Considering that an average maintenance team handles over 2,300 work orders per year, a maintenance backlog is inevitable. Maintenance backlog includes any recurring repairs, preventive maintenance, predictive maintenance, or tasks planned for scheduled downtime that are overdue. While it is normal to have some backlog due to fluctuations in the daily schedule or unforeseen events, there are some key things to watch for.
Maintenance Backlog Red Flags
A sudden spike in a backlog or a massive amount of overdue tasks are a red flag for a few things. For many, it signals that your maintenance is more reactive than it is preventive. Your goal should be around 80% preventive maintenance and 20% reactive. Certainly, the backlog is a sign to analyze your work order data to determine what is taking up your technicians’ time.
Next, pay close attention to what specific assets have a maintenance backlog. Do you have a lot of backlog tasks associated with your mission-critical assets that cost the most in production downtime? Or, is it mostly for less essential assets that won’t have a catastrophic impact? You may want to look at your preventive maintenance plan to remove unnecessary tasks based on your usage. Optimizing your process and freeing up resources to work on the backlog will reduce the chance of equipment failure from missed maintenance.
Common Causes of Maintenance Backlog
The answer to reducing backlog isn’t simply hiring more maintenance technicians. Instead, it helps to look at what is causing your growing maintenance backlog. The most common causes are:
- Required spare parts weren’t available
- Technicians with the skills or training weren’t available
- Work orders were missed or forgotten
- You need to schedule a third-party expert or vendor
- Work delays due to higher priority tasks coming up or a techs previous work orders taking longer than expected
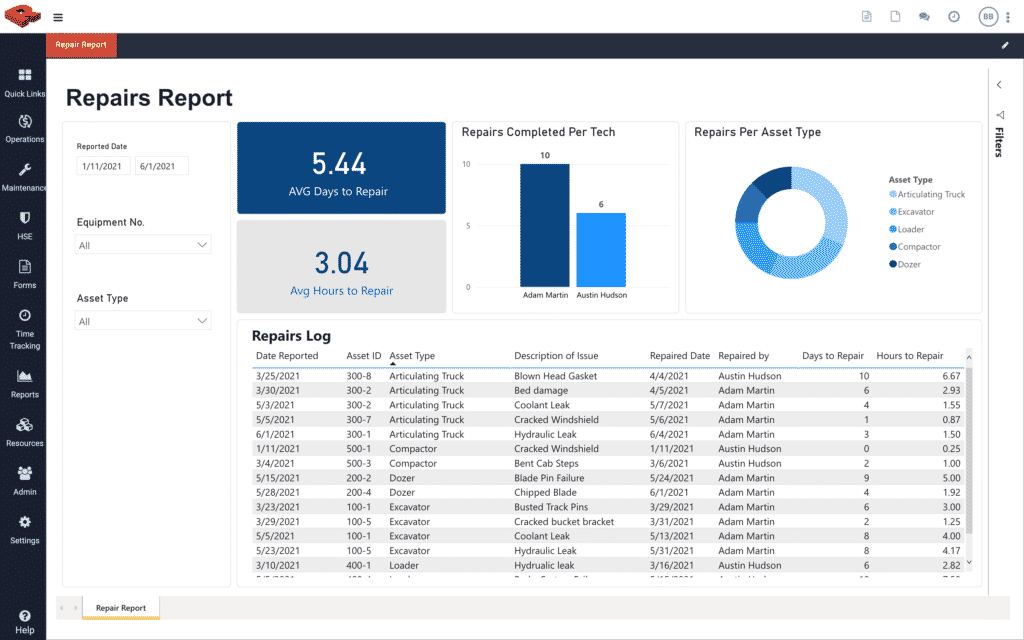
Reducing Backlog with Redlist
Measuring or analyzing your backlog is far more difficult with paper work orders than with Enterprise Asset Management (EAM) software. Redlist enables you to view your backlog at a high level or hone in on the backlog for specific assets. Additionally, all of the reports are auto-populated with real-time, current information. This means you can quickly see your total backlog and make an informed decision about how to reduce it. Also, you can set up automated reminders to go to you and your team members when work orders are overdue.
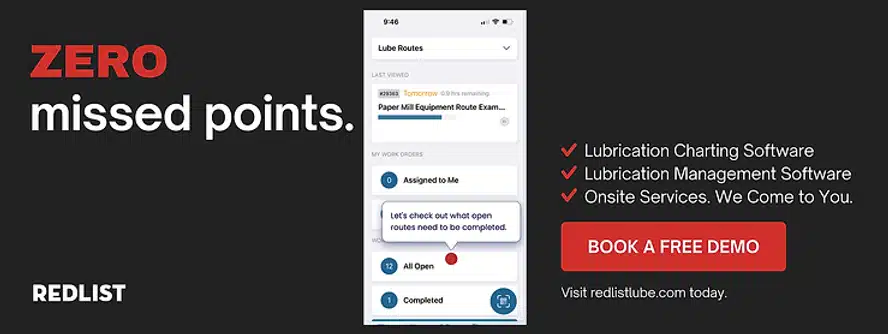
Prevent Future Backlog by Preventing the Cause
Most importantly, reducing maintenance backlog will be an endless cycle for you if you don’t determine the root cause and take action to prevent it. For example, if the majority of your backlog is caused by not having the right parts on hand, then you should make a plan to improve your spare parts management. If most of your backlog is from scheduling issues, then Redlist’s EAM will help you better forecast the staff, vendors, and parts needed to perform the scheduled work.
Alternatively, if your backlog happens because technicians seem to run out of time in the day, then you will want to look at how you’re scheduling maintenance. Redlist’s work orders module allows you to set the expected time to complete the work order and cross-reference with the recorded time it took. This may lead you to discover opportunities for more training, providing more details in work orders, or that you can eliminate some unnecessary preventive maintenance.
Many factors can lead to a maintenance backlog, and the cause may differ over time based on your business. Creating or improving your systems for planning, scheduling, inventory, and work orders are essential to reduce your backlog. Redlist makes it easier to see the data, make a plan, put systems in place, and audit for continual improvement.