There are plenty of statistics about the cost of asset downtime and plenty of metrics to measure it. But, how do you translate those metrics into impactful action to decrease downtime? FRACAS is the answer, so add it to your list of maintenance acronyms.
FRACAS: Failure Reporting Analysis and Corrective Action System
We find that a lot of organizations have one or two pieces of this system already. You’re likely collecting maintenance data, but maybe you don’t have a strategic plan for analyzing the reports. Alternatively, you may be analyzing what you can and taking action. However, if your failure reporting isn’t systematic, you might be making decisions based on inaccurate or incomplete data. So, FRACAS comes down to making sure the pieces you have are streamlined and building out processes for the rest. The easiest way to define FRACAS, its benefit, and how to implement it is to break it down.
Failure Reporting
Reporting actually starts with collecting thorough, accurate data. It may never be perfect because there is always the potential for human error. But, you can take steps to make your data as trustworthy as possible. Technicians need time and an easy system, so digitizing your data collection is the best way to meet both of those needs. Redlist’s mobile app allows you to configure the modules to gather the data you need on any device. When your maintenance team completes work orders, data input is quick and easy. This ensures they don’t put it off until they have time later in the day, which results in more accurate information.
The second step of reporting is consistency. Not consistency as in how often you generate reports, but consistency in your data. If you create a set of failure codes that technicians can use, then you can better see asset failure trends. Without consistency, you could still find the trends, but it takes more work to analyze.
The final step of FRACAS reporting is generating the reports. Redlist’s reporting dashboard auto-populates with your data, making it incredibly easy to generate the reports you want. You can check the status of your failure metrics and improvements without the need for hours of data entry. To have the most effective FRACAS, you want to make it as easy as you can. Even though FRACAS offers a great long-term benefit, many organizations struggle to dedicate the time needed if it requires a lot of labor to do.
Failure Analysis
The biggest chunk of work is done with the data collection and reporting. If you’ve built a strong foundation in that step, failure analysis should be pretty smooth. We recommend starting with work order analysis and ending with root cause analysis.
Your work orders will guide you to the trends, but there are a few approaches you can take. You could begin with analyzing work orders for your most critical or most valuable assets. These assets would be anything that has a large impact on production costs when it breaks down or assets that cost the most to repair. Once you’ve completed the FRACAS loop on those assets, you can move on to assets that are less mission-critical and less expensive.
Next, perform a root cause analysis. Talk to your team and dig deep to get to the true root cause of the failures. This is the only way to determine the most effective corrective action to take. To learn from asset failure, you have to know what caused it.
Failure Correction
To round out the FRACAS loop, we have failure correction. Each step is only as strong as the one before it, meaning your corrective actions depend entirely on the accuracy of your data and the depth of your analysis. However, FRACAS is a constant cycle that allows you to report, analyze, and continue to refine your corrections. Your first analysis gives you a baseline metric to compare future data to. So, don’t worry too much about getting it perfect on the first try. You may find that the failure code is happening just as frequently as before your corrective action. That is simply a sign to go deeper on your root cause analysis to hone your corrective action plan. Ideally, each of these steps moves you closer to eliminating asset downtime even if it is one small change at a time.
Ultimately, you may find some issues that you can’t really change, such as aging assets. The corrective action, in that case, would be analyzing the total cost of ownership and potentially replacing the asset. It may be more cost-effective to replace the asset, as the repairs and the impact of downtime costs add up.
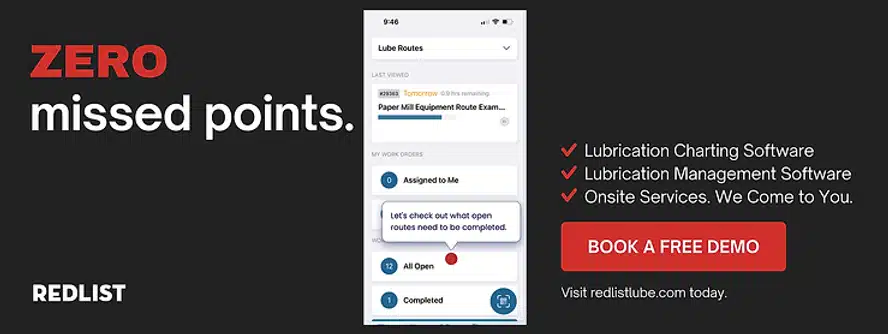
Pulling Value from FRACAS
Creating a FRACAS shifts your perspective on failure to pull real value from it. While it is a commitment, the potential for long-term return on investment is worth it. When you make it part of your maintenance culture, everyone can play a role in the system. Data is important and analysis is important. But, without people to provide accurate data and carry out the corrective actions, you can’t make impactful change. The easiest way to tackle FRACAS implementation is to start small and include your technicians every step of the way. Redlist is here to support you by streamlining those steps for the best results.