A rotating machine with a well-greased bearing will last much longer than one without proper lubrication. However, if you’re not careful, you can easily make mistakes that will cause premature bearing failure. When a bearing fails, it can be catastrophic for a business. Not only is there the cost of repairing or replacing the bearing, but there’s also the downtime that comes with it. In many cases, the failure could have been prevented if the correct lubrication techniques had been used. In this blog post, we’ll discuss some of the most common bearing lubrication mistakes and how to avoid them.
Problem #1: Greased Bearing Buildup
Considering that bearings need lubrication, it may come as a shock when regreasing results in a sudden-death bearing failure. The issue is when new grease enters a bearing that is either infrequently greased or excessively greased. This allows time for the soap-based thickener to separate from the oil and create a dry buildup. Heat, lengthy relube intervals, over-lubrication, and aged bearings are the main causes of this greased bearing buildup. Other elements include grease quality, vibration, centrifugal forces, contamination, pressure, and the relubrication process. Furthermore, particle contaminants such as wear particles, dust, dirt, and debris can gather with the dried thickener to form a wall of sorts in your equipment.
Now, these dry remains of the previous grease and particles are pushed aside as the fresh grease enters. But, the danger comes from the pressure of new grease sending this rock-like formation into the bearing track. A grease gun can exert hydrostatic pressures over 15,000 psi, which is more than enough to do exactly that. In some cases, the obstruction actually keeps the fresh grease from reaching the bearing altogether. While you think you’re sufficiently lubricating your bearing, it may be in there dying of lubricant starvation.
If you use supply pipes instead of a grease gun, especially to lubricate big bearings, then you’re not in the clear either. Over time, rust, hardened thickener, and other substances may accumulate in these pipes. The fresh grease acts as a plunger during relubrication, pushing the particles into the bearing cavity below.
Problem #2: You Have Always Greased Bearings Based on Time Not Condition
It may seem reasonable to lubricate a bearing once a week or once a month. Performing scheduled maintenance at regular intervals is a well-known and accepted practice. There is only one reason why grease is needed in bearings, to reduce friction. If the lubricant is still serving that need, it isn’t always necessary to change it or add more. Despite this, many organizations do exactly that because the calendar says so, sometimes with catastrophic results. In the age of sensors and condition monitoring technology, lubricating a bearing on a time basis is a mistake.
Because the main function of lubrication is to lower friction, it makes sense that monitoring friction levels, rather than time in service, is the best way to assess a machine’s lubrication requirement. You can achieve a large decrease in grease usage via condition monitoring and lubrication management optimization.
Problem #3: Lubricating Bearings Too Much or Not Enough
Both under and over-lubrication can result in equipment failure.
An excessive amount of grease creates pressure on the rolling components against the outer race and through the fluid film. To force their way through the mountain of grease, the bearings must now exert much more effort. Additionally, too much grease causes higher friction and pressure, which raises the operating temperature. Overheating could reduce the lubricant’s efficiency and cause the oil to split from the thickener.
A similar impact results from not adding enough grease. Friction, temperature, and component wear all increase with a shortage of lubrication. You can use condition monitoring while lubricating to help determine the correct amount of grease. For example, you can use ultrasound to measure the amount of friction in the machine, stopping between each pump of grease to confirm if the friction level dropped.
Problem #4: Unreliable Sensor Data
If you listen to a bearing with an ultrasound device without measurement feedback, you are setting yourself up for failure. Using audible feedback alone is not enough to make a comparative conclusion. Every person hears things differently, and it’s impossible to remember what the bearing sounded like a month ago. When precise quantifiable data is available, don’t rely solely on subjective ultrasound noise. Therefore, it is best to always use ultrasound instruments with digital decibel meters. It would be even better if you used a device that provided multiple condition indicators.
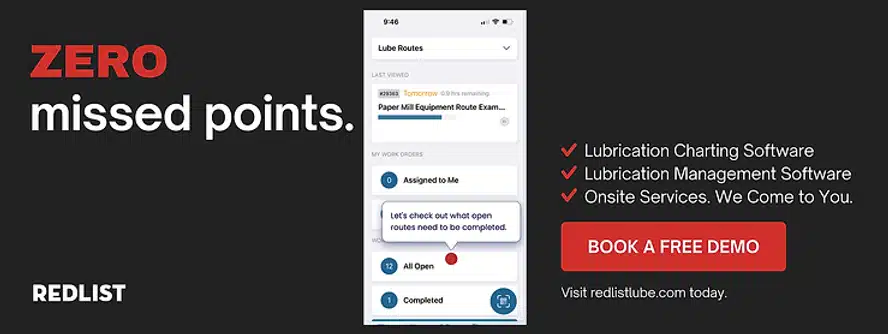
Unexpected Benefits of Greased Bearing Success
A properly lubricated machine consumes less energy. So, not only will you potentially reduce your grease usage, but also you’ll lower your energy bills. Furthermore, a machine that runs cooler and consumes less electricity will last longer. Precision and skill are necessary for world-class lubrication. A good education and training program can develop top-notch lubrication skills and prolong the lifespan of greased bearings.