There’s no doubt that viscosity is a critical topic when it comes to lubricating oils. We have even written several posts about this topic, which you can find here. In this post, you’ll read all the essential information on high viscosity and its importance in lubricating oils and maintenance management.
What is Viscosity?
Let’s start by defining viscosity. Viscosity is simply how thick or thin a flowing material is. In technical terms, viscosity is a fluid’s resistance to flow. A fluid with high viscosity has high resistance to flow, making it appear thick or less flowy. A fluid with low viscosity is the opposite. To illustrate, honey would be a high-viscosity substance and water would be a low-viscosity substance.
The Many Factors that Impact Viscosity
Although viscosity is a simple concept on paper, understanding it can be challenging when we consider the factors that can affect it. Viscosity can change according to the following factors:
1. Temperature
In general, viscosity decreases with increasing temperature. At high temperatures, fluid molecules gain more energy, are less bound together, and are more likely to flow. Lubricants available on the market come with temperature-viscosity charts that help users identify the expected viscosity at certain temperatures. Similarly, machines can also come with the manufacturer’s lubricant viscosity recommendations according to certain operating conditions.
2. Pressure
The effect of pressure on the viscosity of fluids is often overlooked because changes in pressure almost always come with temperature changes. However, the effect of pressure on viscosity can be independent of temperature. Typically, an increase in pressure increases the fluid viscosity.
Regular lubricating oils and greases react differently to pressure. Lubricating oils flow more freely with increasing pressure while greases only change in viscosity once a certain pressure is reached.
3. Shear Rate
Shear rate is the measure of how fast a fluid is being deformed. A fluid is said to have reached ‘shear’ when it permanently loses its viscosity. A lubricant’s resistance to loss of viscosity due to deformation is called its shear stability.
Exposure to high shear conditions does not have a significant effect on the viscosity of regular lubricating oils. For greases and high-viscosity lubricants, however, high shear rates can cause a remarkable decrease in viscosity
4. Inherent Properties
Inherent properties include the fluid type, composition, additives, etc. that can influence viscosity. In lubricants, the type of base oil determines the viscosity of the product. This viscosity can further change according to the other ingredients and additives mixed into this base oil. Special additives such as viscosity index improvers can add stability to lubricants, which helps them maintain their viscosity with changes in temperature, pressure, etc.
5. Contaminants
Exposure to contamination can increase or decrease the viscosity of a fluid. If lubricants are exposed to water or dirt, these can react with oil components and result in chemical by-products that thicken the oil. On the other hand, viscosity-stabilizing additives in the lubricant can react with contaminants, promoting drastic viscosity loss at high temperatures.
How High Viscosity Lubricants Work
Now you know what affects viscosity, let’s discuss high-viscosity lubricating oils. What are they, and how do they work? High viscosity in a lubricant is desirable when the application is:
- Heavy-duty
- Requiring high loads
- Reaches high operating temperatures
Heavy-duty engine oils, greases, and gear oils are some common examples of high-viscosity lubricants for these applications. Below are the ways high viscosity is essential to lubrication under heavy-duty applications:
Maintains Protective Boundary
The viscosity of the lubricant should be high enough to form a protective film between surfaces. This protective boundary must be maintained during operations to reduce the friction between said surfaces. Reduced friction means less wear and tear and less heat, which can reduce viscosity.
Increases Load Capacity
The use of a high-viscosity lubricant results in a thick and stable protective film between surfaces. In turn, this increases the load-bearing capacity of the machine. This means that the more viscous and stable the lubricant, the more operational load the machine can carry and support.
Protects from Contaminants
High-viscosity lubricants can provide better protection from contaminants. As metal debris, dirt, moisture, etc. are released during operations, a high-viscosity lubricant can collect and trap these better than a low-viscosity one. Thus, contaminants can be removed and prevented from causing damage to the surfaces of machines. High-viscosity lubricants can also be used as sealants to seal off gaps that allow the entry of contaminants into the system.
Stable Against High Temperatures
High-viscosity lubricants are inherently stable against temperature changes. Drastic temperature changes are often experienced by heavy-duty machines operating in cold climates. Applications such as these can benefit greatly from using high-viscosity lubricants because they provide effective lubrication at a wide range of temperatures.
High Viscosity Challenges
The many benefits of high-viscosity lubricants do not come without some challenges. For one, the use of high-viscosity lubricants does not guarantee success in heavy-duty applications. Your operating conditions, specific lubricant composition, lubrication practices, and other factors can reduce the lubricating effect of high-viscosity lubricants. Furthermore, there is no one high-viscosity lubricant that is ideal for all applications.
What works for one machine or process does not always mean it will work on another. Also, using a lubricant that is too viscous can increase energy consumption and introduce too much strain on a machine, shortening its lifespan. Finally, high-viscosity lubricants also come at higher prices and are costly to store and use.
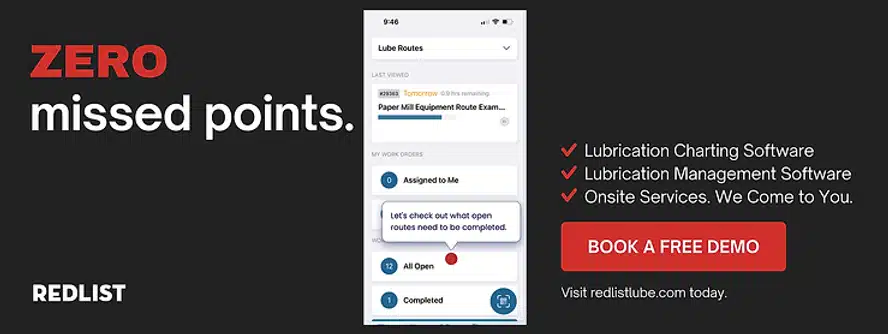
Managing High Viscosity and Lubricant Selection with a Lubrication Management Software from Redlist
The use of lubricating oils, whether of low or high viscosity, should be one part informed selection and the other part, trial-and-error. Under informed selection, you review the lubricant properties, consider the manufacturers’ recommendations, evaluate your unique requirements and processes, and from these select the lubricants to use. The lubricants you select should then be subjected to trial-and-error, where you use them and monitor their performance. And then, from these results, improve your lubrication process or replace your lubricants.

This is where Redlist’s Lubrication Management Software becomes valuable in lubrication. Redlist lets you keep organized files of information on your assets and their relevant lubrication details. Thus, you create a database you can easily reference the next time you are selecting new lubricants to use. It can also let you keep track of lubricant performance in a more detailed and accurate way.
And the valuable insights from lubrication performance can help you make improvements in selecting your lubricant or optimizing your lubrication process. To learn more about the benefits of Redlist, schedule your free demo with our experts today!