Bearings are critical to the reliability of machines. A machine’s ability to perform depends on the health of its bearings. And maintaining bearing health depends on proper lubrication. In our previous webinar with Reliability Solutions’ Tim Dunton, we talked about the steps in achieving and maintaining a successful lubrication program. In doing so, we also talked a lot about lubricating bearings. You can check out the webinar here.
Rarely do we talk about machine lubrication without citing examples of bearing lubrication. In fact, the majority of lubrication a machine receives is focused on its bearings. In this article, we elaborate on the principles of bearing lubrication briefly discussed in the webinar.
What is a Bearing?
A bearing is part of a machine that allows it to move and rotate without excessive friction. It reduces friction between a machine’s moving parts, allowing these parts to move with better speed and efficiency. A bearing is also called that because as it promotes movement and reduces friction, it also ‘bears’ the stress that builds up as moving parts slide or roll against each other.
Bearings come in several types for varied purposes and functions, but in general, they consist of the following components:
- Rings – one inner and one outer, with raceways
- Rolling elements – rollers or balls
- Cage – separates rolling elements and acts as a motion guide
How Bearing Lubrication Works
Because bearings act as the cushion between moving machine parts, they are the first components to experience wear and tear. And, machines with heavy loads, extreme temperatures, excessive dirt, or water contamination are subject to faster bearing wear. So, bearing lubrication aims to extend the life of a machine’s bearings, especially for equipment that is exposed to high levels of wear and tear. Lubricants form a film around the bearing components to reduce friction, dissipate heat, and protect from contamination. Simply put, the thicker the oil film, the longer the bearing life.
Pitfalls in Bearing Lubrication
The following are some of the factors that if not considered, result in bearing lubrication failure:
Using the Wrong Viscosity
The key player in this game is viscosity, which determines the thickness of the protective film around your bearing. But here’s the catch: as temperatures rise, viscosity decreases. So, finding the right viscosity based on the expected operating conditions is critical. But here’s an important tip: managing viscosity isn’t as straightforward as it may seem. Increasing viscosity might create a thicker oil film, but it can also ramp up fluid friction within the bearing, causing even more heat and friction—without actually fixing anything. So, be cautious when adjusting viscosity and ensure you have the correct specifications.
Remember, viscosity is the superstar when it comes to selecting a lubricant. While other properties and additives can be helpful, they won’t make much of a difference if the viscosity isn’t spot-on. So, if you want your bearings to work like a well-oiled machine—smoothly and efficiently—keep a close eye on the viscosity of your lubricant. It’s the secret to unlocking peak performance!
High Operating Temperatures
Here’s the science behind it all: temperature plays a crucial role because of a fundamental law of chemistry. For every 10 degrees Celsius increase in temperature, chemical reactions double in rate. What does that mean for your lubricant? Well, if the temperature rises, the lifespan of the lubricant is cut in half. Imagine running a bearing at a temperature much higher than it was designed for—it’s like giving it an early retirement notice!
You want a lubricant that can handle the heat without breaking down. Why does this matter? Well, when oils are exposed to high temperatures, they can darken and their viscosity can change. But that’s not all. Nasty deposits like varnishes and gums can also start to form, causing headaches in hydraulic systems with tight clearances.
Water Contamination
This seemingly innocent contaminant can wreak havoc and spell trouble for your bearings. Even at low concentrations of just 200 parts per million, water has the power to slash the lifespan of your bearings in half. To put it into perspective, imagine one drop of water in a whopping 14 gallons of liquid—that’s equivalent to just one part per million.
Now, here’s the deal: any amount of moisture present in your lubricants can be harmful. Additives, like emulsifiers, can help by keeping water at bay, preventing it from forming an emulsion. It’s a bit like how Rain-X keeps water off your windshield, creating a barrier between your precious bearings and the damaging effects of water. But, don’t underestimate the power of water when it comes to your bearings.
Over-lubrication of Bearings
It’s only natural to think that adding more grease to a hot bearing would cool it down, but here’s the surprising truth: it’s actually the wrong move. Over-lubrication is a common pitfall that causes more harm to bearings than under-lubrication. Keep in mind that the various ways to calculate lubrication amount and frequency offer baseline figures, and different types of bearings may require more frequent lubrication. The shape of the bearing plays a role in how the lubricant is distributed, with some bearings being more efficient at ejecting excess lubricant than others. Mastering the art of lubrication is essential for the longevity and optimal performance of your bearings. So, strike the perfect balance—apply the right amount of lubricant at the right intervals, and your machines will thank you with smooth operation and extended lifespans.
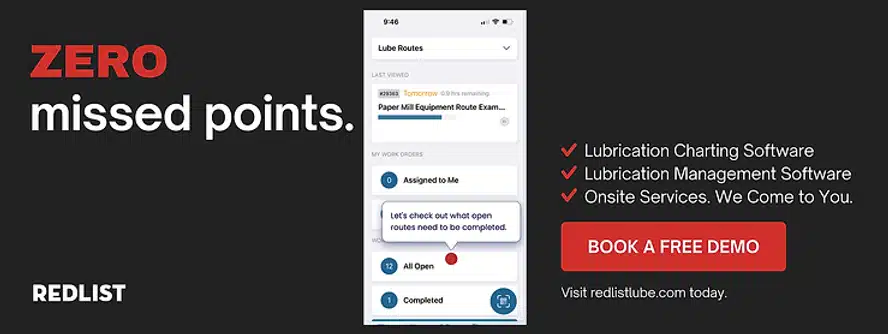
Optimize Your Bearing Lubrication Management
In the quest to ensure the reliability and longevity of machines, the importance of proper bearing lubrication cannot be overstated. Bearings are the lifeblood of a machine, enabling smooth movement and reducing friction between its various components. Maintaining the health of these bearings relies heavily on effective lubrication practices. Throughout this blog post, we have explored the principles of bearing lubrication and identified common pitfalls that can lead to lubrication failure. However, to successfully manage the lubrication of bearings and ensure their reliable operation, implementing digital Lubrication Management software can be highly beneficial. Redlist provides a comprehensive platform for tracking and scheduling lubrication tasks, maintaining records, and generating alerts for timely maintenance. It streamlines the lubrication process, enhances efficiency, and minimizes the risk of human error.
To learn more about the 5 Steps to Maintaining a Successful Lubrication Program and how you can benefit from digital lubrication management, click here for the full webinar with a Certified Maintenance and Reliability Professional with over 30 years of experience.