minimizing the costs involved. To achieve its goals, lubrication management relies on the standardized implementation of lubrication tasks and the timely collection, organization, and analysis of data. These are the areas that are greatly improved with the use of Redlist’s lubrication management software.
How Does a Lube Management Software Work?
The features and functionalities of lube management software vary according to the system and system provider. They also depend on how the user utilizes the system and the assets or processes involved. Most lube management software, in general, works as a digital platform for lubrication tasks, allowing you to:
- Schedule lubrication tasks
- Store asset and lubricant information
- Track assets and lubrication inventory
- Collect lubrication data
- Generate data reports and analytics
- Access information from on-site and off-site devices
How Redlist Stands Out
There are several useful lube management software out there, but Redlist is a clear stand out among all of them. Redlist is superior to other lube management solutions for its:
Cutting-Edge Technology
Redlist uses only the most advanced technologies for its system. With its user-friendly interface, Redlist can be easily used by anyone, regardless of background or technological skill.
Furthermore, Redlist’s innovative system provides comprehensive analytics, letting users gain insights necessary to make lubrication decisions. With powerful computing technology, a few finger taps are enough to generate metrics on lubrication schedules, asset health status, or predictive maintenance programs.
Finally, and most importantly, this system is customizable to fit any type of industry, asset, process, etc. The most sophisticated software is worthless if it does not fit your specific lubrication needs.
Focus on User Education
Redlist believes that the successful implementation of its lube management solutions relies heavily on the end-users of the system. Thus, Redlist maintains a focus on user education, making sure that they understand and apply proper system utilization steps. By doing so, users can get the most benefit out of their system while elevating the industry standard for lube management solutions.
Redlist conducts regular online sessions with its users, providing regular updates on the latest trends and best practices in lubrication technology. Aside from workshops and webinars, Redlist also maintains an extensive collection of resources including guides for use and troubleshooting, case studies, and other informative articles.
Modern Approach and Adaptability
Finally, Redlist’s success in providing the best lube management software is a result of its modern approach and adaptability. Redlist recognizes that every business is unique and will grow over time, thus requiring a system that is flexible to adapt to the changes that come with growth.
Redlist’s system is highly capable of integration with any existing system within an organization. You can customize the features you need to fit and work with your current systems. As you use the system, you can add or remove features based on your experience or changing lube management needs.
Real-Life Redlist Lube Management Software Results
To illustrate some of the many benefits of using Redlist, read about the results of several case studies below:
Case Study 1: Engineering Services Company Saves 240 Hours per Engineer
A company that provides preventive maintenance and lubrication program equipment inspections and monitoring services used Redlist and it was able to save up to 240 hours for every engineer. Redlist eliminated manual spreadsheet entry, allowing engineers to collect data faster and with more accuracy. As a result, inspections are completed in less time, and data is organized and analyzed more easily.
Before Redlist, the company projects would take up to three months and multiple staff to complete. With Redlist, projects can be completed in 2-3 weeks by a single person.
Case Study 2: Sustainable Wood Production Company Attains 100% Lube Route Compliance
Redlist was used by a company without any prior lubrication management plan in place. The company created a comprehensive lubrication management plan for its current facility. With Redlist’s help, the company completed 100% of its lubrication routes at the right frequencies. As a result, bearing failures due to lubrication were eliminated and asset reliability increased.
Furthermore, Redlist increased production yield from the original 200 cubic meters to 800 cubic meters after only 2 months of implementation. On top of that, the company also achieved a $180,000/year savings on lubrication labor and $300,000 in downtime savings.
Case Study 3: Metal Manufacturing Company Saves Over $200,000
An asset-heavy company with a large workforce used Redlist to expand and improve its lubrication program. The company used Redlist to assign technician lubrication tasks and collect information as they executed these tasks. After only one month of implementation, the company was convinced of the benefits of Redlist.
The company reports a total of $209,070 in savings in the first year of using Redlist. The maintenance team detected and fixed 66 major asset issues before they escalated into catastrophic failures, saving the company $165,000 in downtime costs. Redlist also saved the company $24,750 on critical machine component replacements. The improved lubrication program also resulted in less stressed employees and a safer work environment, saving the company $19,320 in OSHA (Occupational Safety and Health Administration) fines.
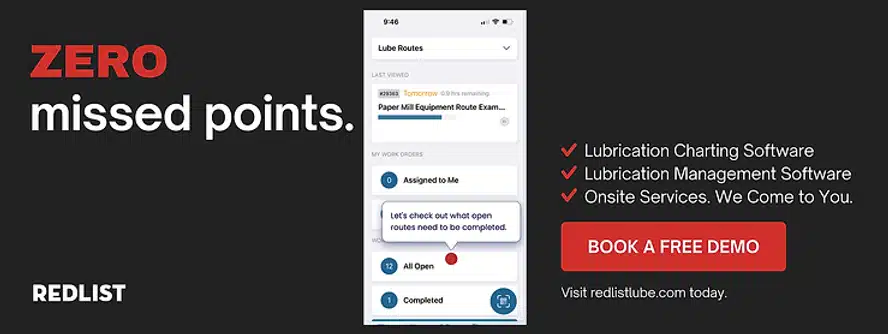
Get the Most Lube Management Benefits with Redlist
Redlist surpasses traditional options like Lube-IT and DMSI Software in terms of technology, user services, and adaptability. Click here to learn more about our Lubrication Management Software. Redlist’s benefits have been experienced and enjoyed by a wide range of industries, it’s time you experience it yourself. Get Redlist and get more benefits, schedule a free demo today!
