Proper lubrication is essential for the reliable operation of machines and equipment. And, oil level control is a critical aspect of maintaining optimal lubrication. In this blog post, we will explore the importance of oil level control in optimizing the reliability of bearings, gears, and engines. Either an inadequate or excess oil level can lead to problems such as bearing failure, gear damage, and engine wear. So, maintaining the correct oil level can help prolong the lifespan of these components and reduce the risk of breakdowns. Whether you are a maintenance professional, a facility manager, or simply someone interested in keeping your equipment running smoothly, you’ll find valuable insights in this post about how oil level control can have a significant impact on the reliability of your machines and equipment.
Why is Oil Level Important?
Any lubrication management program’s overall objective is to reduce downtime and equipment breakdowns. The right oil level is one of the obvious and less-obvious critical components of proper lubrication. But, what exactly is the “correct level” of lubricant? And, how do you determine the “right” quantity in the first place? Simply put, the appropriate level is the level at which the component delivers its maximum level of performance.
Size and Speed Determine Optimal Oil Level
No matter if the component is a bearing, gearbox, motor, pump, or hydraulic system, size is a significant factor in determining how much lubrication it needs. Naturally, greater bearing sizes in greased applications require more grease. Similarly, larger reservoirs in oiled applications demand more oil. However, due to the requirements for lubricant dispersion and needed film thickness, speed also influences lubricant levels. Speed impacts grease application quantities differently than oiled applications.
For instance, a slow-moving greased bearing will probably require more grease during installation. This is because the low speed will prevent the grease from being effectively disseminated. On a bearing with a greater speed, you will need slightly less grease, since the grease will spread more quickly and freely throughout the bearing.
Besides that, the viscosity required for optimal lubrication will vary depending on the load and the speed. In terms of oiled applications, splash-lubricated parts moving at higher speeds may need less oil to achieve the right fluid film thickness. You may need a bigger volume for a splash-lubricated system operating at a lower speed.
Inspections: A Vital Task for Oil Level Maintenance
While routine inspections are likely part of your preventive maintenance program, inspections don’t stop there. Everyone who works at the facility, including operators, maintenance technicians, lubrication technicians, managers, etc., is responsible for inspections. Nobody is as familiar with the equipment as those who work with it every day. When you move through the floor, pay attention to vibrations, sounds, and odors. Additionally, everyone can keep an eye out for low oil levels or lubricant leaking from machinery.
What are the Risks of High Oil Level?
If you overfill your lubricant, you run the risk of increased friction in your equipment. This generates heat, which causes machines to malfunction. When a machine malfunctions, it begins to break down and introduces debris and particles into the oil.
Whether it’s over-greasing or over-oiling, overfilling is bad for any equipment. If you overfill a gearbox or pump, pressure will increase and could lead to seal failure. A seal failure may not be immediately catastrophic, but it comes with consequences. When a seal breaks, air, dust, water, or any other airborne contaminants will enter your machine. This series of events results in equipment failure and downtime.
What is the Impact of Low Oil Level?
Many of the same problems that overfilling causes can also result from underfilling or starvation. A component with insufficient oil or grease will experience excessive friction. This increases the risk of adhesive wear because it lacks the fluid film thickness necessary to meet boundary film requirements. Particularly in machines with hard starts and stops, this will be damaging.
Inadequate lubrication will result in overheating, additive depletion, and lubricant deterioration in addition to adhesive wear. A lubricant’s viscosity will drop significantly if the temperature increases above the upper range of tolerances. One of the most vital factors to take into account while choosing the right lubricant is viscosity. Therefore, if you don’t fill the required volume, it will ultimately degrade. This causes it to lose its proper lubricating capacity, even if you chose the right viscosity and additive package for the application.
Oil Level Tips
Get Precise with Your Gauges
Particularly for big volume reservoirs with columnar level gauges, running level and down level are relevant. You check the oil level using a red and green level indication on Luneta columnar gauges, which is present both while the machine is working and when it is not. Otherwise, many facilities have columnar level gauges that have two permanent marker lines. While that is ok, permanent marker isn’t always permanent, especially in industrial chemical facilities. Consider using a physical marker, such as colored hose clamps or zip ties, which can’t wear off easily. When you’re dealing with something as important as your oil level on critical machinery, you need to be precise.
Don’t Forget Stored Equipment
The amount of lubricant in assets like gearboxes, bearings, motors, and pumps that you keep in storage should also be considered. Even if they don’t need to be checked as frequently as assets that are in use, it is still a good idea to make sure that the right amount of lubricant is present and that the asset is receiving lubrication, usually by rotating the shafts and periodically checking for leaks and lubricant level. This will guarantee that your backups are ready for use at all times.
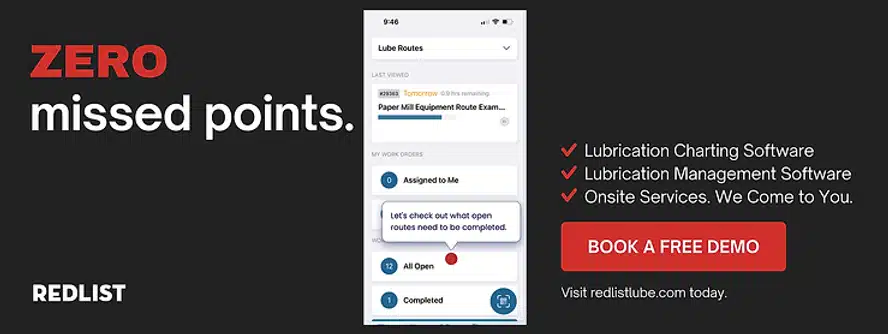
One Piece to the Big Asset Reliability Puzzle
Asset reliability is essential for companies in order to avoid costly shut-downs and repairs. Oil level is one aspect of many that must be regularly monitored in order to ensure asset reliability. This blog post covers why oil level is important, what risks are associated with high or low oil levels, and provides some tips on incorporating oil level monitoring into your company’s routine maintenance plans. Regular inspections, precise gauges, and taking into account stored equipment are all key factors in maintaining optimal oil levels. By following these guidelines, you can help extend the life of your assets and avoid unplanned downtime.